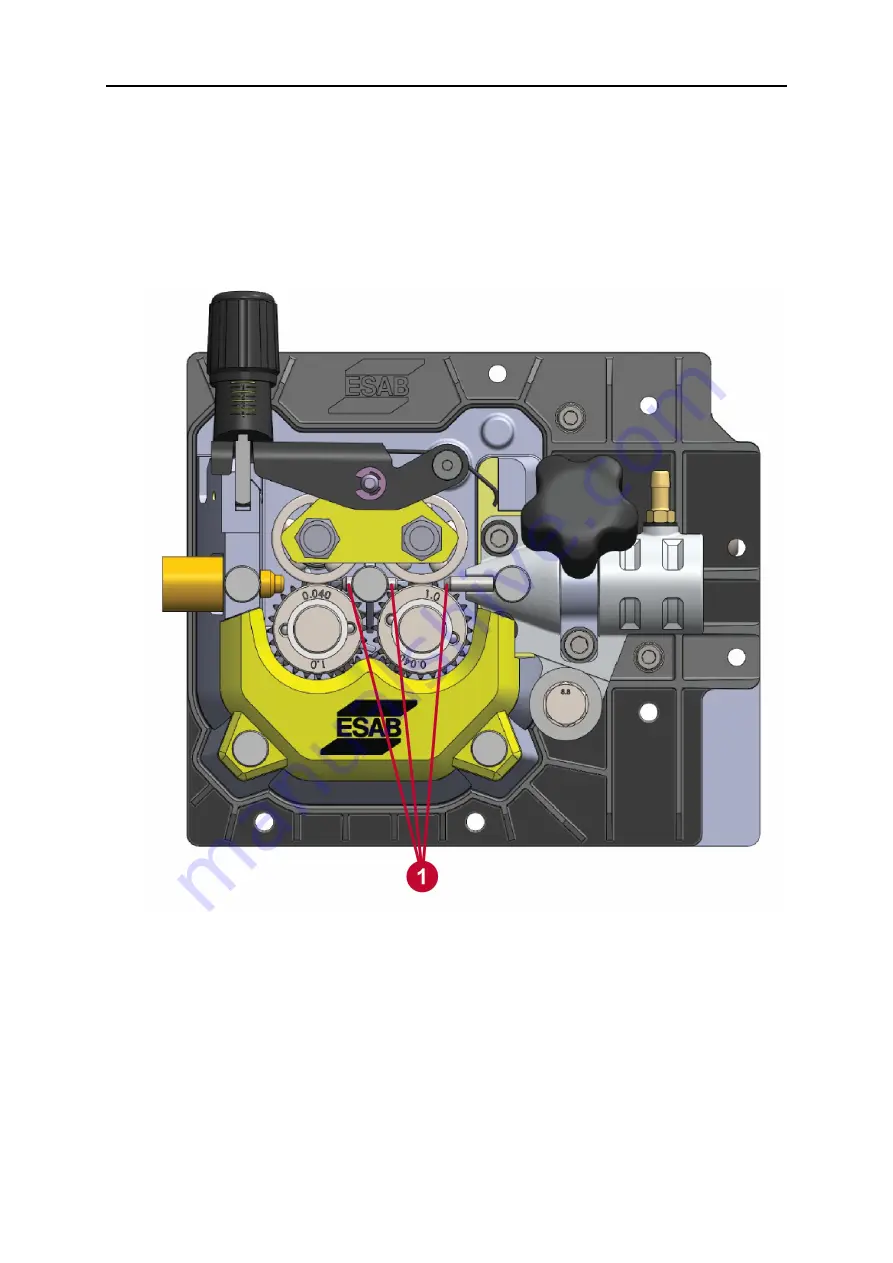
5 OPERATION
0463 618 001
- 51 -
© ESAB AB 2019
5.12.3
Adjusting wire guides
1.
Verify center wire-guide tube has clearance from each feed-roller. The center
wire-guide tube set screw should be finger-tight (see Figure 20 and 18). The center
wire-guide tube requires no adjustment, but it must be inserted completely to assure
clearance from the rollers.
2.
Adjust the output wire-guide tube for 1 mm (0.03 in.) of clearance from the right
feed-roller (see Figure 20), verify center wire-guide tube has clearance from each
feed-roller and tighten its thumb screw finger-tight.
Figure 20. Verify clearance of both guide tubes
1.
Roller and guide tubes
3.
Access the bitter-end of the wire on the bobbin and cut off the length from the bitter
end to have a clean, straight, bitter-end. This is needed to allow a
low-resistance-travel re-install of the wire along the length of the torch cable to the
torch tip.
4.
Feed the wire from the bobbin through the wire-feed guides laying the wire in the
grooves of the wire-feed rollers as shown in Figure 18. Lay the wire into the
inside
groove of the wire-feed rollers. Continue feeding the wire until it projects beyond the
torch-adapter output side by a few centimeters.
5.
Close the pressure rollers on the wire.
6.
Re-connect the torch assembly on the EMP unit.