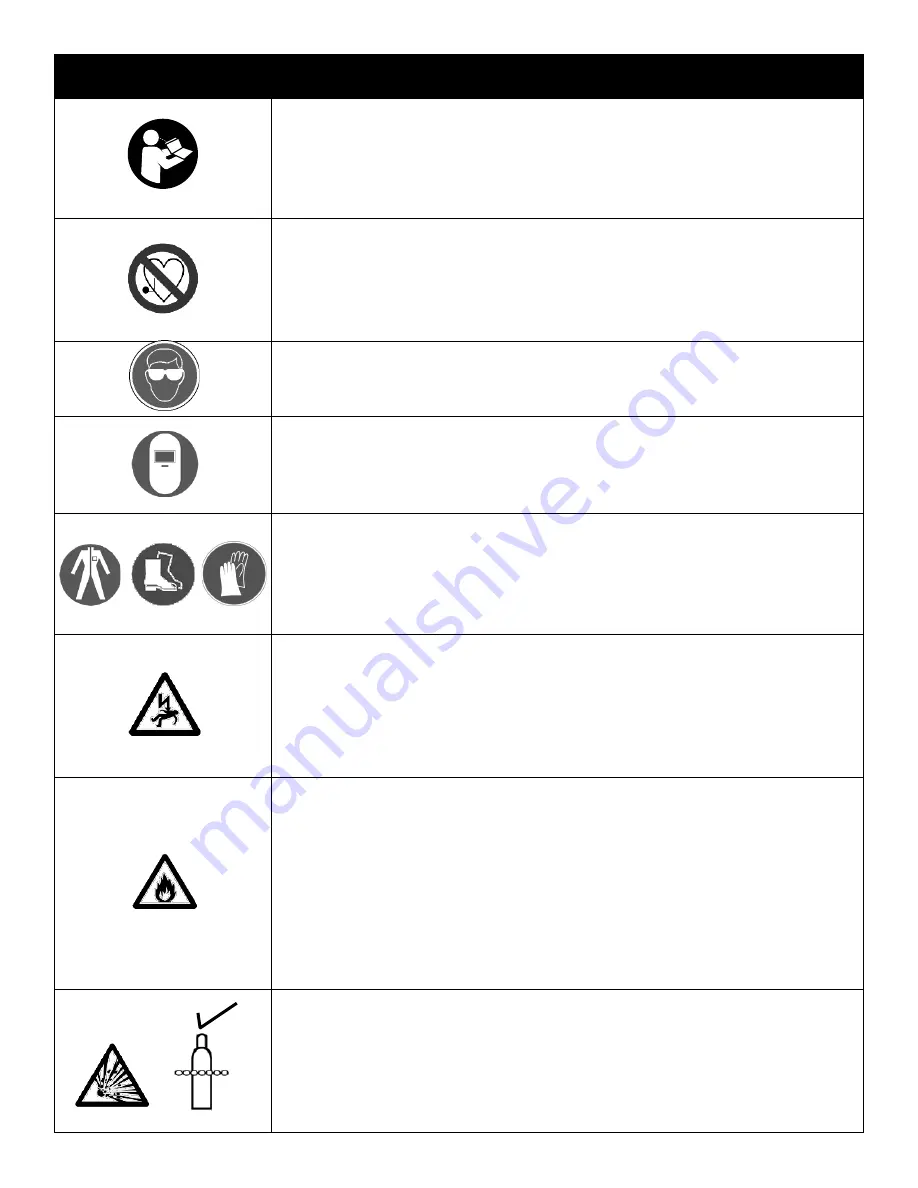
7
Safety Warnings, Dangers, Cautions and Instructions
NOTICE. This unit manual is intended for users with basic knowledge and skillset in weld-
ing. It is your responsibility to make certain that the use of this welder is restricted to per-
sons who have read, understand and follow the warnings and instructions in this manual. If
you or the operator needs further instruction, contact Everlast welding support at 1
-
877 755
-
9353 ext. 204 or seek qualified professional advice and training.
WARNING! High Frequency (HF) energy can interfere with the operation of pacemakers and
can damage pacemakers. Consult with your physician and pacemaker manufacturer
before
entering an area where welding and cutting equipment is in operation and
before
using this
welder. Some pacemakers have limited shielding. Alert any users or customers of this po-
tential problem.
WARNING! Use approved safety glasses with wrap around shields and sides while welding
and working in the weld area or serious eye damage or loss of vision may result. Use a
grinding shield in addition to the safety glasses during chipping and grinding operations.
WARNING! When welding always use an approved welding helmet or shielding device
equipped with at least an equivalent of a shade 9 or greater. Increase the shade number
rating as amperage increase over 100 amps. Inspect helmet for cracks in lenses and in the
helmet. Keep lens covers in good condition and replace as necessary.
WARNING! Welding/cutting operations carry inherent risks which include but not limited to
possible cuts burns, electrical shocks, lung damage, eye damage and even death. Take all
appropriate measures to use proper Personal Protective Equipment (PPE). Always use
leather welding gloves, closed toe (preferably reinforced or steel toe leather shoes, and long
-
sleeved flame resistant clothing (i.e. denim). Do not wear Poly/Nylon blend materials.
DANGER! Welding/cutting poses shock and electrocution risks. Keep this welding equip-
ment dry. Do not weld in the rain or where moisture accumulates. Use dry, rubber soled
shoes, gloves and clothing when welding. Do not rest or contact work clamp (ground) when
welding. Keep all parts of the body insulated from the part being welded when possible. Do
not touch terminals or connections while the unit is on. Consider all parts to be
“
live
”
at all
times even if no live work is being performed. Do not use frayed welding cables.
CAUTION! Fires are possible but also preventable while welding. Always remove flammable
rags, papers, and other materials from the weld area. Keep rags stored in an approved flame
proof canister. Keep a fully charged fire extinguisher at hand. Remove any fuels, oils,
paint, pressurized spray cans, and chemicals from the weld area. Make sure any smoke/fire
detectors are function properly. Do not weld on tanks, drums or barrels, especially if pres-
surized or sealed. Do not weld on any container that previously held fuel or chemicals.
Make sure the weld area is clear of flammable materials such as grass or wood shavings
solvents and fuels. Do not wear frayed or loose clothing. Visually inspect and recheck the
work area after welding looking for smoldering debris or flames.
WARNING! Welding gas cylinders are under high pressure. Keep all gas cylinders upright
and chained to a cart or held safely in a safety holding pen. Never transport gas cylinders
in an enclosed car van or other vehicle. Transport gas cylinders securely. Keep all cylin-
ders capped while not in use or during transport. Replace the cap on the cylinder when it
is going to be more than 24 hours before use. Do not use or attempt to repair faulty regu-
lators. Never weld on gas cylinders. Keep gas cylinders away from direct sparks.