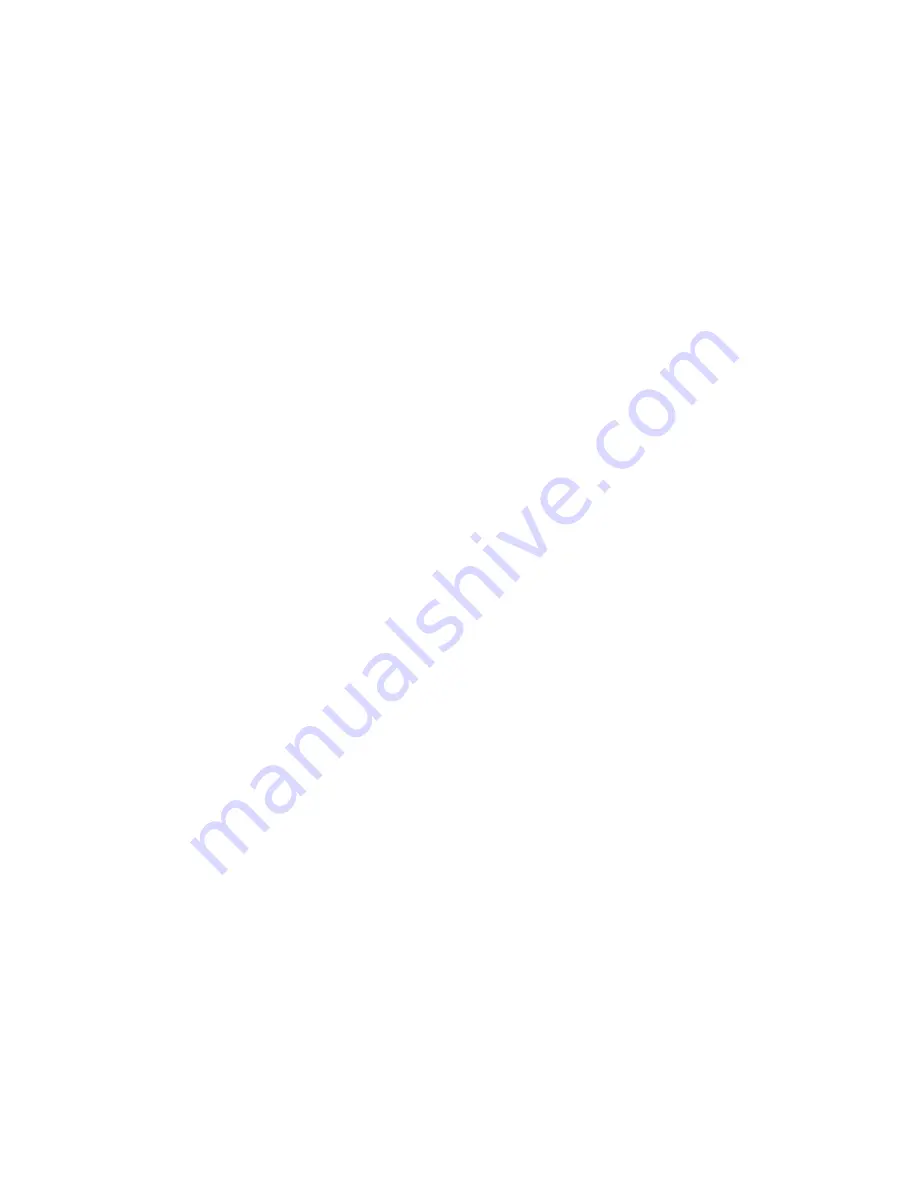
The following procedure must be followed
exactly as outlined or the calibration will not
be correct which will result in inaccurate
readings. These controls are very sensitive. A
small change can cause a large difference in
the reading so be careful and patient. Move
the controls very slowly and only a very
small amount at a time. After each change in
control settings, release the power button
and press and hold it again to ensure that the
meter is reading the change you just made.
Insert the probe leads that you are using into the
two probe jacks located in the lower left and
lower right corners of the board. Attach the 1
Meg Ohm resistor to the clip leads and be sure
that the ends of the leads that are attached to
the resistor don’t touch anything else
including the table that you are working on.
It is important for you to understand that all
of the calibration controls are interrelated.
That is, if you make a change to one control, the
other two may very well be out of calibration.
You must do a sort of balancing act between
the three controls in order to arrive at a
calibrated meter. Do the first one first, then the
second, and then the third. Then go back and
check them again. When you are getting close
you might notice that changing R11 affects the
reading of R9. You have to set R11 and recheck
R10 and R9. If you change R10 you need to
check R11 and R9. If you change R9 you need
to recheck R11 and R10 and so on.
Carefully push the red power button on the face
of the meter and hold it in while the meter makes
its reading. The meter should read close to
1.0 E 6. If the reading is too high, rotate R11 (the
one on the left) counterclockwise just a little
while pressing the red power button. If the
reading is too low, then rotate R11 clockwise
just a little while holding in the red power button.
As with each slight change you make with all
the controls, you must release the power
button and re-press and hold it to ensure that
the change you made is read by the meter.
Continue this process until the reading is 1.0 E 6.
Once the reading is 1.0 E 6 then proceed to the
next step.
Remove the 1 Meg Ohm resistor and replace it
with the 22 Kilo Ohm resistor making sure that
the resistor leads and the probe leads don’t
touch anything else. Press and hold the red
power button on the front of the meter and
observe the reading. The meter should read 2.2
E 4. If the reading is too high then carefully and
slightly rotate the R10 control counterclockwise
and re-test the change. If the reading was too
low then rotate R10 clockwise just a little and re-
test the change you made. After adjusting R10
the meter should read 2.2 E 4. Proceed to the
next step.
Remove the 22 Kilo Ohm resistor and replace it
with a 1 Kilo Ohm resistor. Press and hold the
red power switch. The meter should read
1.0 E 3. As with the other two adjustments, if the
reading is too high then rotate R9 counter-
clockwise and re-test. If the reading is too low
then rotate R9 clockwise a bit and re-test. When
the meter reads 1.0 E 3 then proceed to the next
step.
After the initial adjustments of the three controls
for the three calibration resistors you must now
go back and re-check all of the settings. The
reason for this is due to the fact that all three
controls are interrelated and must be adjusted
and calibrated together. To achieve this you must
start with R11. Re-adjust and re-test R11 with the
1 Meg Ohm resistor and then check, re-adjust
and re-test R9 and R10 with their respective
calibration resistors. Now start with R10 (22 Kilo
Ohms) and re-check and re-adjust R11 and R9.
Finally start with R9 (1 Kilo Ohms) and re-check
and re-adjust R11 and R10.
Once you have done this process a few times
all the readings should be exactly as
described. If one or more of the calibration
steps don’t result in an accurate reading then
something may be wrong with the meter. If
this occurs then you must send the meter
back to the factory for repair or replacement.
This instrument contains no end user
serviceable components. This meter utilizes
proprietary software that is copyright
protected. Any attempt to repair this
instrument by unqualified persons may result
in damage to its static sensitive components
and or the software program which would
void any warranty.