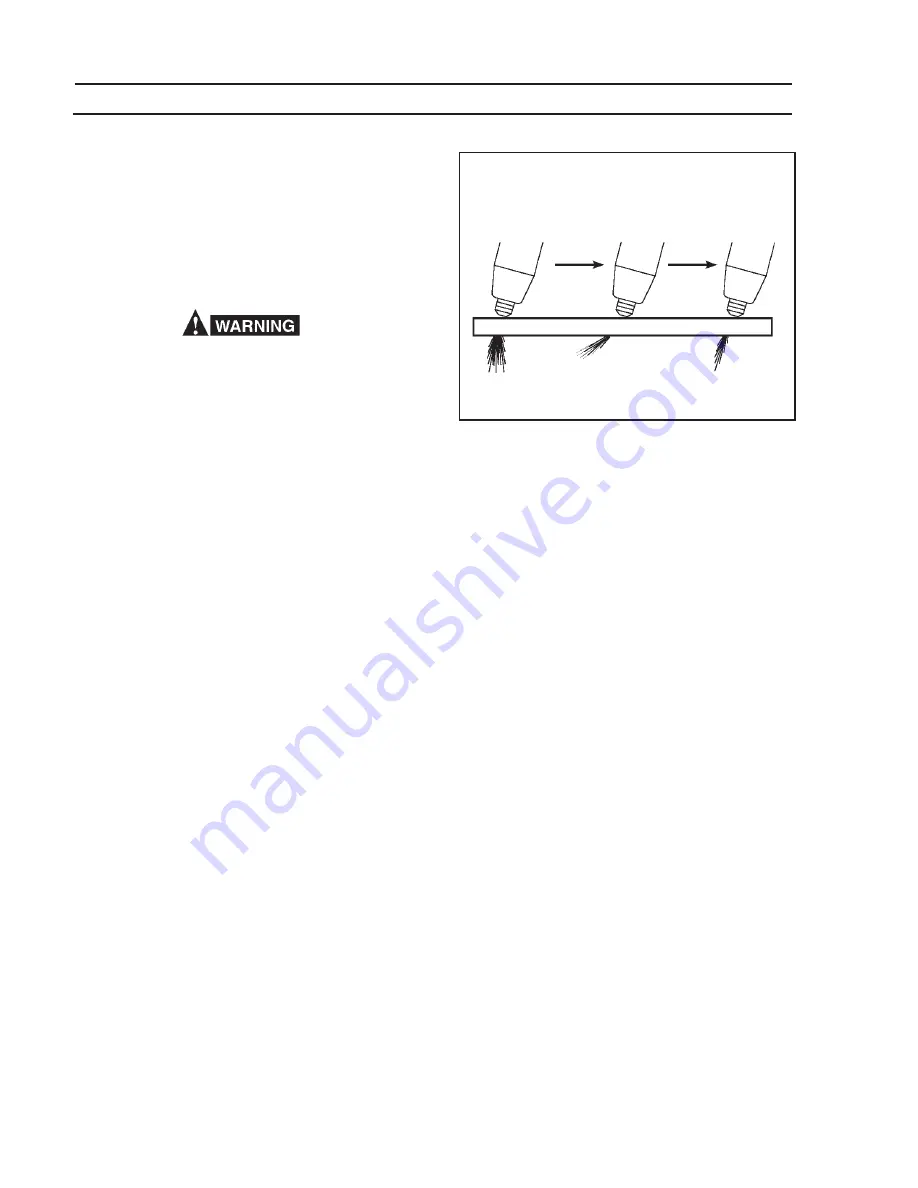
10
a.
The duty cycle of this unit is 30% at rated out-
put current. Duty cycle is based on a 10 minute
cycle; therefore, the unit can operate for a to-
tal of 3 minutes and shut off for cooling a total
of 7 minutes in a 10 minute period.
OPERATION
Wear the usual protective gloves, clothing and hel-
met. Helmet with filter lens shade No. 6 to 8 should
provide adequate protection.
Never touch any parts forward of the torch handle
(tip, heat shield, electrode, etc.) unless the power
switch is in the OFF position.
Do not depress the torch switch unless the torch
tip is touching or within 0.020-in. (less than 1/32-in.)
of the workpiece.
CAUTION: Locate the console at least 10-ft. from the
cutting work area. Chips and hot slag, from
the cutting operation, can damage the con-
sole.
After plugging in the input power cable, and turning the
power swithc on:
1.
Touch the tip of the torch to the workpiece (or within
0.020 in. of the workpiece) holding the torch at
about 15- 30
o
angle to avoid damaging the tip.
2.
Depress the torch switch. (Air should begin flow-
ing and H.F. should come on.)
3.
Two seconds after depressing torch switch, the
plasma arc will start cutting.
4.
After starting the cut, the tip can be dragged along
the workpiece.
D. OPERATING TECHNIQUES
1.
Piercing
- Thin materials may be pierced with the
torch touching the work. When piercing thicker ma-
terials (up to 1/8-in.) immediately raise the torch to
1/16 in. standoff after initiating the cutting arc. This
will reduce the chance of spatter entering the torch
and prevent the possibility of welding the tip to the
plate. The torch should be angled at about 30
o
when
starting to pierce, and then straightened after ac-
complishing the pierce.
2.
Grate Cutting
- For rapid restarts, such as grate
or heavy mesh cutting, keep torch switch de-
pressed until entire cutting operation is completed.
This avoids the 2 second preflow portion of the
cutting cycle.
E. COMMON CUTTING FAULTS
Listed below are common cutting problems followed
by probable cause of each. If problems are determined
to be caused by the HANDY PLASMA 125, see your
ESAB representative.
1.
Insufficient Penetration.
a.
Cutting speed too fast.
b.
Damaged cutting tip.
c.
Improper air pressure.
2.
Main Arc Extinguishes.
a.
Cutting speed too slow.
3.
Dross Formation. (In some materials and thick-
nesses, it may be impossible to get dross-free
cuts.)
a.
Cutting speed too fast or too slow.
b.
Improper air pressure.
c.
Faulty tip or electrode.
4.
Double Arcing. (Damaged Tip Orifice.)
a.
Low air pressure.
b.
Damaged cutting tip.
SECTION
4
OPERATION
Fig. 4.1 - Effect of Cutting Speed
CORRECT
TOO FAST
TOO SLOW