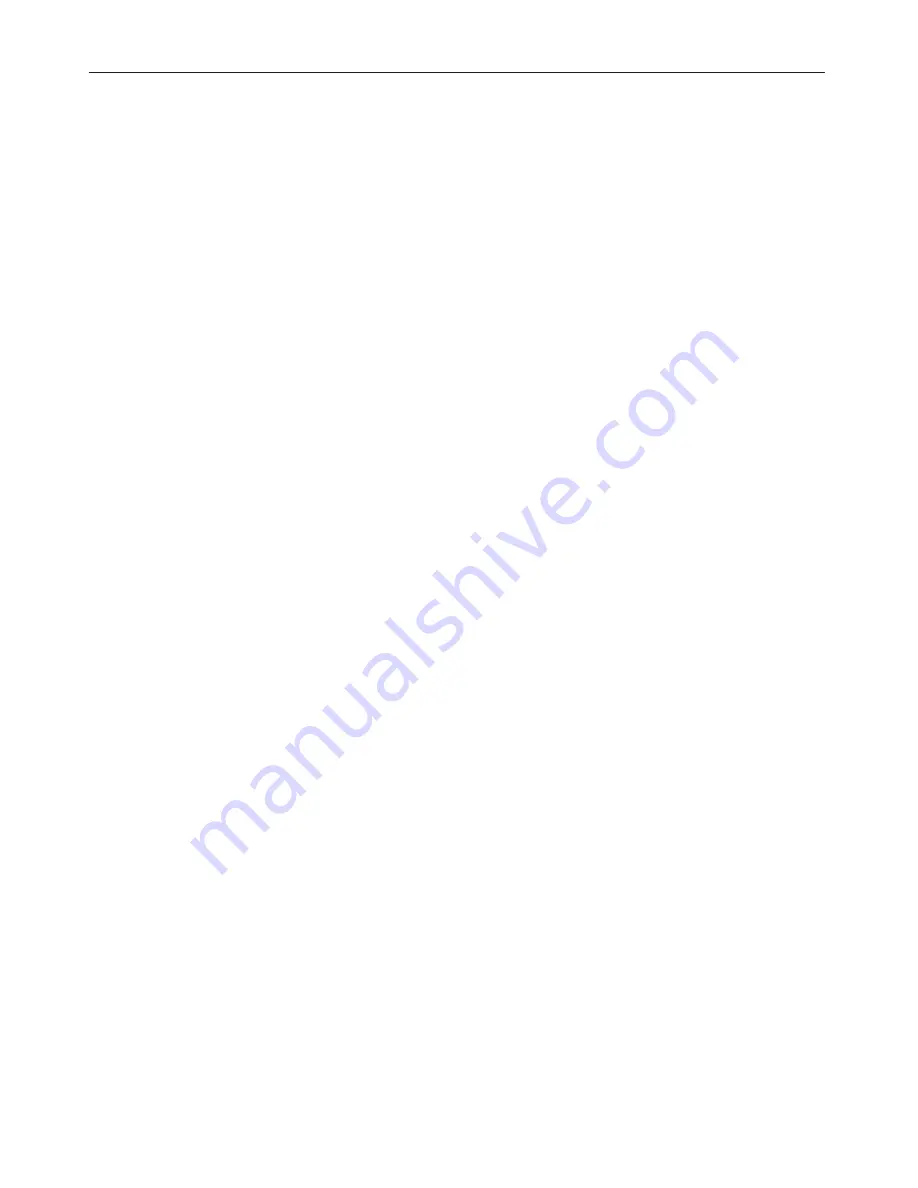
•
18
•
1.0 - HINTS AND WARNINGS
Please read the warning notices given in this section very carefully, because they provide important information
regarding safety in installation, use and maintenance of the pump.
• Keep this manual in a safe place, so that it will always be available for further consultation.
• The pump complies with EEC directives No.89/336 regarding "electromagnetic compatibility" and No.73/23
regarding "low voltages", as also the subsequent modification No.93/68.
N.B. The pump has been constructed in accordance with best practice. Both its life and it electrical and
mechanical reliability will be enhanced if it is correctly used and subjected to regular maintenance.
1.1 - WARNING:
Any intervention or repair to the internal parts of the pump must be carried out by qualified and authorized
personnel. The manufacturers decline all responsibility for the consequences of failure to respect this rule.
GUARANTEE: 1 year (the normal wearing parts are excluded, i.e.: valves, nipples, tube nuts, tubing, filter
and injection valve). Improper use of the equipment invalidates the above guarantee. The guarantee is ex-
factory or authorized distributors.
1.2 - SHIPPING AND TRANSPORTING THE PUMP
The pump should always be moved in a vertical (and never in a horizontal) position. No matter what the means
of transport employed, delivery of the pump, even when free to the purchaser's or the addressee's domicile, is
always at the purchaser's risk. Claims for any missing materials must be made within 10 (ten) days of arrival,
while claims for defective materials will be considered up to the 30th (thirtieth) day following receipt. Return of
pumps or other materials to us or the authorized distributor must be agreed beforehand with the responsible
personnel.
1.3 - PROPER USE OF THE PUMP
• The pump should be used only for the purpose for which it has been expressly designed, namely the dosing
of liquid additives. Any different use is to be considered improper and therefore dangerous.The pump should not
therefore be used for applications that were not allowed for in its design. In case of doubt, please contact our
offices for further information about the characteristics of the pump and its proper use.
The manufactures cannot be held responsible for damage deriving from improper, erroneous or unreasonable
use of the pump.
1.4 - RISKS
•
After unpacking the pump, make sure it is completely sound. In case of doubt, do not use the pump and con-
tact qualified personnel. The packing materials (especially bags made of plastics, polystyrene, etc.) should
be kept out of the reach of children: they constitute potential sources of danger.
• Before you connect the pump, make sure that the voltage ratings, etc., correspond to your particular power
supply. You will find these values on the rating plate attached to the pump.
• The electrical installation to which the pump is connected must comply with the standards and good prac-
tice rule in force in the country under consideration.
• Use of electrical equipment always implies observance of some basic rules: In particular:
1 - do not touch the equipment with wet or damp hands or feet;
2 - do not operate the pump with bare feet (Example: swimming pool equipment);
3 - do not leave the equipment exposed to the action of the atmospheric agents;
4 - do not allow the pump to be used by children or unskilled individuals without supervision;
• In case of breakdown or improper functioning of the pump, switch off, but do not touch. Contact our techni-
cal assistance for any necessary repairs and insist on the use of original spares. Failure to respect this con-
dition could render the pump unsafe for use.
• When you decide to make no further use of an installed pump, make sure to disconnect it from the power
supply.
Before carrying out any service on the item, check:
1. Disconnect the pins from the mains or by means of a two poles switch with 3 mm minimum distance
between the contacts. (Fig. 4).
2. Relieve all the pressure from the pump head and injection tube.
3. Drain or flush all dosing liquid from the pump head. This operation can also be done with the pump dis-
connected from the plant by turning the pump upside-down for 15 to 30 seconds and without connecting
the tubing to the nipples: if this operation is not possible, dismount and remount the pump head using
the four mounting screws (Fig. 12).
In event of possible losses in the hydraulic system of the pump (breakage of the "O" ring gasket, the valves
or the hoses) the pump should immediately be brought to a stop, emptying and depressurizing the delivery
hose while taking all due safety precautions (gloves, goggles, overalls, etc.).