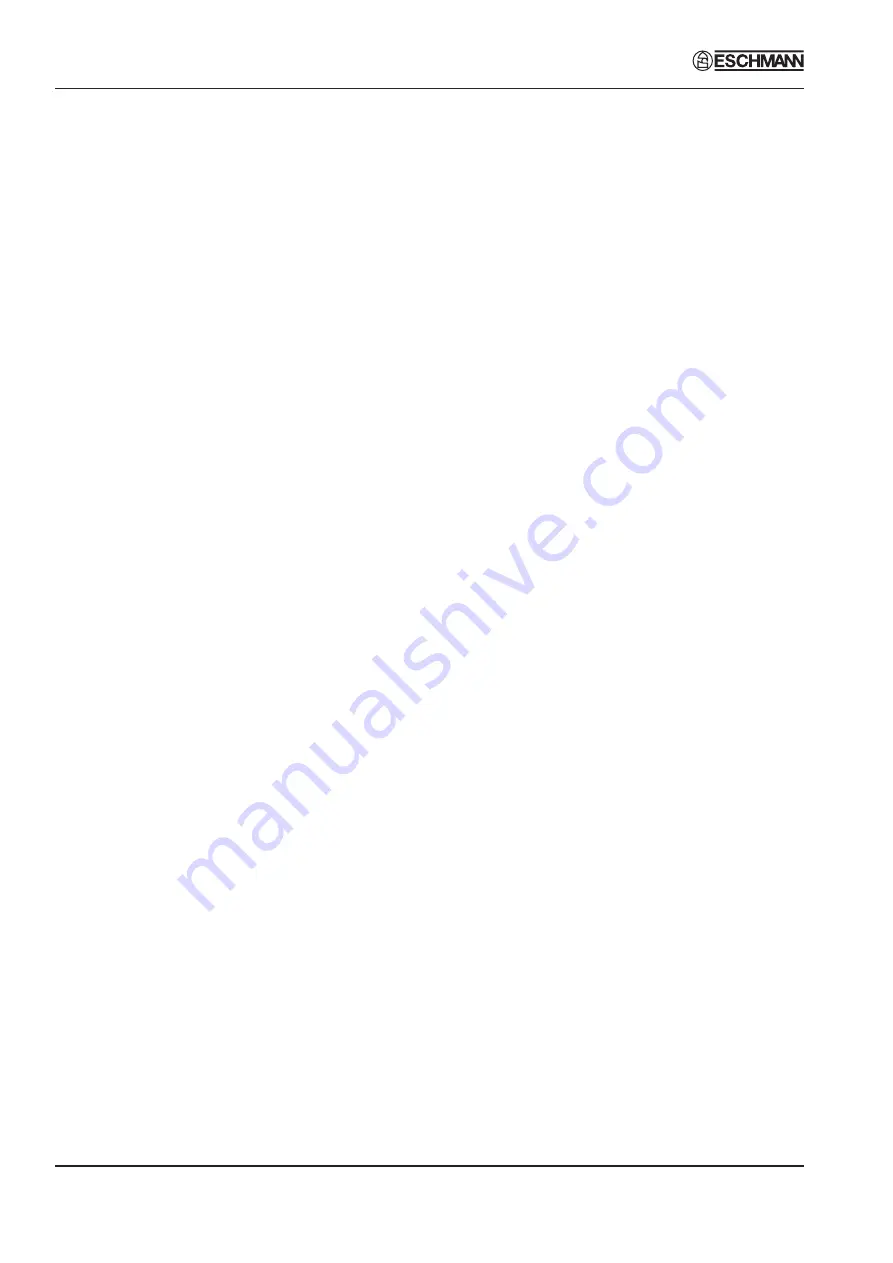
Part 2
SES 2000 Vac (LS3) AUTOCLAVE
Page 8 of 53
ST-SM45g
PART 2 DESCRIPTION
❑
Water Filter. The water filter is fitted on the end of
the water fill pipe in the water reservoir, and filters
the water entering the chamber.
❑
Reservoir Float Switch (Fig. 2.3, item 11). The water
reservoir is fitted with a float switch which will stop
the cycle being started if there is insufficient water
in the reservoir to complete a chamber fill. ‘Fill
Reservoir’ will be displayed should this occur.
❑
Heating Element (Fig. 2.4, item 1). The heating
element consists of a single immersion element
inside the chamber. The heating element is controlled
by a solid state relay and protected from overheating
by a manual reset thermostat. Refer to TECHNICAL
DATA for heater element loading.
❑
Solid-State Relay Board (Fig. 2.4, item 14). See
Appendix B. There are a number of key functions
provided by the relay board:
w
Solid state relays (SSR) control the mains
supply to the water heater element (10A), band
heater (10A) and vacuum pump (2A).
w
SSR status LEDs, give an indication of drive
status (On/Off).
w
Mechanical relay provides additional safety
for heater and pump circuits.
w
Fuses for protecting the 20V a.c. supply (3.15A),
condenser fan (2A) and vacuum pump (5A)
see 'Parts List 3'.
w
Two voltage regulators.
w
Autoclave bleeper.
w
Connections for mains loom, signal loom,
temperature and pressure sensors, solenoid
valves, and transformer.
w
Interface for front panel, control board, and
printer.
❑
Manual Reset Overheat Cutout (Fig. 2.4, item 21).
The manual reset overheat cutout is fitted at the rear
of the unit and is connected in series with the power
supply switch, band heater overheat cutout,
mechanical and SS relay and heater element. The
manual reset overheat cutout is operated by a fluid-
filled capsule clamped to the heating element,
providing protection if the temperature of the heater
surface exceeds 250°C. It will remake electrically if
the reset button at the rear of the cabinet is pressed,
after giving the heater element time to cool.
❑
Band Heater Overheat Cutout (Fig. 2.4, item 24).
The band heater cutout is fitted on the band heater
and is connected in series with the power supply
switch, Manual Reset Overheat Cutout, mechanical
and SS relay and Band Heater. It contains a bi-
metallic disc thermostat which operates if the
temperature of the heater surface exceeds 250°C.
The cutout will remake electrically if the reset button
is pressed when the heater has cooled.
❑
Fuses. The unit has five fuses:
w
Two fuses (Fig. 2.4, item 2) on the rear panel
of the cabinet rated as shown in TECHNICAL
DATA, which are connected in the ‘mains
supply’ to the unit.
w
Three more fuses are fitted on the solid-state
relay board (see TECHNICAL DATA).
❑
Transformer (Fig. 2.4, item 17). The transformer
converts the incoming mains voltage to 24V a.c. It
is rated at 50VA.
❑
Water Fill Solenoid Valve (Fig. 2.3, item 4). The
water fill valve controls the water fill sequence. It is
electrically operated from the 24V d.c. supply
generated and signalled from the SSR board.
❑
Water Discharge Solenoid Valve (Fig. 2.3, item 3).
The water discharge valve is used at the end of the
sterilizing cycle to allow water and steam vapour
from the chamber to pass back into the reservoir.
The valve is electrically operated from a 24V d.c.
supply generated and signalled from the SSR board.
❑
Discharge Line Filter (Fig. 2.3, item 12). Prevents
debris from the chamber entering and fouling the
water discharge valve.
❑
Steam Bleed Solenoid Valve (Fig. 2.3, item 2). The
steam bleed solenoid valve operates in conjunction
with the steam bleed valve.
❑
Steam Bleed Valve (Fig. 2.3, item 15). The steam
bleed valve is connected in series with the steam
bleed solenoid valve to bleed steam from the chamber
during the 121°C cycles. It contains a ball and
spring which allows air displaced by the steam
generated in the chamber to pass into the reservoir.
Once steam starts to pass, the ball then lifts and
seals. A small ‘bleed’ remains, however, and it is
quite normal for small quantities of steam to escape
into the reservoir throughout the cycle.
❑
Safety Valve (Fig. 2.3, item 16). The safety valve
is fitted on the chamber tee-piece at the rear of the
chamber, and is factory set to release pressure from
within the chamber. It is a primary safety device and
must not be readjusted.
❑
Air In Solenoid Valve (Fig. 2.3, item 5). The air inlet
valve controls the admission of bacteriologically
filtered air to the chamber during the drying phase.
A non-return valve prevents flow from the chamber
to the bacterial filter to keep it dry.
❑
Vacuum Solenoid Valve (Fig. 2.3, item 1). When
open, this valve allows the vacuum pump to suck air
and steam from the chamber.