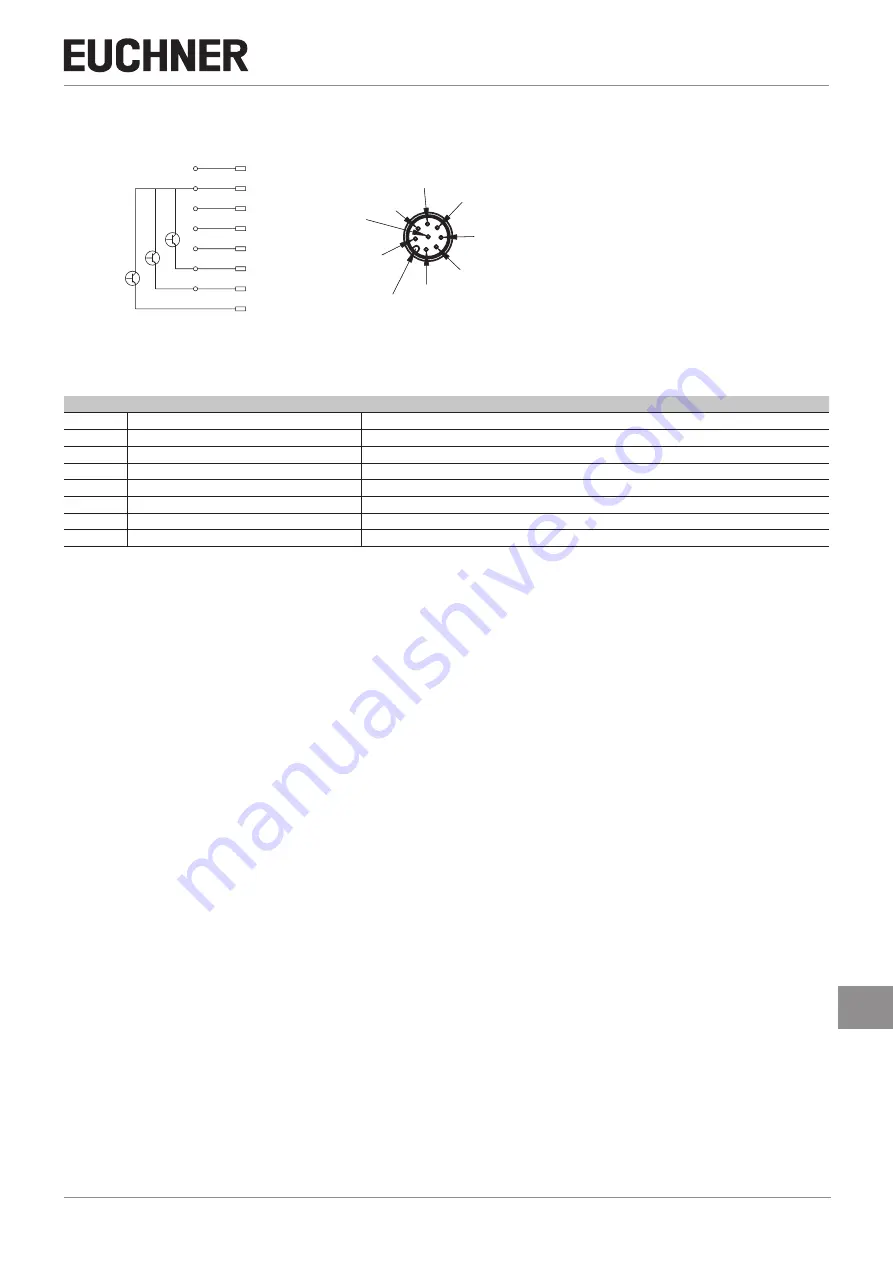
11
2510145-05-08/21 (translation of the original operating instructions)
Operating Instructions
Non-Contact Safety Switch CES-I-BR-.-C07-…
EN
8.5. Connector assignment of safety switch CES-I-BR
1
7
6
5
4
3
2
8
8
2
7
6
1
3
4
5
UB
0V
FI1A
FI1B
FO1A
FO1B
OD/C
nc
Coding lug
View of connection side on the safety switch
Fig. 1:
Connector assignment of safety switch CES-I-BR
Pin
Designation
Description
1
FI1B
Enable input, channel B
2
UB
Operating voltage, 24 V DC
3
FO1A
Safety output, channel A
4
FO1B
Safety output, channel B
5
OD/C
Door position monitoring output/communication
6
FI1A
Enable input, channel A
7
0V
Ground 0 V DC
8
nc
n.c.
8.6. Notes on operation with safe control systems
Observe the following requirements for connection to safe control systems:
Ì
Use a common power supply for the control system and the connected safety switches.
Ì
A pulsed power supply must not be used for U
B
. Tap the supply voltage directly from the power supply unit. If the power
supply is connected to a terminal of a safe control system, this output must provide sufficient electrical current.
Ì
Always connect inputs FI1A and FI1B directly to a power supply unit or to outputs FO1A and FO1B of another EUCHNER
BR device (series connection). Pulsed signals must not be present at inputs FI1A and FI1B.
Ì
The safety outputs FO1A and FO1B can be connected to the safe inputs of a control system. Prerequisite: The input
must be suitable for pulsed safety signals (OSSD signals, e.g. from light grids). The control system must tolerate test
pulses on the input signals. This normally can be set up by parameter assignment in the control system. Observe the
notes of the control system manufacturer. For the test pulse duration of your safety switch, refer to chapter
.
A detailed example of connecting and setting the parameters of the control system is available for many devices at
www.euchner.com, in the area
Downloads/Applications/CES
. The features of the respective device are dealt with there in
greater detail.
8.7. Connection without and with IO-Link communication
8.7.1. Connection without IO-Link communication
Only the safety and monitoring outputs are switched with this connection method.
With a series connection, the safety signals are looped through from device to device.
8.7.2. Connection with IO-Link communication
If, in addition to the safety function, detailed monitoring and diagnostic data are to be processed, a BR/IO-Link Gateway
is required. To poll the communication data from the connected device, communication connection C is routed to the BR/
IO-Link Gateway.
You will find further information in the operating instructions for your BR/IO-Link Gateway.