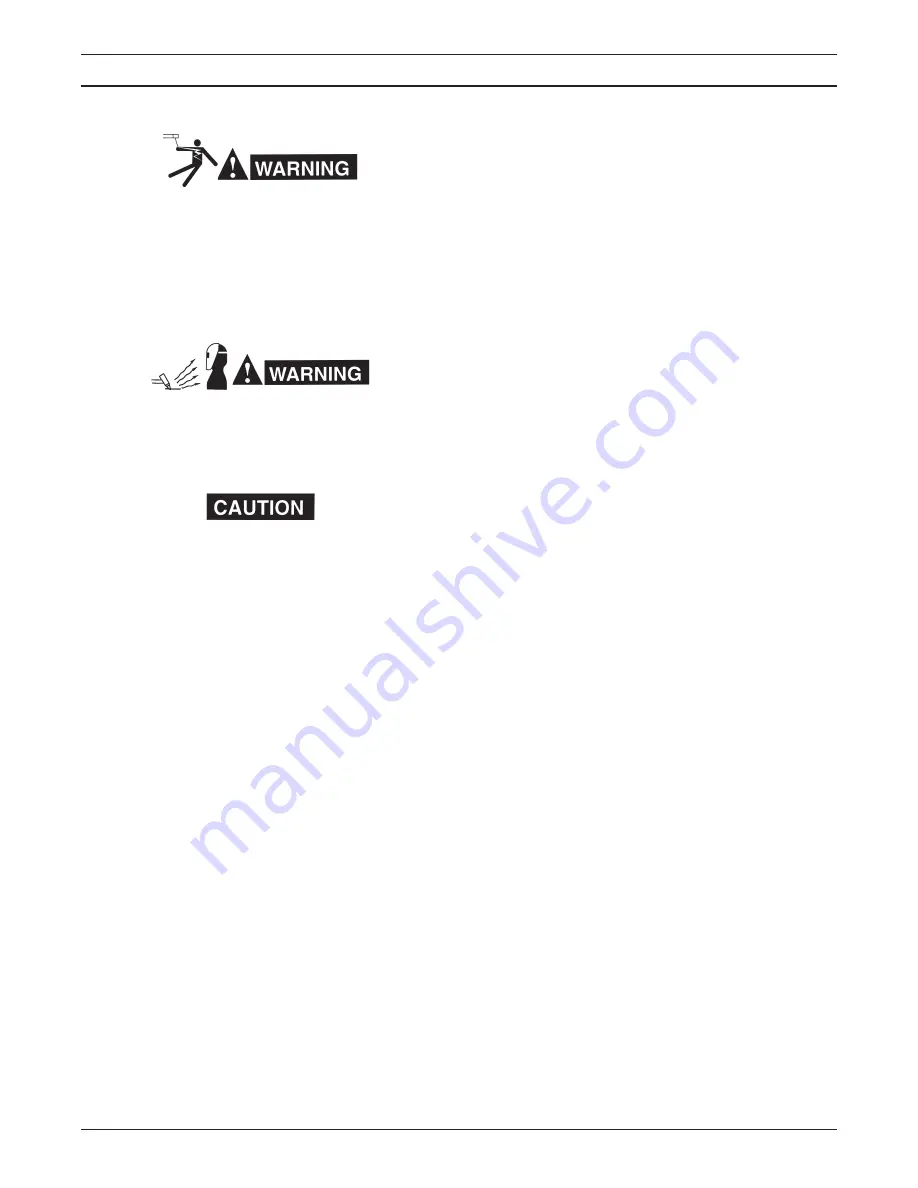
SECTION 3
OPERATION
16
3.1 OPERATION
ELECTRIC SHOCK can kill.
Do NOT operate the unit with the cover removed.
Do NOT apply power to the unit while holding or
carrying the unit.
Do NOT touch any torch parts forward of the torch
handle (nozzle, heat shield, electrode, etc.) with
power switch on.
ARC RAYS can burn eyes and skin;
NOISE can damage hearing.
Wear welding helmet with No. 6 or 7 lens shade.
Wear eye, ear, and body protection.
Position the PCM-875 at least 10 feet (3 meters) from
the cutting area. Sparks and hot slag from the cut-
ting operation can damage the unit.
3.2 PCM-875 CONTROLS (FIGURE 3-1)
A.
Power Switch (located on rear panel).
When
placed in ON position, the green pilot light will glow
indicating control circuit is energized and the
cooling fan will run.
B.
Output Current Control.
Adjustable from 10 to
60 amperes.
C.
Air Test Switch.
When placed in Test position, air
filter-regulator can be adjusted to desired pres-
sure (65-75 psig) before cutting operations. Allow
air to flow for a few minutes. This should remove
any condensation that may have accumulated
during shutdown period. Be sure to place switch
in OPERATE position before starting cutting op-
erations.
D.
Trigger Lock Switch.
When placed in LOCK
position, this permits releasing torch switch button
after cutting arc has been initiated. To extinguish
arc at end of cut, press and release torch switch
button again or pull torch away from work. When
placed in UNLOCK position, torch switch must be
held closed by the operator during the entire
cutting operation and then released at the end of
cut.
E.
Fault Light.
Will glow amber under the following
conditions and operations will come to a complete
stop.
Flow Fault:
The fault light will be
mostly on
but
will flick off for about 1/10th of a second every
second. This indicates that the air flow supply is
low.
Over Temperature:
The fault light will be
mostly
off
but will flick on for about 1/10th of a second
every second. This indicates that the duty cycle
has been exceeded. Allow the power source to
cool down before returning to operate.
High/Low Line Voltage:
The fault light will
rap-
idly blink on and off
(five times per second). This
indicates that the input voltage is outside the + or
- 15% range of the input rating.
Over-Current:
The fault light will be on
continu-
ously
. This indicates that input current has been
exceeded.
All fault signals will remain on for a minimum
of 10 seconds. If fault clears, all will reset
automatically except for over-current. To clear
over-current, the power must be shut off for 5
seconds and then turned back on.
3.3 CUTTING WITH THE PT-27
Use the following procedures to cut with the PT-27 torch
(Figure 3-4).
A.
Hold the torch nozzle approximately 1/8 to 3/16
inch above the work and tilted at about 15 - 30°.
This reduces the chance of spatter entering the
nozzle. If the PT-27's standoff tool is being used,
set the standoff between 3/16 and 1/4-inch.
B.
Depress the torch switch. Air should flow from the
torch nozzle.
C.
Two seconds after depressing the torch switch,
the pilot arc should start. The main arc should
immediately follow, allowing the cut to begin. (If
using the trigger LOCK mode, torch switch may be
released after establishing the cutting arc.)
D.
After starting the cut, the torch should be main-
tained at a 5-15° forward angle (Figure 3-2). This
angle is especially useful in helping to create a
"drop" cut. When not using the standoff guide, the
nozzle should be held approximately 1/4 inch from
the work.
Summary of Contents for PCM-875
Page 29: ...28 D 36587 Figure 5 1 Schematic Diagram PCM 875 208 230 V 50 60 Hz 1 or 3 Phase ...
Page 30: ...29 D 36595 Figure 5 2 Wiring Diagram Sheet 1 of 2 PCM 875 208 230 V 50 60 Hz 1 or 3 Phase ...
Page 31: ...30 Figure 5 3 Wiring Diagram Sheet 2 of 2 PCM 875 208 230 V 50 60 Hz 1 or 3 Phase D 36595 ...
Page 32: ...31 D 36597 B Figure 5 4 Schematic Diagram PCM 875 400 460 V 50 60 Hz 3 Phase 1 2 3 4 5 6 ...
Page 33: ...32 D 36598 Figure 5 5 Wiring Diagram Sheet 1 of 2 PCM 875 400 460 V 50 60 Hz 3 Phase ...
Page 34: ...33 D 36598 Figure 5 6 Wiring Diagram Sheet 2 of 2 PCM 875 400 460 V 50 60 Hz 3 Phase ...
Page 35: ...34 D 36715 A Figure 5 7 Schematic Diagram PCM 875 575 V 60 Hz 3 Phase ...
Page 36: ...35 D 36716 Figure 5 8 Wiring Diagram Sheet 1 of 2 PCM 875 575 V 60 Hz 3 Phase ...
Page 37: ...36 D 36716 Figure 5 9 Wiring Diagram Sheet 2 of 2 PCM 875 575 V 60 Hz 3 Phase ...
Page 47: ...46 ...