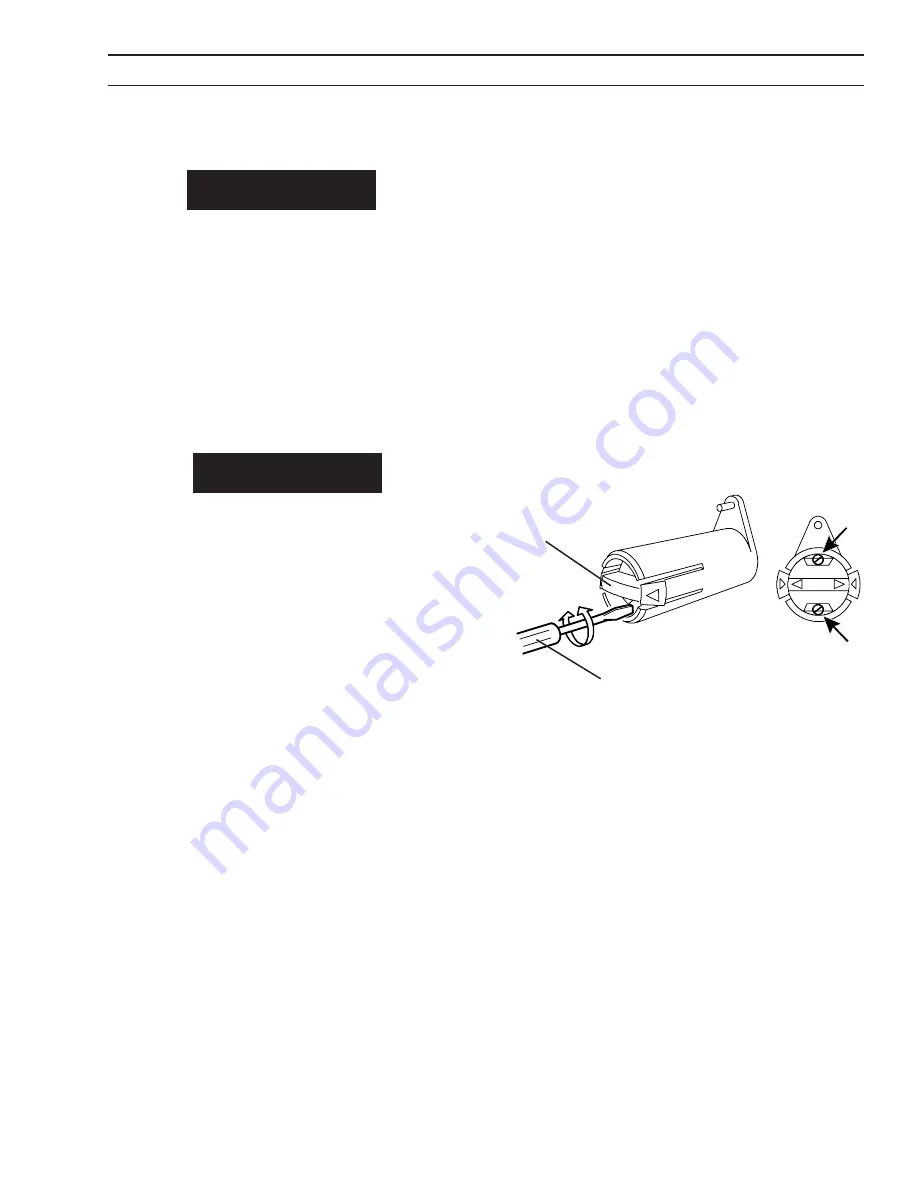
25
2.5 threaDIng the WelDIng WIre
When the wire feeder is connected to the power source,
the work lead from the power source is connected to
the work piece and the power source is energized,
closing the torch trigger will cause the welding wire to
become electrically hot and will cause the drive rolls
to turn. Keep fingers clear!
A. Turn OFF the power source and the wire feeder.
B. Release the pressure roll assembly lever and check
for the proper drive roll, groove position and wire
guides.
Before threading welding wire, make sure the chisel
point and burrs have been removed from the end
of the wire to prevent the wire from jamming in the
torch liner.
C. Feed the wire from the spool through the inlet guide
along the drive roll groove and into the outlet guide
tube.
D. Lower the pressure roll assembly and adjust the drive
roll pressure to assure no wire slippage, but not too
tight to create excess pressure.
E. Turn ON the power source and the wire feeder. Close
the torch trigger to feed wire through the torch.
cautIon
WarnIng
2.6 BraKe Drag aDJustMent
Brake disc friction should provide enough drag to keep the
wire spool from spinning freely after the wire feed stops.
The brake hub is adjusted when delivered, if readjustment
is required, follow the instructions below. Adjust the brake
hub so that wire is slightly slack when wire feed stops.
adjusting the braking torque:
Turn the red handle to the locked position.
•
Insert a screwdriver into the springs in the hub.
•
Turn the springs clockwise to reduce the braking torque
Turn the springs counterclockwise to increase the braking
torque. Turn both springs through the same amount.
sectIon 2
InstallatIon
-- 13 --
bm29d1ea
7
MAINTENANCE
Regular maintenance is important in ensuring safe and reliable.
Note!
All guarantee undertakings from the supplier cease to apply if the customer himself
attempts any work in the product during the guarantee period in order to rectify any
faults.
7.1
Inspection and cleaning
Wire feed unit
Check regularly that the wire feed unit is not clogged with dirt.
S
Cleaning and replacement of the wire feed unit mechanism’s worn parts should
take place at regular intervals in order to achieve trouble--free wire feed. Note
that if pre--tensioning is set too hard, this can result in abnormal wear on the
pressure roller, feed roller and wire guide.
SCREWDRIVER
SPRING
LOCATIONS
RED
HANDLE
Summary of Contents for MobileFeed 300 AVS
Page 1: ...MobileFeed 300 AVS Portable Off The Arc Wire Feeder Instruction Manual 0558005921 03 2008 ...
Page 3: ......
Page 4: ...4 ...
Page 6: ...6 TABLE OF CONTENTS ...
Page 22: ...22 SECTION 1 DESCRIPTION ...
Page 26: ...26 SECTION 2 INSTALLATION ...
Page 35: ...35 SECTION 4 MAINTENANCE ...
Page 36: ...36 SECTION 4 MAINTENANCE ...
Page 38: ...38 SECTION 5 REPLACEMENT PARTS ...
Page 39: ...39 SECTION 5 REPLACEMENT PARTS ...
Page 40: ...40 SECTION 5 REPLACEMENT PARTS ...
Page 41: ...41 SECTION 5 REPLACEMENT PARTS ...
Page 42: ...SECTION 5 REPLACEMENT PARTS ...
Page 43: ...SECTION 5 REPLACEMENT PARTS ...
Page 44: ...SECTION 5 REPLACEMENT PARTS ...
Page 45: ...SECTION 5 REPLACEMENT PARTS ...
Page 46: ...46 SECTION 5 REPLACEMENT PARTS ...
Page 48: ...SECTION 5 REPLACEMENT PARTS ...
Page 51: ......
Page 52: ......