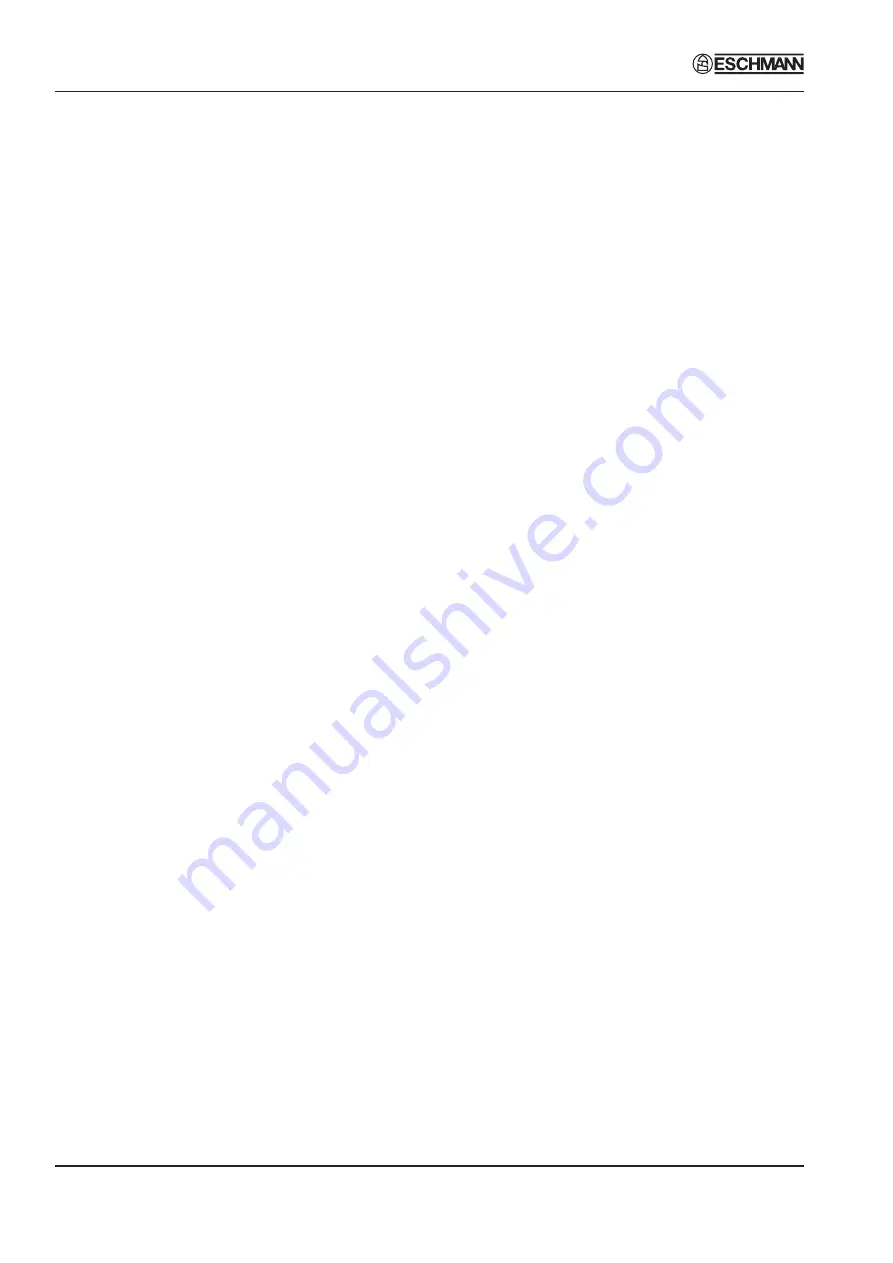
Part 3
SES 2000 Vac (LS3) AUTOCLAVE
Page 24 of 53
ST-SM45g
PART 3 MAINTENANCE
Control Board (Fig. 2.4, item 19)
9
To remove control board, pull on handle provided and
slide control board on tracks. Replacement is the reverse
of the removal procedure, but ensure that board locates
firmly in the solid state relay board.
Note 1: When a new control board is fitted, it will be
necessary to recalibrate it to suit the temperature sensor
fitted in the machine (see Calibration Procedure, para. 57
onwards).
Note 2: When ordering a new control board (part number
424424 for standard or 424425 for long) it is important to
determine what version of software is driving the machine.
The Version state of software for each particular Autoclave
will be displayed momentarily upon switching ON the
Autoclave and on later versions of the control board it is
also printed on the EPROM on the board.
Pressure Door Lock (Fig. 2.3, item 14)
10
To remove pressure door lock for adjustment or
replacement proceed as follows. From front of pressure
door lock remove screw-slotted locking bolt. Detach
plumbing connection from rear of lock body, then slacken
the two hexagon headed screws in the lock housing to
release lock body. Clean old locking compound fragments
out of threaded hole in piston, if re-fitting original lock unit.
To fit the original or a new pressure lock unit, proceed as
follows:
a Apply a drop of thread lock (Part No.306234) to
female thread only in hexagon shaped piston, then
fit lock body into lock housing on chamber neck ring
and secure it with the two hexagon headed screws
(use thread lock part number 306033 on threads).
b Attach and secure plumbing connection.
c Apply a smear of silicone grease (Part No.306055)
to shaft only of locking bolt, avoiding the thread.
d Insert locking bolt into front of lock body and screw
it into piston thread until bolt head stands
1/2mm clear of cabinet front plate. Ensure that bolt
is free to move in and out easily.
e Ensure locking bolt is fully engaged with the door at
its maximum extension.
Note: Do not try to repair a leaking or otherwise
unserviceable door lock.
Steam Bleed Valve (Fig. 2.3, item 15)
11
The steam bleed valve is fitted to the steam bleed
solenoid valve at the rear of the sterilizing chamber. To
remove the valve:
a Disconnect flexible PTFE pipe from steam valve.
b Remove steam bleed valve from solenoid elbow
fitting.
c Replacement is the reverse of the removal procedure.
When fitting replacement valve, use PTFE tape
(Part No.301600) to make a leakproof joint.
Note: It is recommended that a valve suspected of
unsatisfactory performance is renewed.
Door Interlock Microswitch (Fig. 2.4, item 4)
12
The door interlock microswitch is operated by an
actuator lever. To remove and dismantle the microswitch
actuator lever proceed as follows (the numbers in brackets
refer to the relevant parts in Fig.3.1) :
a Loosen clamp screw (7) and slide microswitch
actuator lever (5), complete with leaf spring (4), from
actuator lever (2), and then remove nylon washer
(3).
b Withdraw actuator lever (2) from the front of the
panel, and remove nylon washer (1).
c Remove clamp screw (7) and washer (8) to release
leaf spring (4).
d Remove nut (9) and striker screw (6).
e Inspect, and renew all defective items.
Reassemble and adjust the mechanism as follows, refer
to parts list if replacing parts to ensure compatible spare
parts are used:
f
Apply a smear of silicone grease (Part No.306055)
to both sides of nylon washer (1) and position it on
spindle of actuator lever (2).
g Apply a little silicone grease (Part No.306055) on
spindle of actuator lever (2) and slide the lever
through the front panel. Apply a smear of silicone
grease to both sides of nylon washer (3) and locate
the washer on the protruding end of the spindle, at
the back of the neck ring.
h Fit leaf spring (4) to microswitch actuator lever (5),
with clamp screw (7) and washer (8).
i
Fit striker screw (6) [use thread lock (part number
306033) on threads] and nut (9) to microswitch
actuator lever (5).
j
Fit microswitch actuator lever (5) to actuator lever
(2) ensuring that the mechanism is located between
limit stops (11).
k Ensure leaf spring (4) is positioned and adjusted to
keep microswitch actuator lever (5) clear of
microswitch (10).
l
While tightening clamp screw (7), twist levers (2)
and (5) apart to ensure that any slack between the
flats on the spindle and lever is in its worse condition.