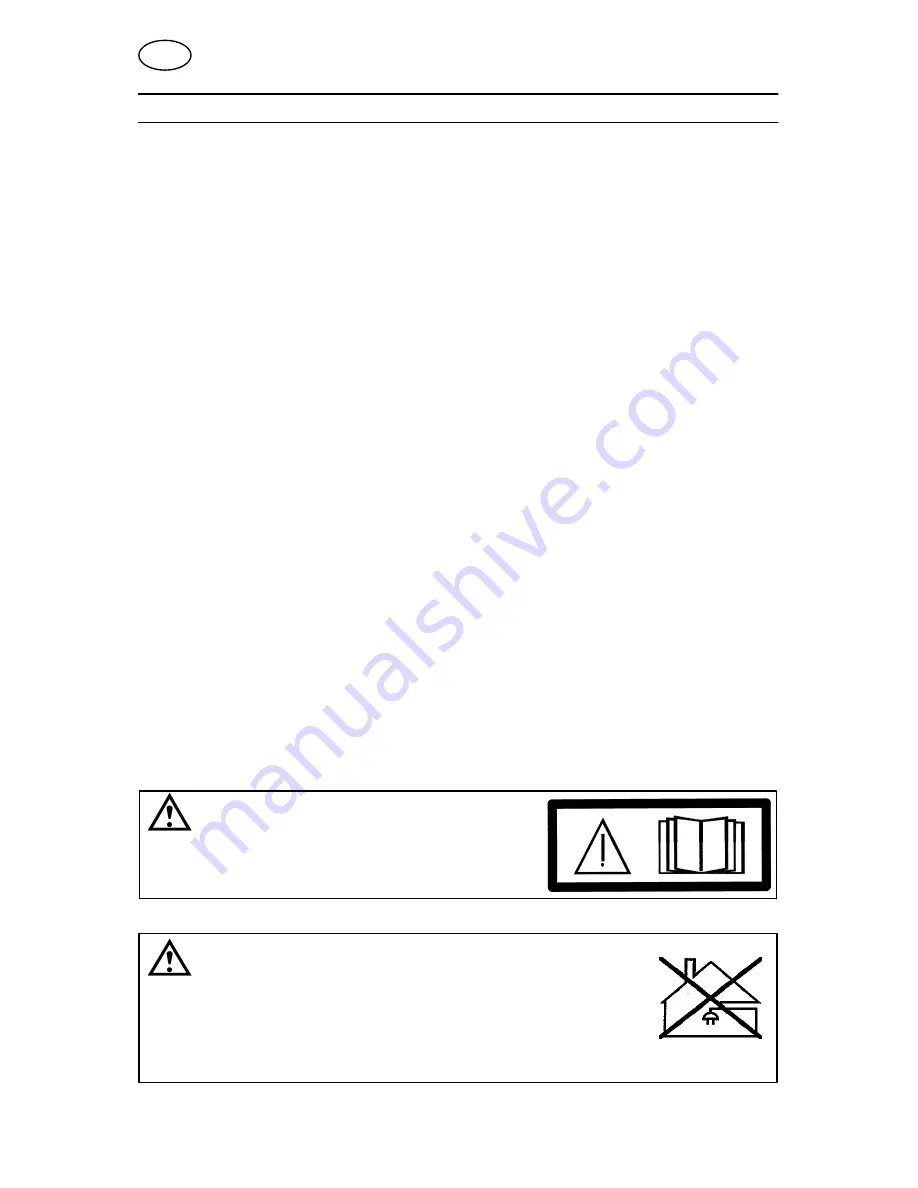
© ESAB AB 2003
- 4 -
bm33d1ea
1
SAFETY
Users of ESAB equipment have the ultimate responsibility for ensuring that anyone who works on or
near the equipment observes all the relevant safety precautions. Safety precautions must meet the
requirements that apply to this type of equipment. The following recommendations should be ob
served in addition to the standard regulations that apply to the workplace.
All work must be carried out by trained personnel well-acquainted with the operation of the equip
ment. Incorrect operation of the equipment may lead to hazardous situations which can result in in
jury to the operator and damage to the equipment.
1.
Anyone who uses the equipment must be familiar with:
its operation
location of emergency stops
its function
relevant safety precautions
welding and cutting
2.
The operator must ensure that:
no unauthorised person is stationed within the working area of the equipment when it is
started up.
no-one is unprotected when the arc is struck
3.
The workplace must:
be suitable for the purpose
be free from drafts
4.
Personal safety equipment
Always wear recommended personal safety equipment, such as safety glasses, flame-proof
clothing, safety gloves.
Do not wear loose-fitting items, such as scarves, bracelets, rings, etc., which could become
trapped or cause burns.
5.
General precautions
Make sure the return cable is connected securely.
Work on high voltage equipment
may only be carried out by a qualified electrician.
Appropriate fire extinquishing equipment must be clearly marked and close at hand.
Lubrication and maintenance must
not
be carried out on the equipment during operation.
ESAB can provide you with all necessary welding protection and accessories.
CAUTION
Read and understand the instruction manual before
installing or operating.
CAUTION
Class A equipment is not intended for use in residential locations where
the electrical power is provided by the public low-voltage supply system.
There may be potential difficulties in ensuring electromagnetic
compatibility of class A equipment in those locations, due to conducted
as well as radiated disturbances.
GB
Summary of Contents for Origo M 12 Feed 304
Page 2: ...2...
Page 15: ...ESAB AB 2003 15 bm33e11a...
Page 16: ...ESAB AB 2003 16 bm33e11a Feed 304 M12 valid from serial no 917 xxx xxxx...
Page 17: ...ESAB AB 2003 17 bm33e11a...
Page 18: ...18 p...
Page 21: ...Feed 304 ESAB AB 2003 21 bm33whj1...
Page 24: ...Feed 484 ESAB AB 2003 24 bm33whk1...
Page 30: ...30 notes NOTES...
Page 31: ...31 notes NOTES...