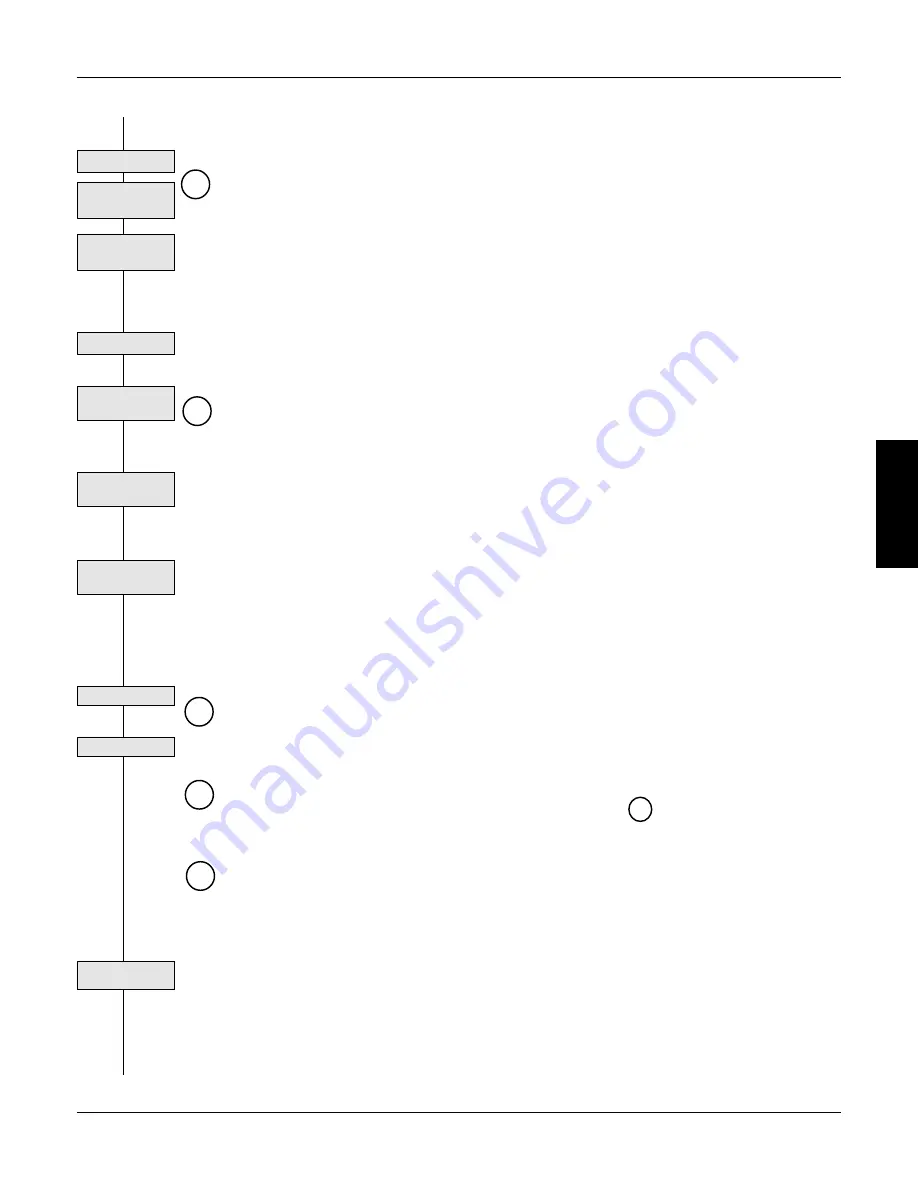
Chapter 3 Installation and Wiring
3 - 7
3
590 DRV Digital DC Drive Product Manual
Current Limit
For most applications, connect terminal A6 (ANALOG INPUT 5) to terminal B3 (+10 VDC REFER-
ENCE) and connect terminal A5 (ANALOG INPUT 4) to terminal B4 (-10 VDC REFERENCE).
This sets the drive's positive and negative current limit clamps to +100% and -100% respectively for
forward and reverse motor operation and allows you to adjust the MAIN CURRENT LIMIT param-
eter from 0 to 200%. If you need to control the main current limit externally, connect a 10k
W
potentiometer between terminal B3 (+10 VDC REFERENCE) and terminal B1 (0 VDC). Connect the
wiper to terminal A6. You can then adjust the current limit from 0 to 200% if SETUP PARAM-
ETERS:: CURRENT LOOP::MAIN CURR. LIMIT is set to 200.00%.
Speed Demand
For normal operation, connect the speed demand signal to terminal A4 (RAMP SETPOINT). This
input is scaled so that +10 VDC input equals maximum forward speed demand (+100%), and –10
VDC input equals maximum reverse speed demand (–100%).
Connect the ends of an external 10k
W
potentiometer to terminal B3 (+10 VDC REFERENCE) and
terminal B4 (–10 VDC REFERENCE) and the wiper to terminal A4. For non-reversing applications,
the speed demand needs only to operate between 0 and +10 VDC. Connect the high, or clockwise end
of the potentiometer to B3 and the low or counterclockwise end to the 0 VDC terminal, A1 (SIGNAL
GROUND).
Terminal A2 (SPEED SETPOINT NO. 1) is an additional, non-ramped speed demand input which
sums with the drive's other speed inputs. Connect your speed demand to this terminal for non-ramped
speed control.
Terminal A3 (SPEED SETPOINT NO. 2 or CURRENT DEMAND) is a hardwired input which
functions either as a non-ramped speed or current demand. The state of control terminal C8 (I DMD.
ISOLATE) determines the operating mode of the input. When tied to +24 VDC (terminal C9), A3 is
a direct current demand input to the drive's current loop. When terminal C8 is left open-circuited, A3
is a non-ramped speed demand input and sums with the other drive speed loop inputs.
Start/Stop Input
Connecting terminal C9 through a normally-open contact to terminal C3 (RUN) provides normal start/
stop control. When the contact is open, the drive will attempt to perform a controlled stop; when it is
closed, the drive will start.
Jog Input
Terminal C4 (JOG) is connected through a normally-open contact to terminal C9 for jog applications.
Interlock the jog relay contact with the run relay coils as shown at
in Figure 3.20.
Armature Current Feedback Terminal
You can connect a meter to terminal A9 (ARMATURE CURRENT) to monitor the motor DC
armature current. The output is hardwired and not software configurable. Refer to Appendix A for
the terminal's output rating and signal scaling. This connection is optional.
Speed Feedback
The 590 DRV Digital drive accepts the following types of speed feedback signals:
• armature voltage feedback
• analog AC or DC tachometer generator feedback
• wire-ended electrical encoder feedback
• plastic (5701) or glass (5901) fiber optic Microtach encoder feedback.
Current Limit
A6 to +10 VDC
(B3)
A5 to -10 VDC
(B4)
Speed/Current
Input (A3)
Non-ramped
Setpoint (A2)
Ramped Setpoint
(A4)
Speed Inputs
Start (C5)
Jog (C4)
K
L
M
N
Feedback Options
▼
▼
O
I
Summary of Contents for 590 DRV Digital
Page 2: ......
Page 16: ...1 4 Chapter 1 Introduction 1 590 DRV Digital DC Drive Product Manual ...
Page 22: ...2 6 2 Chapter 2 Identification 590 DRV Digital DC Drive Product Manual ...
Page 45: ...Figure 3 20 Wiring Circuit Diagram for 590 DRV Digital Drive ...
Page 77: ...5 22 5 590 DRV Digital DC Drive Product Manual Chapter 5 Troubleshooting ...
Page 103: ...App A 18 A Appendix A Technical Description 590 DRV Digital DC Drive Product Manual ...
Page 107: ...B Appendix B Using the Man Machine Interface App B 4 590 DRV Digital DC Drive Product Manual ...
Page 149: ...Appendix C Setup Parameters 590 DRV Digital DC Drive Product Manual App C 42 C ...
Page 173: ...Appendix D I O Configuration System Menu App D 24 D 590 DRV Digital DC Drive Product Manual ...
Page 174: ...Figure D 20 590 DRV Digital DC Drive Software Block Diagram t t t t ...
Page 202: ...App F 18 Appendix F Spare Parts List 590 DRV Digital DC Drive Product Manual F ...
Page 208: ...Appendix G RS232 System Port P3 590 DRV Digital DC Drive Product Manual App G 6 G ...
Page 250: ...Appendix J Parameter List by Menu App J 8 J 590 DRV Digital DC Drive Product Manual ...
Page 258: ...Appendix K Parameter List by Parameter Name 590 DRV Digtial DC Drive Product Manual App K 8 K ...