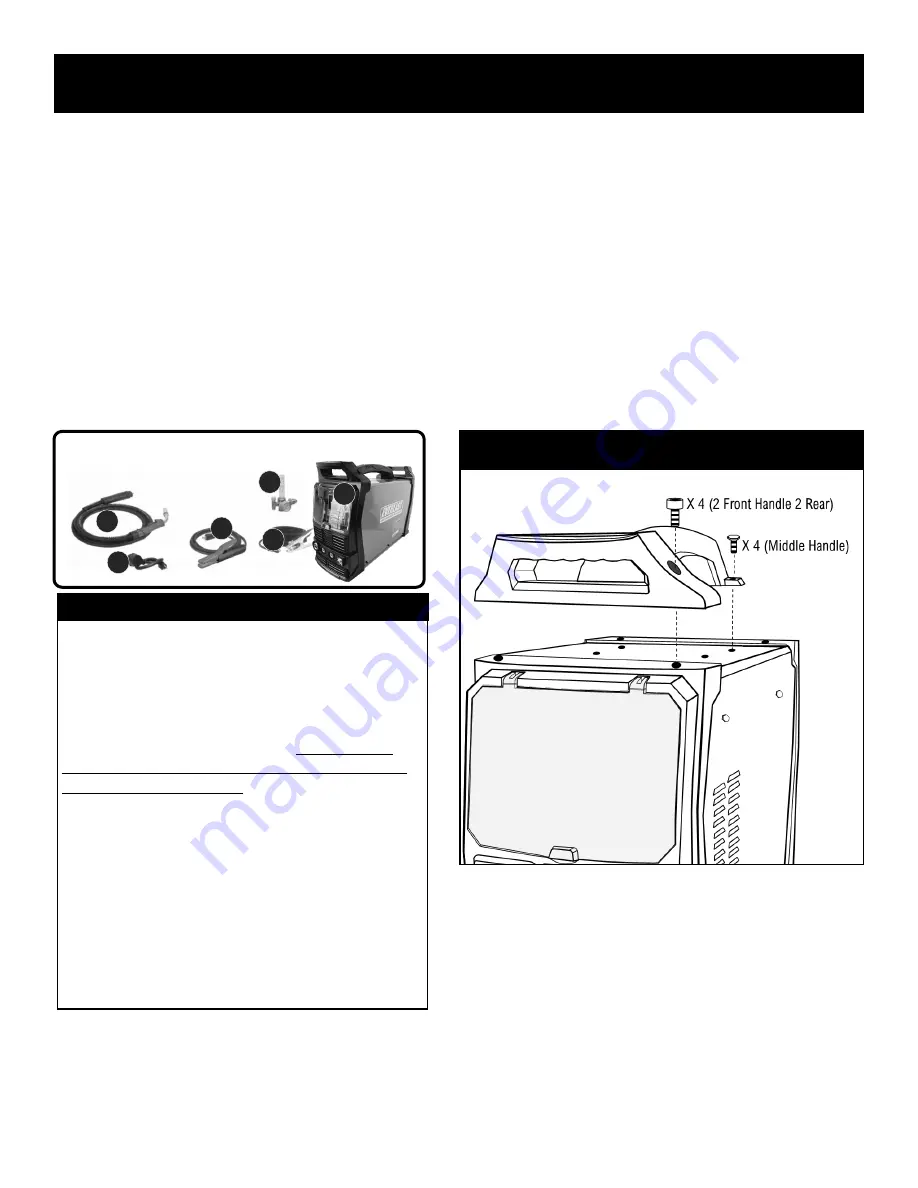
14
Setup Guide
Getting Started
UNPACK YOUR UNIT.
Upon arrival, you will need to completely unpack your unit, and check
things over. This is a time sensitive matter. Do not delay or hold the
welder unopened in the box. First, make sure the unit is opened from
the top. Be careful with using knives and sharp objects so you won
’
t
cut cords and cables inside the boxes. Lay all items out and inspect
them.
You should have the following in your box:
1.
Cyclone 212 MIG/Stick welder (bare unit).
2.
Floating Ball Regulator for MIG. (hose included but not pictured).
3.
15 Series MIG Gun/Torch. (MB15AK style)
4.
250A Work Clamp (approx. 9.5 ft with cable).
5.
250A Stick Electrode Holder (approx. 9.5 ft with cable).
6.
240V to 120V power cord adapter.
INSPECT AND ASSEMBLE YOUR UNIT.
When you receive your package, inspect the unit for damage. Check for
the presence and general condition of the accessories. Some slight
rubbing or chaffing of some of the accessories may be present, but this
is considered normal. Most notably, the MIG torch may appear to be
NOTICE:
This unit includes an additional
.030”
MIG contact Tip (it may also
include a
.023”
but may vary by region) but does not contain any
other MIG consumables, including filler (MIG or Flux
-
Cored) wire.
Additional sizes of contact tips, nozzles and basic gun parts are
available direct from Everlast
’
s website, from other online sources
and may be also available locally at welding supply stores that carry
parts for similar MB15AK styled MIG guns.
Additionally, some
miscellaneous parts like a contact tip wrench may be found in the
box, depending upon your region.
Filler (MIG and Flux
-
Cored)
wire should be purchased locally or direct from other online
sources. Other drive roll sizes and types should be purchased direct
from Everlast. The included drive roll is a V groove drive roll, de-
signed for solid steel wire
.035”
and
.030”
wire. For flux core or
aluminum use, you must purchase the correct type for proper wire
feeding. See more drive roll information found later in this manual.
NOTE: If you think you are missing a needed part, check the con-
sumable kit bag and box before calling Everlast for replacement. If
you are missing parts, call 1
-
877
-
755
-
9353 ext. 206 for help. (Only
in the USA, for other areas, contact the distributor in your region).
used or fired. This is because it has been live tested in the factory for
proper operation before putting into the box. If any item is damaged or
missing, please inform Everlast within 72 hours of product receipt. See
pages 4 and 5 for more details. Assemble the front, middle and rear
handles with the supplied screws. Use a 5mm hex key to tighten the
socket head cap screws to the front and rear handles. (Screws may be
found in the consumable bag.) Remove the cap screws from the center
of the machine and install the center, long handle. Use a Phillips type
screw driver to tight the screws, or alternately use a 10mm socket and
1/4”
drive socket wrench to tighten the screws. IMPORTANT! Do not
overtighten the screws.
If desired for proper fitment or for space saving,
the unit may be used without the handles. However, install the screws
and tighten them to the panels anyway. Do not leave them out. Be sure
to reinstall the handles if the unit is to be carried or lifted. Do not lift
from any other point on the machine or damage may occur.
POWER UP AND TEST YOUR UNIT.
You will need to fully test the unit as soon as possible. Within 72 hours
after receipt of the unit, be sure to have every thing you need at hand to
test the unit. Make sure the correct input power, wiring, and plug con-
figuration is being used. Make sure you have the regulator is installed
(See following section). Then, power up your machine without any ac-
cessories installed. Allow the unit to idle for 15 minutes. Check and
observe operation of knobs, controls and buttons, cycling through each
as required. Make sure the fan is running at full speed. After the static
running test is completed, turn the unit off, connect the torches and
cables. Then, conduct live testing of all the functions and features of the
machine. For testing make sure work clamp is connected directly to the
part being welded (work). Check for arc starting and stability. If you are
testing the unit on 120V, maximum output will be reduced. If any weld-
1
2
5
3
6
Cyclone 212
4
ASSEMBLE THE HANDLES