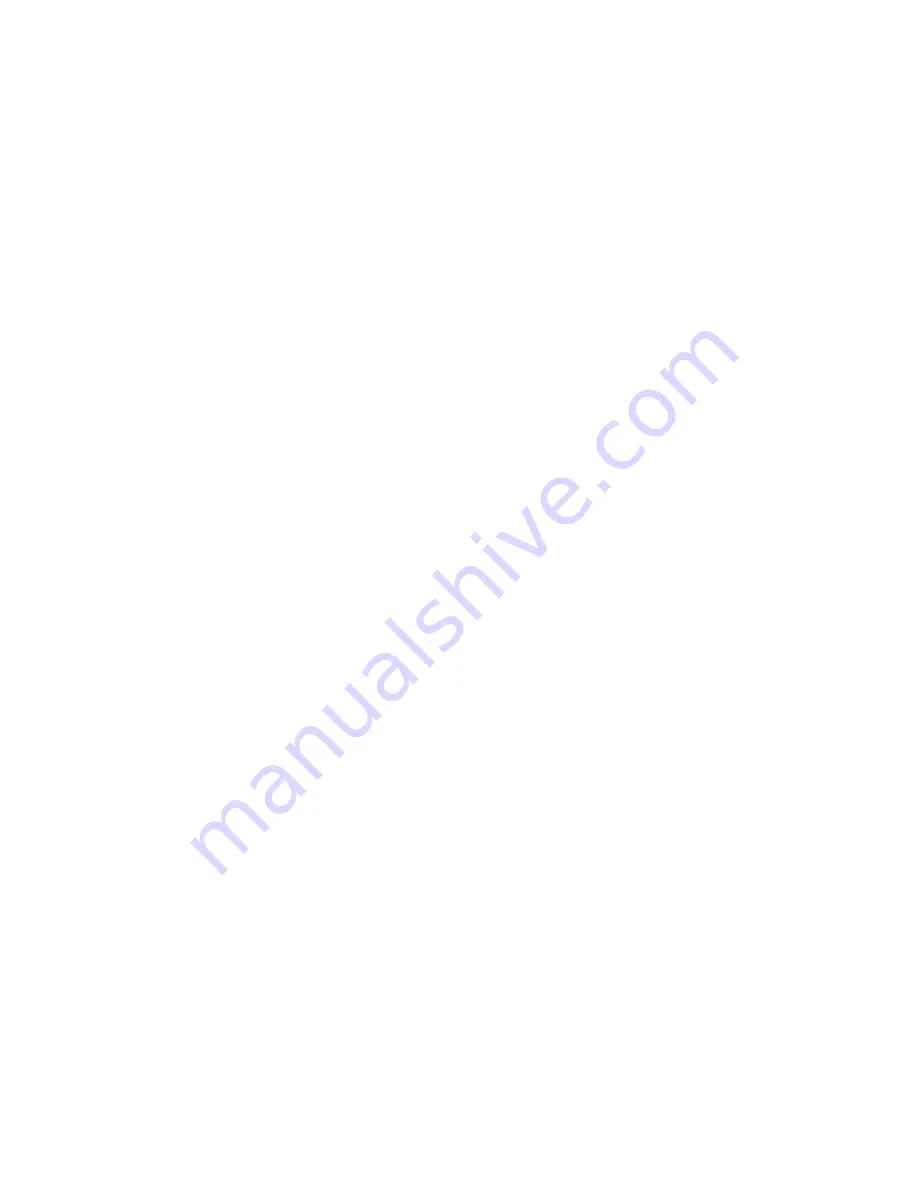
ET 201i DC
OPERATION
0-5452
4-2
A. POWER Indicator
The POWER Indicator illuminates when the ON/OFF switch is in the ON position and the correct mains voltage is present.
B. FAULT Indicator
If Fault indicator lights up continuously then that is an Overcurrent Condition and needs to be serviced by an Autho-
rized ESAB Technician.
C. TRIGGER Mode Switch (LIFT TIG Mode Only)
2T (Normal) Mode
Press the TIG Torch Trigger Switch or Foot Control and hold depressed to weld. Release the TIG Torch Trigger Switch
or Foot Control to stop welding. Down Slope operates in LIFT TIG/HF TIG (GTAW) mode only. While welding if the TIG
Torch Trigger Switch is released, the welding current ramps down to zero current over a defined period of time. The
time period is determined by the Down Slope Control Knob (F).
4T (Latch) Mode
This mode of welding is mainly used for long weld runs. The operator need only to press the TIG Torch Trigger Switch to
activate and then release the TIG Torch Trigger Switch to continue to weld, then press the TIG Torch Trigger Switch again
and release the TIG Torch Trigger Switch to stop welding. This eliminates the need for the operator to depress the TIG Torch
Trigger Switch for the complete length of the weld. The 4T mode incorporates a current slope function which includes a
fixed current up slope of 1 second and an adjustable current down slope. Current slope operates in TIG Mode only. Up
Slope is not adjustable and activates automatically in 4T mode when the TIG torch trigger is depressed. To activate the
Down Slope function in 4T mode while welding, the TIG Torch Trigger Switch must be depressed and held while welding
which will ramp the Welding Current down to zero over a defined period of time. The time period is determined by the
Down Slope Control Knob (F). At any time while welding if the TIG Torch Trigger Switch is depressed and released the arc
will extinguish immediately.
D. Process Selection Switch-
Switches between STICK (SMAW), LIFT TIG (GTAW) and HF TIG (GTAW) modes. Refer to Section 3.06 Setup for STICK
(SMAW) Welding, 3.07 Setup for LIFT TIG (GTAW)Welding and 3.08 Setup for HF TIG (GTAW)Welding.
E. Welding Current Control
The welding current is increased by turning the Weld Current Control Knob clockwise or decreased by turning the Weld
Current Control Knob counterclockwise. The welding current should be set according to the specific application. Refer to
application notes in this section for further information.
F. Arc Force/Down Slope Control
Arc Force is effective when in STICK (SMAW) Mode only. Arc Force control provides an adjustable amount of Arc Force
(or “dig”) control. This feature can be particularly beneficial in providing the operator the ability to compensate for vari-
ability in joint fit-up in certain situations with particular electrodes. In general increasing the Arc Force control toward ‘10’
(maximum Arc Force) allows greater penetration control to be achieved. Down Slope operates in TIG mode only. It is used
to set the time for weld current to ramp down. Refer to Item C (Trigger Mode Selection Switch) for further information
regarding Downslope operation.
G. Gas Outlet
The Gas Outlet is a 5/8”-18 UNF female gas fitting and is utilized for the connection of a suitable TIG Torch.
H. Post Gas Flow (weld current dependant)
Post Gas Flow is the time Gas flows after the arc has extinguished. The gas flow time is proportional to weld current.
This is used to cool and reduce oxidization of the Tungsten Electrode. For example if the Welding Current is set to
10 amps the Post Gas Flow time will be approximately 3 seconds. For a Welding Current set to 160 Amps the Post
Gas Flow time will be approximately 10 seconds. The Post Gas Flow time cannot be adjusted independently of the
Welding Current.