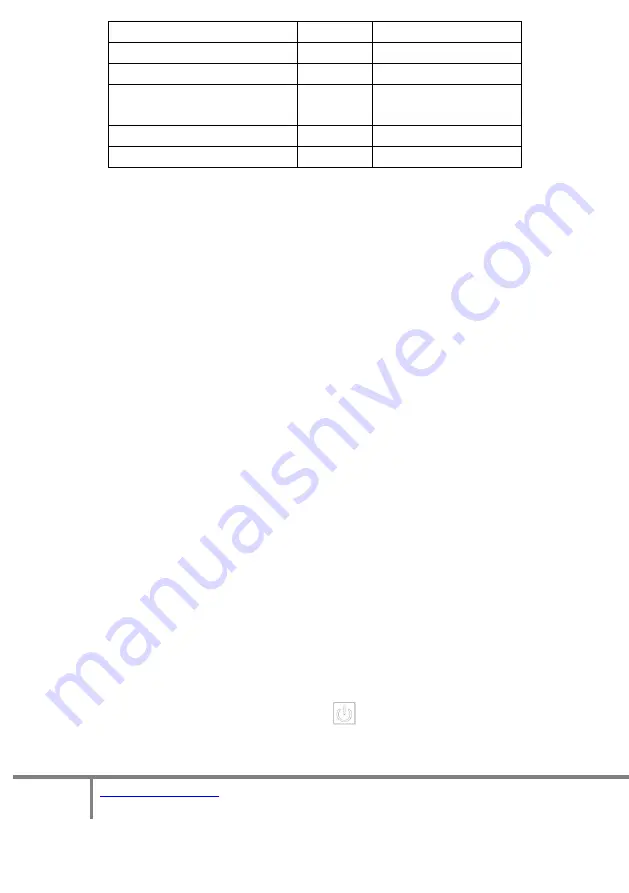
18 of 41
V 1.0
www.esavep.com
PASRW060-D-BP
Water Pressure Drop
KPa
34
Water Capacity
Ltr
2.44
Unit Dimensions
mm
See Drawings
Unit Shipping
Dimensions
mm
1050 X 510 X 1475
Net Weight
Kg
See Unit Label
Shipping Weight
Kg
See Package Label
9.0 Commissioning
9.1 Pre-Start Checks
The following checks must be made prior to starting up the unit for the first
time:
Check that all relevant lever valves are open.
Check the water loop and expansion tank to ensure that both have
adequate water in them to allow the system to operate at 1 – 1.5
bar.
Ensure that all air has been purged from the system.
Ensure that pipes are well insulated using waterproof lagging, with
at
least
30mm wall thickness.
Check the electrical wiring is correct in every respect. In particular,
make sure that the system is properly earthed.
Inspect the heat pump to ensure that all the cover screws have been
replaced and secured properly.
Check that the fan rotates freely.
When you switch on the power to the unit at the rotary isolation
switch, check the controller on the unit casing to see if there is an
error code being displayed.
9.2
Switching on the Unit
Please familiarise yourself with the unit controller and the
instructions in section 10 so that you can check various parameters as
the unit starts.
Start the heat pump by pressing the
key on the unit controller
(see section 10). This will start the water pump. Check that the
water pump is running - there should be a reading of 0.2 MPa on the