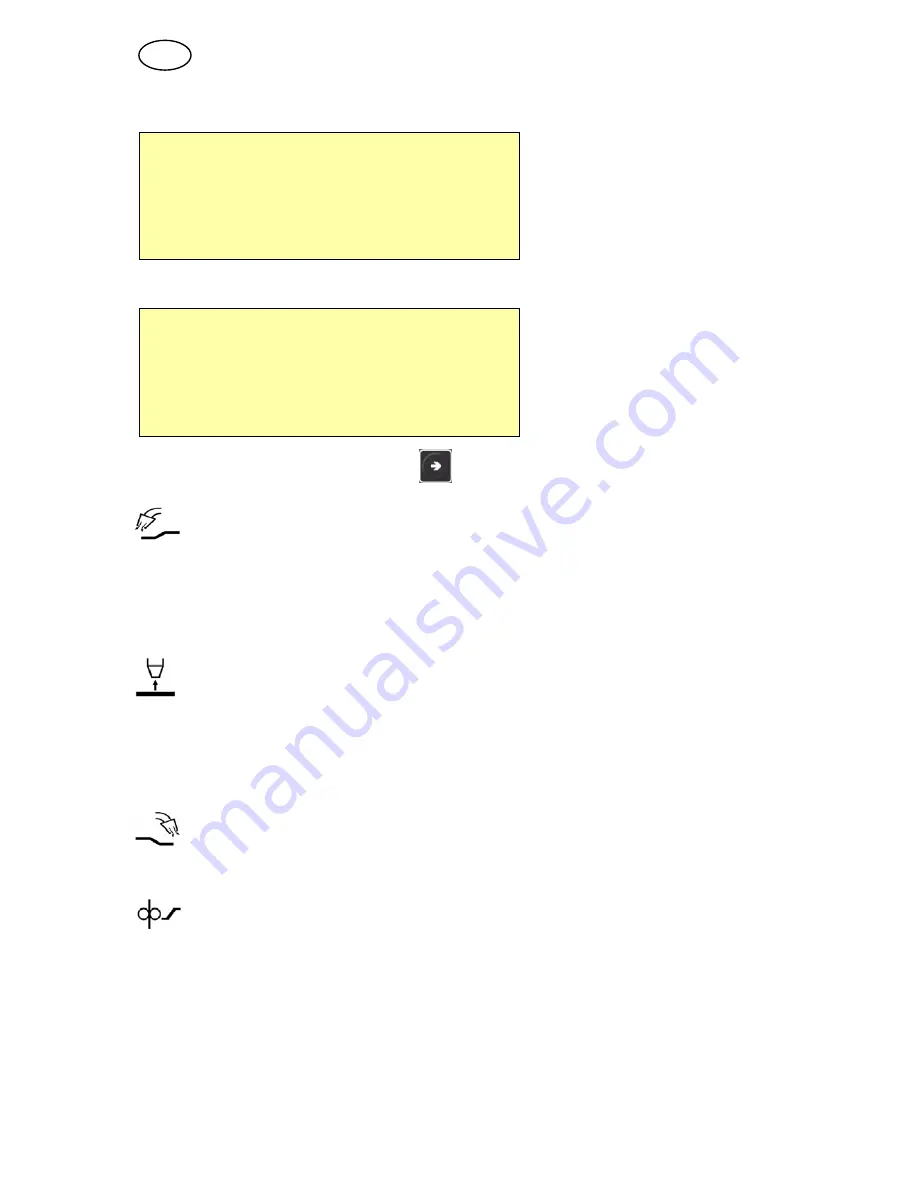
- 9 -
bi21d1ea
MA23
Function letter
Function
A
Gas pre-flow
I
Burnback time
L
Gas post-flow
J
Creep start
MA24
Function letter
Function
A
Gas pre-flow
C
Unit of measurement
I
Burnback time
L
Gas post-flow
To leave the function hold the button
depressed for 5 seconds.
Gas pre-flow
This controls the time during which shielding gas flows before the arc is struck.
Unit of measurement
0 = inch, 1 = mm, Default value = 1
Burnback time
Burnback time is a delay between the time when the wire starts to brake until the
time when the power source switches off the welding voltage. Too short burnback
time results in a long wire stickout after completion of welding, with a risk of the
wire being caught in the solidifying weld pool. Too long a burnback time results in a
shorter stickout, with increased risk of the arc striking back to the contact tip.
Gas post-flow
This controls the time during which shielding gas flows after the arc is extinguished.
Creep start
Creep starting feeds out the wire at 50% of the set speed until it makes electrical
contact with the workpiece.
GB