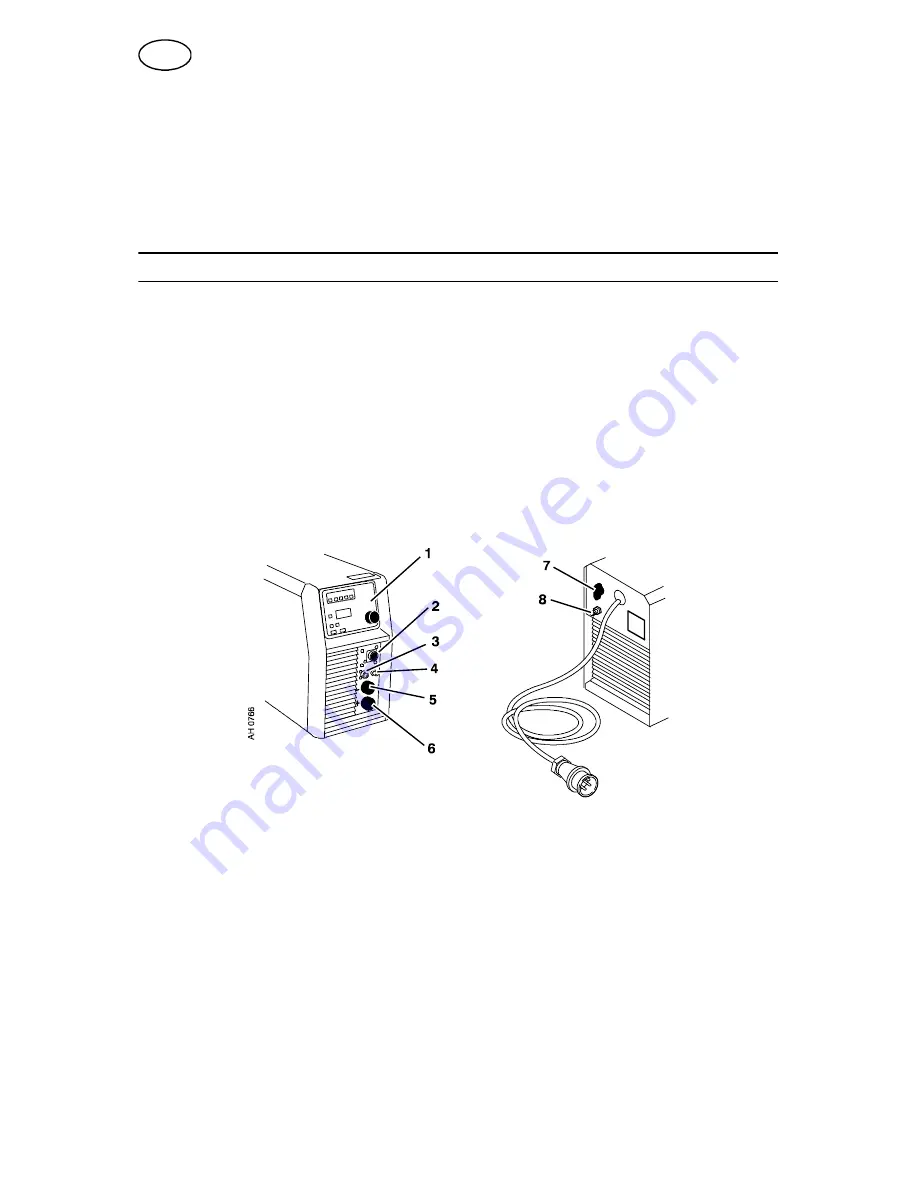
-- 18 --
bt30d1ea
Note!
The mains cable areas and fuse sizes as shown above are in accordance with Swedish
regulations. Use the welding power source in accordance with the relevant national regulations.
Note!
The welding power source is designed for connection to a 230 / 400 volt
system with four conductors.
If the power source is to be used in countries with a higher supply voltage, the power
source must be connected via a safety transformer.
6
OPERATION
General safety regulations for the handling of the equipment can be found on
page
13
. Read through before you start using the equipment!
6.1
Connections and control devices
1
Control panel,
see separate instruction manual
5
Connection for welding cable (--) or
welding torch
2
CAN connection for cooling unit or remote
control unit
6
Connection for return cable (+)
3
Connection for start signal from the
welding torch
7
Mains voltage switch
4
Connection for gas to the torch
8
Connection for shielding gas
6.2
Fan control
The power source has a time control that means that the fans continue to run for 6.5
minutes after welding has stopped, and the unit switches to energy--saving mode.
The fans start again when welding restarts.
The fans run at reduced speed for welding currents up to 110 A, and at full speed for
higher currents.
6.3
Overheating protection
The welding power source has overheating protection that operates if the
temperature becomes too high. When this occurs the welding current is interrupted
and a fault code is displayed on the control panel.
The overheating protection resets automatically when the temperature has fallen.
GB
Summary of Contents for Origo Tig 3000i
Page 21: ... 21 p ...
Page 22: ...Edition 100114 Diagram Ñõåìà 22 cc19e ...
Page 23: ...Edition 100114 23 cc19e ...
Page 27: ... 27 p ...
Page 28: ... 28 backpage ...