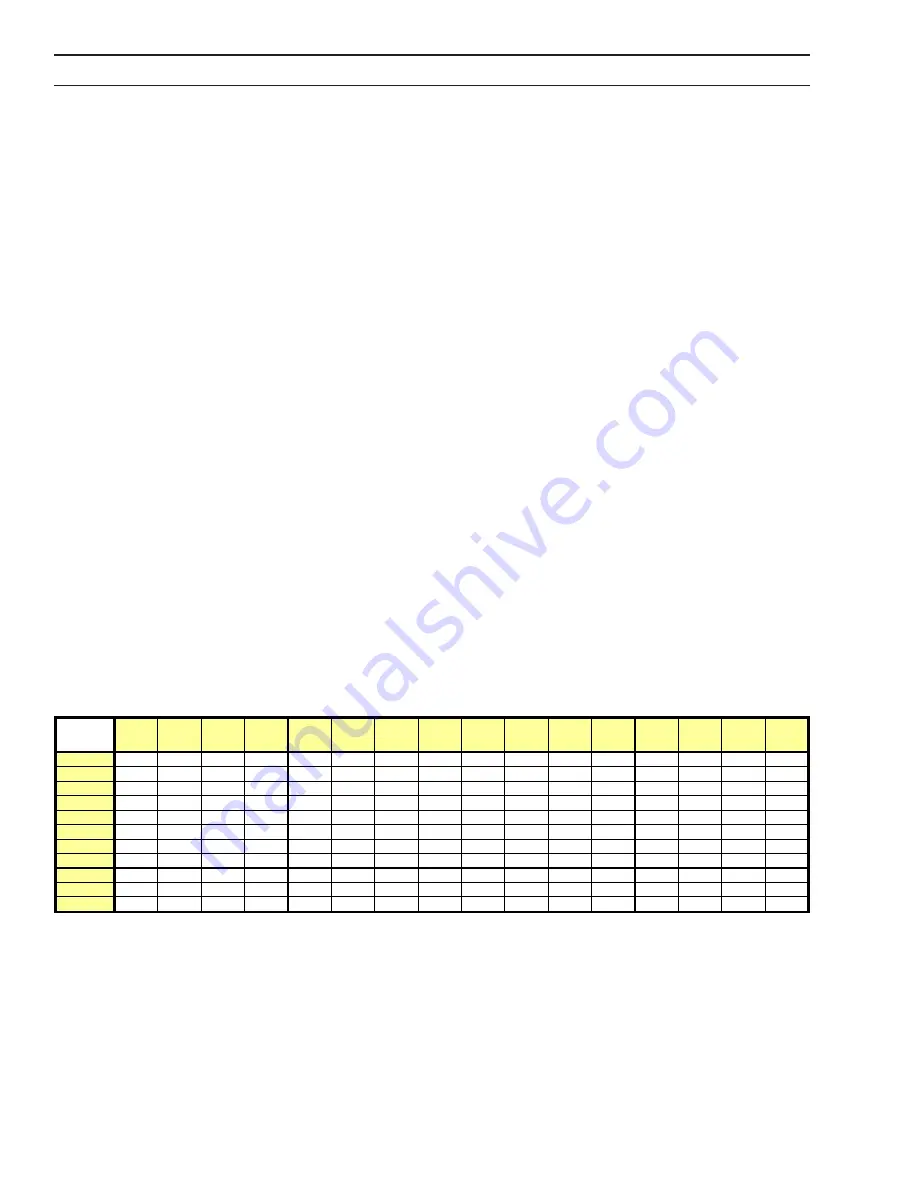
32
sectIon 3
operatIon
note
On many CV power sources the actual welding arc voltage is usually less the “Open Circuit Voltage” (OCV) set on the power
source front panel. Therefore, an extra 3 to 6 volts should be added to the power source front panel setting to achieve the
“actual” arc voltage needed or shown in the tables.
* MobileFeed Wire Feed Speed Knob Position
WIRE FEED SPEED TABLE
WFS
Set
19 V
20 V
21 V
22 V
23 V
24 V
25 V
26 V
27 V
28 V
29 V
30 V
31 V
32 V
33 V
34 V
Min
0
0
0
0
0
0
0
0
0
0
0
0
0
0
0
0
1
4
5
5
6
6
7
7
7
9
11
12
15
14
13
13
11
2
44
51
56
65
70
74
77
85
90
93
95
103
102
102
101
100
3
99
109
116
129
136
140
144
155
165
173
179
196
198
200
201
205
4
152
163
170
184
196
204
211
230
241
250
256
275
282
287
291
302
5
210
225
235
255
270
281
290
315
329
339
347
370
379
385
390
405
6
267
282
292
312
331
345
356
388
412
430
443
483
490
495
499
510
7
334
354
368
395
415
430
441
475
503
524
540
587
594
599
603
615
8
380
411
431
472
494
511
523
560
589
610
626
675
685
693
698
715
9
385
427
454
510
536
556
571
615
649
674
693
750
770
785
796
830
Max
395
435
462
515
544
565
581
630
667
695
716
779
803
820
833
873
Min
Max
* Wire
Speed Set
3.5 shutDoWn
A. Release torch trigger to break the arc.
B. When leaving the equipment unattended, always shut OFF and disconnect all power to the equipment and shut off the
shielding gas supply at source.
MobileFeed 300 with Digital meter and
CONSTANT CURRENT Power Source
Using the table, select the weld VOLTAGE / CURRENT
1.
needed for the wire type and diameter to be weld-
ed.
Set the power supply CURRENT using the cur-
2.
rent control knob on the front panel of the power
source.
Read the WIRE FEED SPEED (WFS) at the top of the
3.
column for the wire type, diameter and weld VOLT-
AGE / CURRENT chosen.
Flip the MobileFeed digital display switch to the WFS
4.
position.
Release the pressure roll assembly and pull the gun
5.
trigger then set the WFS on the digital display using
the VOLTS / WFS knob.
Reset the pressure roll assembly and strike an arc
6.
then trim the arc length as needed using the VOLTS
/ WFS knob.
MobileFeed 300 with Digital meter and
CONSTANT VOLTAGE Power Source
Using the table, select the weld VOLTAGE / CURRENT
1.
needed for the wire type and diameter to be weld-
ed.
Set the power supply VOLTAGE using the voltage con-
2.
trol knob on the front panel of the power source.
Read the WIRE FEED SPEED (WFS) at the top of the
3.
column for the wire type, diameter and weld VOLT-
AGE / CURRENT chosen.
Flip the MobileFeed digital display switch to the WFS
4.
position.
Release the pressure roll assembly and pull the gun
5.
trigger then set the WFS on the digital display using
the VOLTS / WFS knob.
Reset the pressure roll assembly and strike an arc
6.
then trim the arc length as needed using the VOLTS
/ WFS knob.
note
Using the “Constant Feed” dip switch settings when using a CC power source is NOT RECOMMENDED. Extreme wire feed
speed sensitivity exists making it difficult to set stable welding condition. The arc stability is very dependant on maintain-
ing constant TTW distance which is almost impossible to control when welding manually. “Constant Speed” settings is only
recommended for use with CV power sources.
Typical welding voltages for 5000 Aluminum are between 21 and 25 volts which limits the wire feed speed of the Mobile-
Feed especially if trying to weld with 035” diameter 5356 alloy. Welding with wire diameters ≤3/64” and/or below 22 arc
volts could cause problems with limited wire feed speed and the inability to achieve a good welding condition.
Summary of Contents for MobileFeed 300 AVS
Page 1: ...MobileFeed 300 AVS Portable Off The Arc Wire Feeder Instruction Manual 0558005921 03 2008 ...
Page 3: ......
Page 4: ...4 ...
Page 6: ...6 TABLE OF CONTENTS ...
Page 22: ...22 SECTION 1 DESCRIPTION ...
Page 26: ...26 SECTION 2 INSTALLATION ...
Page 35: ...35 SECTION 4 MAINTENANCE ...
Page 36: ...36 SECTION 4 MAINTENANCE ...
Page 38: ...38 SECTION 5 REPLACEMENT PARTS ...
Page 39: ...39 SECTION 5 REPLACEMENT PARTS ...
Page 40: ...40 SECTION 5 REPLACEMENT PARTS ...
Page 41: ...41 SECTION 5 REPLACEMENT PARTS ...
Page 42: ...SECTION 5 REPLACEMENT PARTS ...
Page 43: ...SECTION 5 REPLACEMENT PARTS ...
Page 44: ...SECTION 5 REPLACEMENT PARTS ...
Page 45: ...SECTION 5 REPLACEMENT PARTS ...
Page 46: ...46 SECTION 5 REPLACEMENT PARTS ...
Page 48: ...SECTION 5 REPLACEMENT PARTS ...
Page 51: ......
Page 52: ......