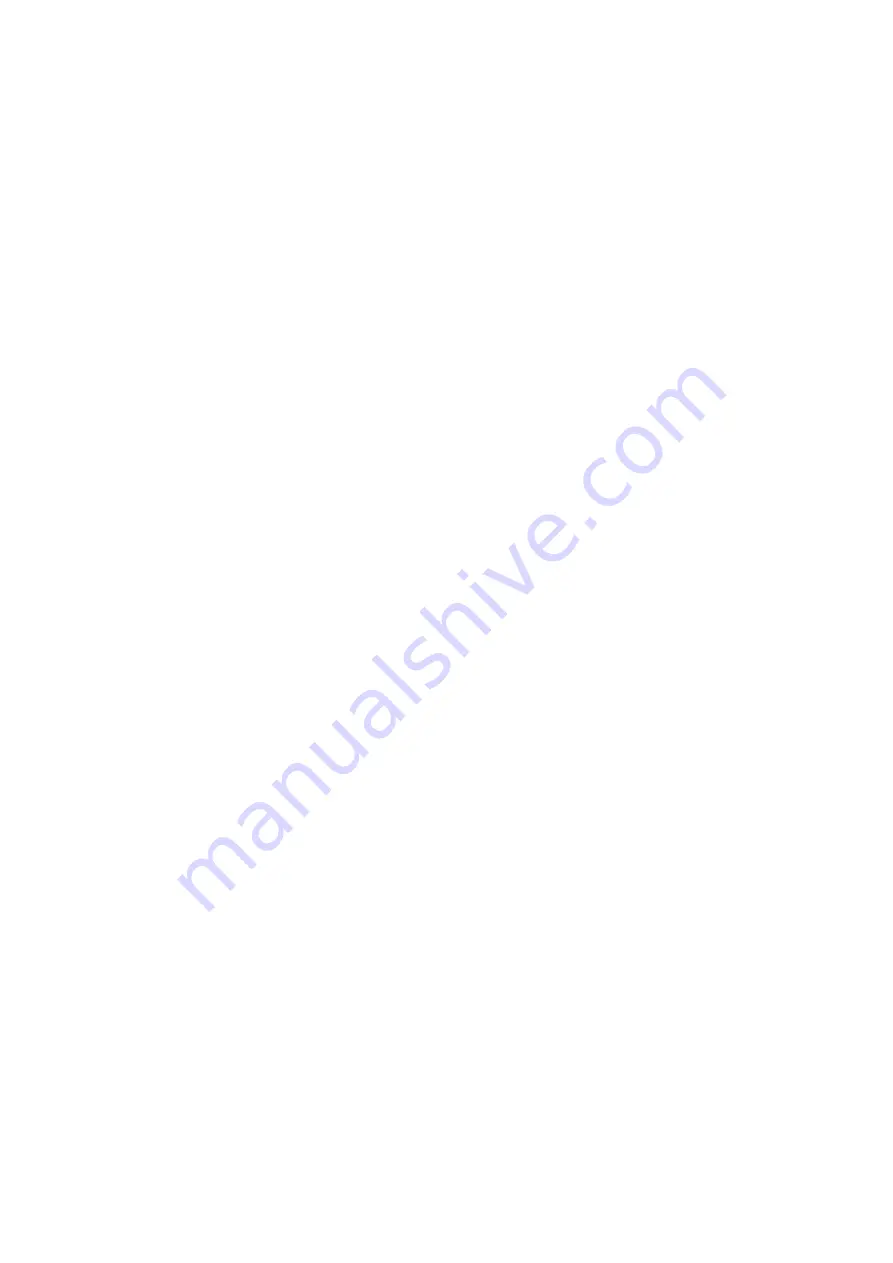
13
3.2 Prior to use
Please make sure that the contacting surface for the magnet is level, clean and rust-free.
Remove any varnish or primer. When working on materials that are not magnetizable, suitable
fixation devices, obtainable as accessories from EUROBOOR, e. g. suction plate, vacuum plate or
pipe-drilling device must be used.
When work on steel materials with a material thickness of less than 3,5 mm, the work piece must
be reinforced with an additional steel plate in order to guarantee the magnetic holding power.
Check the machine for possible damage; Before using the machine, you must carefully check
protective devices or slightly damaged components to ensure they are operating perfectly and as
intended.
Check that moving are in perfect working order and do not jam and check whether parts are
damaged. All parts must be correctly installed and fulfill all conditions necessary to ensure perfect
operation of the machine.
Damaged protective devices and parts must be repaired or replaced according to specifications by
EUROBOOR of any authorized EUROBOOR dealer.
DO NOT use under wet conditions or in presence of flammable liquids or gases. This magnetic drilling
machine is a professional power tool.
DO NOT let children come into contact with the machine. Supervision is required when
inexperienced operators use this machine.
ELECTRICAL SAFETY
The electric motor has been designed for one voltage only. Always check that the power supply
corresponds to the voltage on the rating plate.
Your EUROBOOR MAGNETIC DRILLING MACHINE is designed in class I (grounded) according to
EN 61029-1. Earth wire is required.
If the supply cord is damaged, it must be replaced by a specially prepared cord available through the
EUROBOOR service organization.
EXTENSION CABLE
If an extension cable is required, use an approved 3-core extension cable suitable for the power input
of this tool (see technical data).The minimum conductor size is 1.5 mm²; the maximum length is 30
meter. When using a cable reel, always unwind the cable completely.
TRY A FEW SIMPLE PROJECTS USING SCRAP MATERIAL UNTIL YOU DEVELOP A “FEEL” FOR THE
MACHINE
LET THE MACHINE RUN IN FOR A PERIOD OF 8-10 HOURS BEFORE STARTING WITH BIG
OPERATIONS. DO NOT LOAD THE MACHINE TOO MUCH DURING RUN-IN PERIOD
NEVER USE THE MACHINE IN SERIOUS OVERLOAD
KEEP THE MACHINE CLEAR FROM MOISTURE AT ALL TIMES TO PROTECT THE MACHINE, YOURSELF
AND OTHERS.
Summary of Contents for TUBE.55-T
Page 31: ...31 8 Exploded view spare part list 8 1 Exploded view ...
Page 32: ...32 ...
Page 33: ...33 ...
Page 35: ...35 8 3 Wiring diagram ...