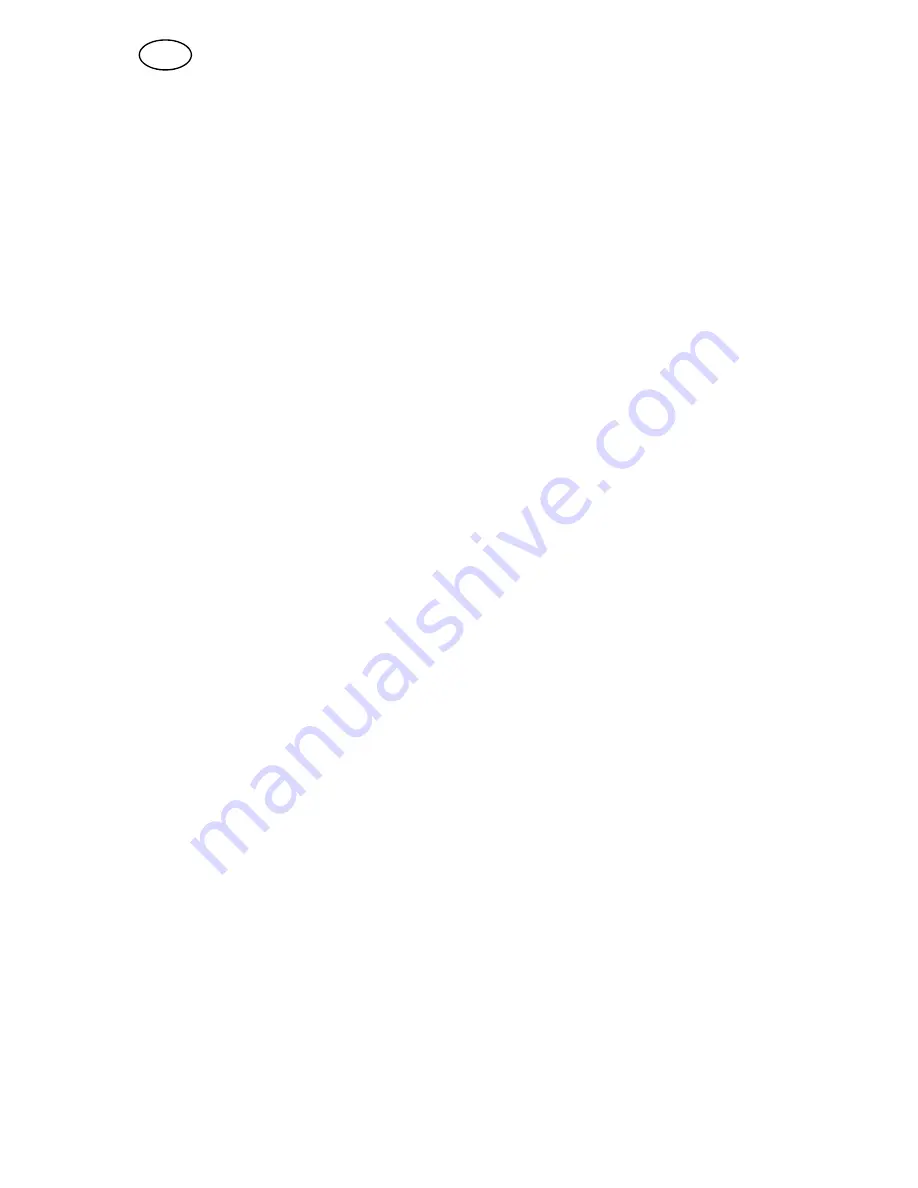
-- 41 --
bt10d12e
5.1
TIG welding with DC
1. Check that the TIG torch, gas hose and return cable are properly connected.
2. Check that a correctly ground thoriated tungsten electrode is fitted to the torch.
3. Use the correct gas and adjust the gas flow to 5--10 l/min.
4. Set the polarity switch SA4 to ”TIG--DC”
5. Set the power switch Q01 to setting ”1” and make sure the flow of cooling air is
not obstructed.
6. Select the start method, HF or tough start.
7. Select local or remote current control using switch SA1.
8. Set the desired current (RP01), slope--up and slope--down times (RP04 and
RP03) and gas post--flow time (RP02).
9. The power source is now ready for welding.
5.2
TIG welding with AC
1. Check that the TIG torch, gas hose and return cable are properly connected.
2. Check that a tungsten or zirconium electrode is fitted to the torch.
3. Use the correct gas and adjust the gas flow to 5--10 l/min.
4. Set the polarity switch SA4 to ”TIG--AC”.
5. Set the power switch Q01 to setting ”1” and make sure the flow of cooling air is
not obstructed.
6. Set switch SA2 to the HF setting.
7. Select local or remote current control using switch SA1.
8. Set the desired current (RP01), slope--up and slope--down times (RP04 and
RP03) and gas post--flow time (RP02).
9.
Adjusting the balance control.
In most situations the balance control can be set to the midway position, so that
the negative and positive half cycles have the same duration. If the knob is
turned clockwise it increases the oxide removal effect of the arc. If it is turned
anticlockwise it reduces the load on the electrode. The setting of the balance
control should be optimised for each individual welding situation.
10. The power source is now ready for welding.
GB