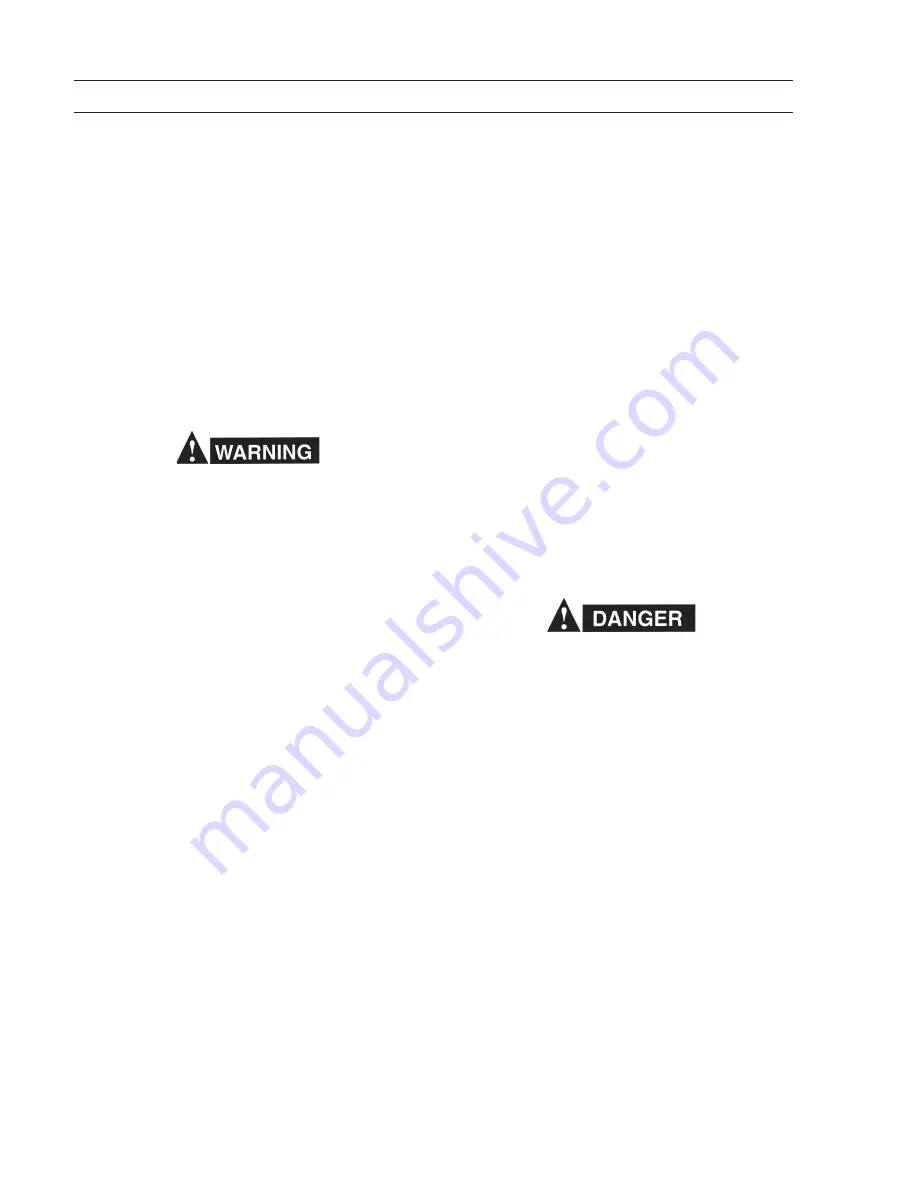
28
E. Never operate the equipment at currents greater
than the rated ampere capacity; overheating will
occur.
F. Never operate equipment in a damp or wet area
without suitable insulation for protection against
shock. Keep hands, feet and clothing dry at all
times.
G. Whenever the equipment is left unattended, turn
all control and power supply switches and gas
supplies OFF and open the main line switch.
H. Wear dark substantial clothing to protect exposed
skin from arcburn, sparks and flying hot metal.
I. Turn off welding power before adjusting or replacing
electrodes.
Never operate the welding machine with any por-
tion of the outer enclosure removed. In addition to
a hazard, improper cooling may result in damage to
the welding transformer and the welding machine
components. Warranty is void if the machine is
operated with any portion of the outer enclosure
removed.
4.3.2 PRE-WELD REQUIREMENTS
Before welding commences, with all power OFF, check
the following:
A. All safety requirements have been read and un-
der stood.
B. All hoses and cables are in good condition, safely
insulated and securely connected.
C. Turn on gas supply by slowly opening cylinder
valve to full ON.
D. Correct size wire accessories have been installed
on the wire feeder, drive gears are meshed, wire
pressure set, and guide tube is installed for type
and size wire you plan to use, refer to Tables
2.4.5, and 4.3..
E. Spool of correct size wire is locked in place, brake
tension is set, and wire is properly threaded
through the inlet guide to the gun tip.
F. The wire feeding compartment cover is closed
and secure.
G.Make sure that the metal to be welded is properly
prepared:
a. Remove loose surface rust, scale or paint with
wire brush or sander.
b. Attempting to weld over grease or oil can cause
weld defects.
c. Before welding on aluminum, be sure to clean
surface thoroughly using a stainless steel brush.
4.3.3 SET-UP PROCEDURE
A. Determine the material type, thickness and joint
configuration to be welded from Table 4.3 and use
the recommendations to set the following:
a. Coarse Voltage Range, LOW/MED/HIGH.
b. Fine Arc Voltage Setting, 1 thru 8 (the higher the
number, the hotter the weld).
c. Wire Speed setting, 0 thru 10 (the higher the
number, the faster the speed).
B. Set the two-position switch in the wire feeder com-
partment to STANDARD for seam welding with the
GUNMASTER 250 torch. (For ST-23A Spool-On-
Gun welding, see Section 4.2.2).
C. If optional Spot/Stitch/Anti-Stick Control module is
installed, refer to Section 4.2.3 for operation, set-
tings and welding condition table.
D. Make sure the GUNMASTER 250 torch fitting
and the “Work” cable are connected to the proper
output terminals (inside unit) for the polarity de-
sired.
Only qualified personnel should make these changes.
Make certain the primary power has been discon-
nected and all safety procedures have been fol-
lowed before proceeding with these instructions.
Normally, you will set-up for “reverse polarity”; this
means the torch fitting is connected to the POS (+)
output terminal and the “Work” cable to the NEG
(-) output terminal.
For “straight polarity”, do just the opposite; torch
fitting to NEG (-) output terminal and “Work” cable
to POS (+) output terminal.
4.3.4 WELDING OPERATION
A. Turn Power switch (on unit) to ON position -- be
careful not to operate the torch switch.
B. Before starting the weld, the welding wire should
extend about 1/2-inch beyond the end of the nozzle.
Adjust this length by either clipping off the end of the
wire with insulated cutters or by using the torch
switch.
SECTION 4 OPERATION
Summary of Contents for MIGMASTER 250
Page 1: ...F15 087 J 04 2003 MigMaster 250 Welding Package Instruction Manual...
Page 4: ...4 TABLE OF CONTENTS...
Page 22: ...22 SECTION 3 INSTALLATION...
Page 38: ...38 Figure 5 3 Wiring Migmaster 250 for 208 230 V Model D 32861 F...
Page 39: ...39 Figure 5 4 Wiring Migmaster 250 for 208 230 380 400 460 575 V Model D 33311 D...
Page 40: ...40 SECTION 5 SERVICE...
Page 52: ...52 SECTION 6 REPLACEMENT PARTS...
Page 53: ...53 NOTES...
Page 54: ...NOTES...