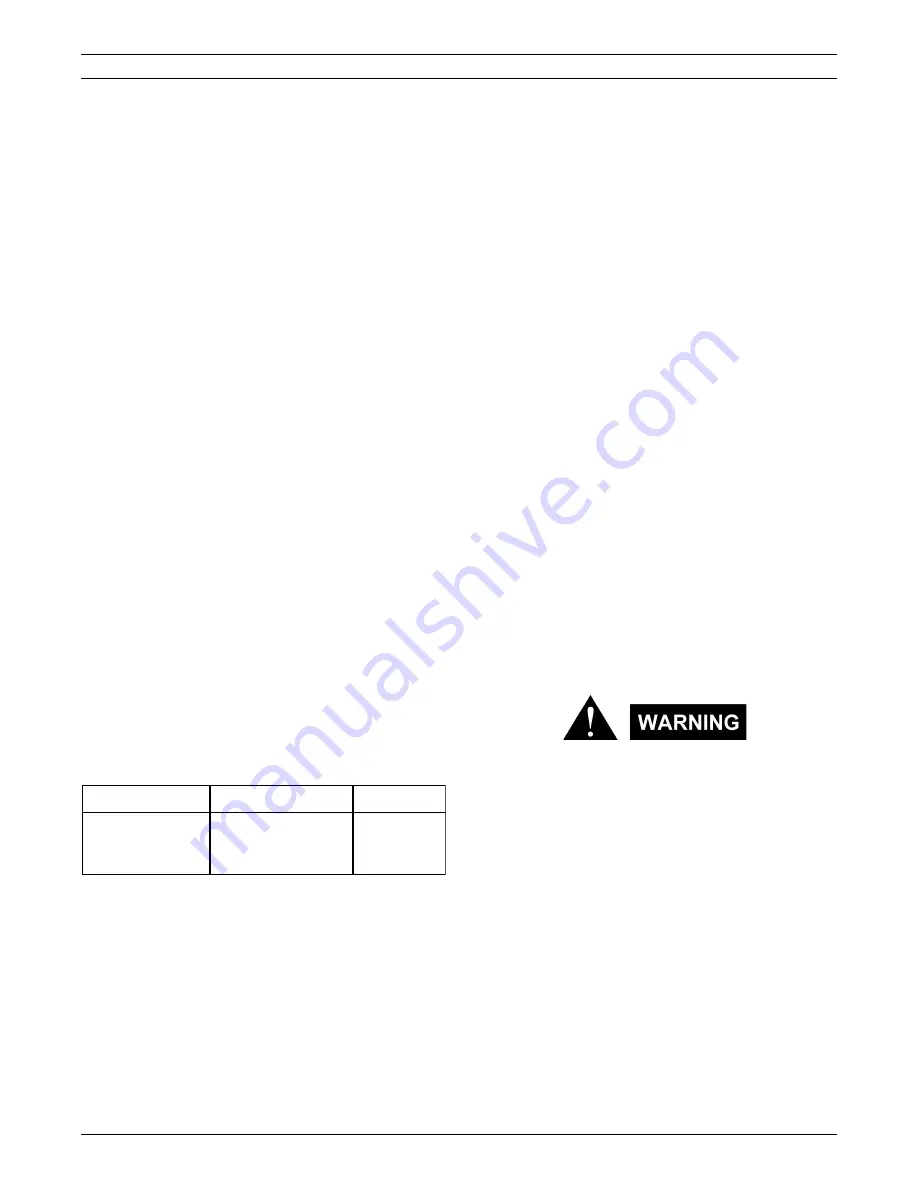
12
SECTION 3
OPERATION
D. Voltage Control Potentiometer (VCP).
This
control sets and regulates the desired amount of
welding voltage required for your operation. The
panel-faced dial surrounding the control knob
provides a convenient reference for resetting
prior welding conditions. Note that the Panel/
Remote switch must be in the PANEL position
when this control (VCP) is used.
E. Panel/Remote Control Switch (SW1).
This
switch determines the location from which weld-
ing voltage will be regulated. In the PANEL posi-
tion, full-range voltage is controlled by setting the
Voltage Control Potentiometer (VCP) on the
power supply — if desired, this position may be
used for non-digital (conventional) wire feeder
voltage control. In the REMOTE position, full
range voltage control is regulated either from the
J1 receptacle for mechanized controls or digital-
microprocessor type (Digimig/Digimatic) feeder
controls, or from the J2 receptacle for non-digital
(conventional) feeder controls using the remote
accessory hand or torch controls.
The REMOTE position is also required to provide
full range "current" control from the J2 receptacle
using the remote accessory hand, foot or torch
controls for the Stick/TIG/Gouging processes.
F. Slope Control Switch (SW3).
This 3-position
switch sets the slope of the volt-ampere curve
characteristic in the MIG (cv) mode — this control
feature is bypassed in the TIG/Stick (cc) mode.
Slope positions (top-to-bottom) are as shown in
table 3-1.
Table 3-1. Slope Positions
Switch Position
Process/Material
Slope
MEDIUM
STEEP
FLAT
Short Arc/MS/AL
Short Arc/MS,AL,SS
Spray Arc
3 V/100 A
6 V/100 A
1 V/100 A
G. Inductance Control Potentiometer (ICP).
This
control allows the operator to set and regulate the
desired amount of inductance required for stan-
dard MIG short arc welding operations. Variable
control allows the operator to fine tune the induc-
tance needed to make the weld puddle more fluid
and minimize the weld spatter produced during
MIG short arc applications. When short arc
welding stainless steel, high values of induc-
tance should be used with A1025 helium rich
shielding gas. This potentiometer should be set
to minimum for all pulse and standard spray arc
welding applications.
H. Digital MIG Control Receptacle (J1).
This 19-
pin remote control receptacle receives a mating
connector from the MIG/Digimig wire feeder or
other mechanized MIG controls (see Figure
2-1).
I. TIG/Stick Control Receptacle (J2).
This 8-pin
remote control receptacle, located on the rear
panel, receives a mating connector from the
remote control accessories (see Figure 2-3).
J. Reset Circuit Breaker (CB).
A 10-ampere cir-
cuit breaker (on the rear panel) provides protec-
tion to the 115-volt control circuit. If an overload
occurs, the breaker will trip and suspend all
operation. To restore service, depress the breaker
button to reset the circuit.
K. Auxiliary 115 Volt Receptacle (J3).
This recep-
tacle supplies 5 amperes of 115-volt power for
auxiliary equipment.
L. Welding Output Receptacles.
Two output re-
ceptacles are located on the front panel — one
negative (-) and one positive (+). Refer to figures
2-1 and 2-3.
3.5 SEQUENCE OF OPERATION
Never, under any circumstances, operate the power
source with the cover or side panels removed. In
addition to the safety hazard, improper cooling may
cause damage to internal components. Also make
sure you are adequately protected before welding.
Welding helmet, gloves, safety glasses, and ear pro-
tection should always be worn.
A. MIG Welding
1. Make all secondary output connections to the
power source output receptacles as described in
section 2 (see Figure 2-2) and as shown in the
appropriate wire feeder and/or control instruction
booklets.
2. Make the necessary control connections to re-
ceptacle J1 as described in section 2 (see Figure
2-2) and J2, if necessary. Make sure that FC-5B