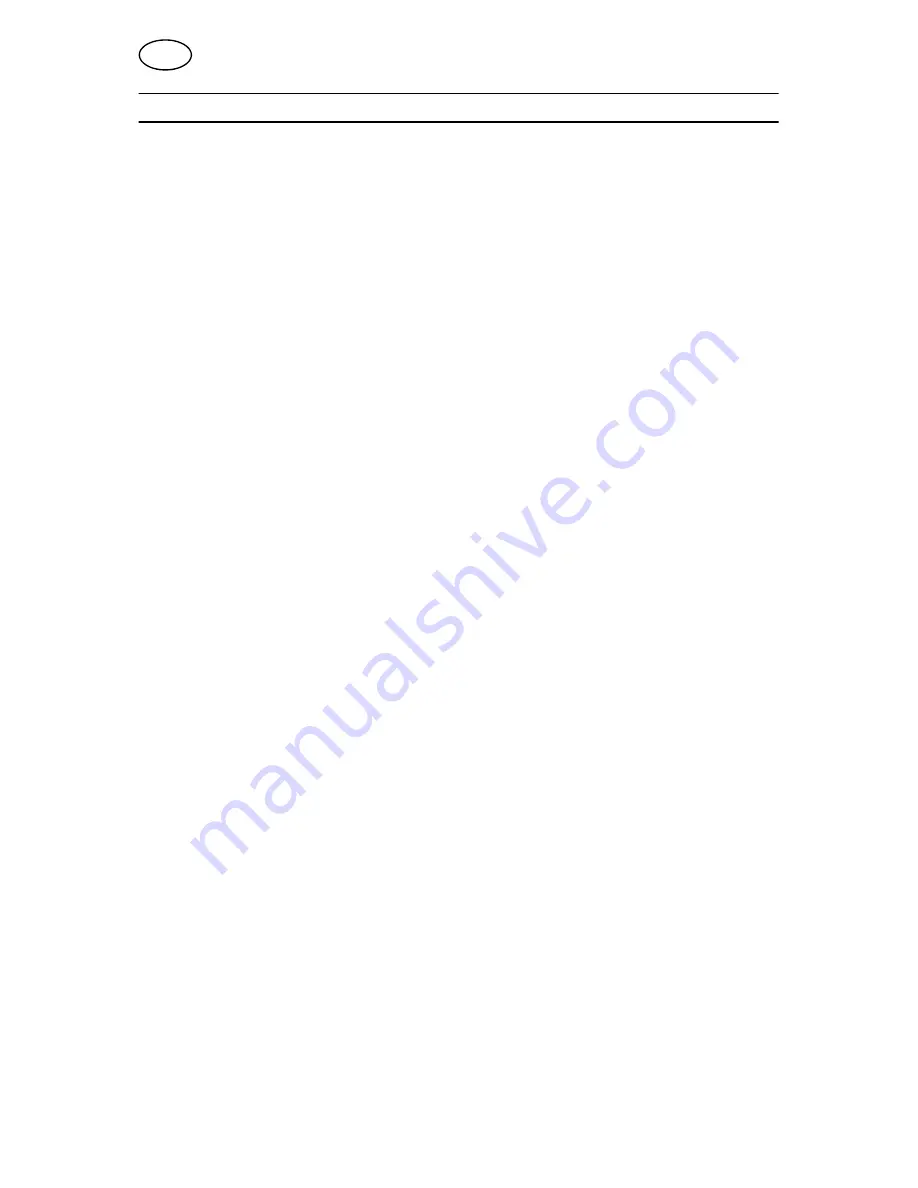
-- 39 --
bt10d12e
5
OPERATION
S
Power switch Q01 for switching power on and off. Indicator lamp lights up and
fan starts in position ”1”.
S
Indicator lamp HL1: indicates that power is on.
S
Indicator lamp HL2: indicates that thermal cut--out has tripped.
S
Potentiometer RP01: for adjusting welding current in range 5--250A.
S
Selector switch SA4: for selecting welding method (TIG or manual metal arc
welding AC or DC).
S
Potentiometer RP04: for adjusting slope--up time 0.5--10 s, during which current
is gradually increased from the minimum current to the set current.
S
Potentiometer RP03: for adjusting slope--down time 0.5--10 s, during which
current is gradually decreased from the set current to the minimum current.
S
Potentiometer RP02: for adjusting the gas post--flow 0.5--30 s, i.e. the time the
gas continues to flow after the arc has died.
S
Selector switch SA2: for choosing between HF start or touch start.
S
Selector switch SA1: for choosing between local or remote control.
Local setting: welding is controlled by power source settings.
Remote setting: welding is controlled by pulse unit or remote unit settings.
S
Remote socket XS1: for connecting remote unit or pulse unit.
S
Selector switch SA3: for 2 stroke/4 stroke.
2 stroke: arc is struck when the torch switch is depressed and extinguished when the
switch is released.
4 stroke: there is no need to keep the torch switch depressed during the welding se-
quence. Press and release the switch to strike the arc. Press and release the switch
again to extinguish the arc.
S
TIG connection XS2 in quick connector for TIG torch, gas and controls.
S
OKC connector XS3. XS4 for return cable and electrode cable.
S
Potentiometer RP05 for balancing square wave output during AC welding.
In most situations the balance control can be set to the midway position, so that
the negative and positive half cycles have the same duration. If the knob is
turned clockwise it increases the oxide removal effect of the arc. If it is turned
anticlockwise it reduces the load on the electrode.
GB