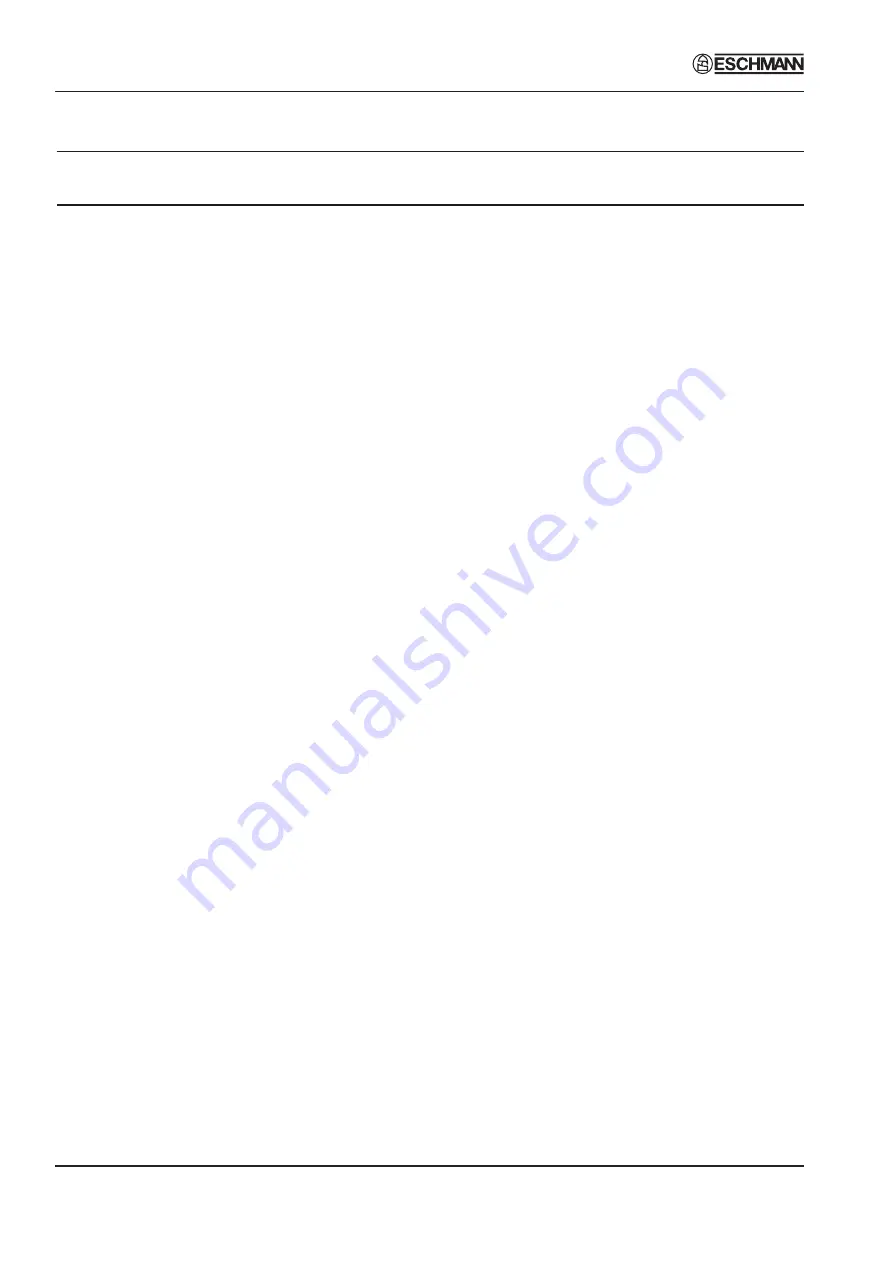
Part 3
SES 2000 Vac (LS3) AUTOCLAVE
Page 22 of 53
ST-SM45g
PART 3 MAINTENANCE
Fault
Possible Cause
Remedy
(21) ERROR 11: Insufficient
(a)
Previous cycle has left chamber
(a) Reset chamber condition by
second vacuum pulse.
too hot and wet.
running a 134°C unwrapped
with drying cycle and leave
door open for 5 minutes on
completion.
(b)
Pressure not reducing to set
(b) Carry out leak test (para.55)
point due to pump
If it fails, check all
inefficiency.
connections, door seal, and
solenoid valves for leaks.
(c)
Pressure calibration error.
(c) Recalibrate pressure channel
(para.57 onwards).
(d)
Pump cooling duct not fitted.
(d) Fit cooling duct (para.32) and
check cooling fan operation.
(22) ERROR 12: No steam pulse.
(a)
Display Pressure not reaching
(a) Check heater element (i.e.not
120kPa (Porous and wrapped
open circuit), solid state relay
cycles) or 98kPa (unwrapped
(RL2) energised (red LED,
cycles).
D6 on SSRB Fig.2.4 item14)
and mains voltage is reaching
heater element. Also see
Appendix B
(23) ERROR 13: Steam quality
(a)
At beginning of sterilizing phase, (a) Check chamber temperature
error, displayed at the
pressure displayed is not within
sensors are fitted correctly,
beginning of the
preset limits.
recalibrate pressure and
sterilizing phase.
temperature (para.57 onwards).
Also see Appendix B
(24) ERROR 13: Air detector test
(a)
Two minute duration leak test
(a) Ensure load is correctly
failed, displayed prior to
immediately prior to filling stage
conditioned (dry) before
filling phase.
has failed. Displayed pressure
starting cycle. Ensure auto-
has increased by 4kPa over a
clave passes a leak test
two minute period.
(para.55). Ensure chamber
has been ventilated with door
open for at least one minute
before starting cycle.
(25) ERROR 14: Insufficient
(a)
Insufficient pump efficiency.
(a) Check pump function, repair
drying vacuum (Display
or replace (para.38 and 20)
pressure not reaching 50kPa).
if required and check all
connections for leaks.
(b)
Pump failed to start at begin-
(b) Check pump valve seats
ning of drying phase (stalled).
have leakage path.
(models up to mod state 'E' only)
(models up to mod state 'E' only)
(26) ERROR 15: Chamber
(a)
Temperature readings differ
(a) Check chamber temperature
temperature sensor failure.
by more than 5°C during
sensors are clamped tightly
heat-up
through 100°C.
to chamber and re-calibrate
(para.57 onwards).
(27) ERROR 16: Clock speed
(a)
Real-time clock has stopped.
(a) Re-start clock by resetting
error during sterilizing phase.
time in SET-UP mode (para.
51). If this is not successful,
replace control board (para.9).
Continued