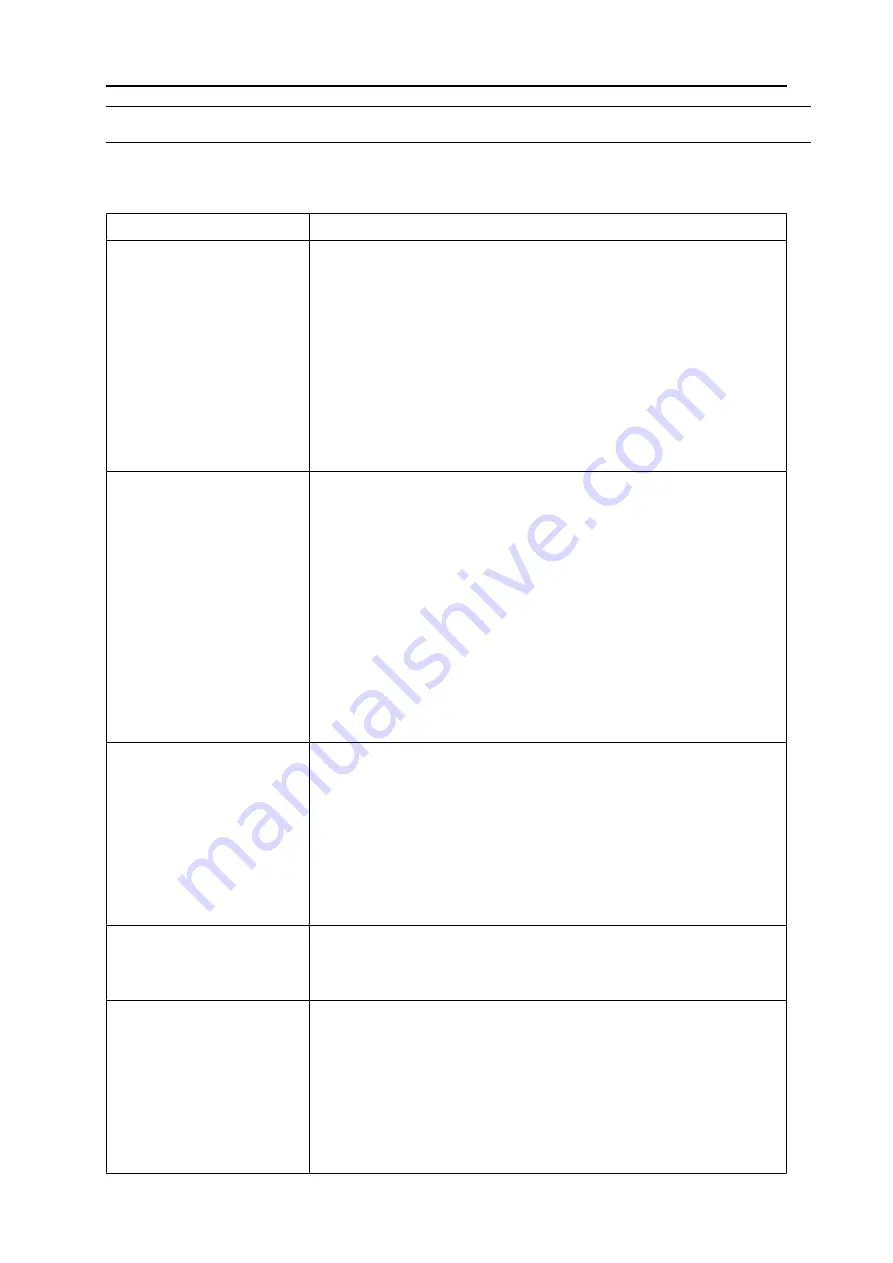
7 TROUBLESHOOTING
0463 709 001
- 23 -
© ESAB AB 2020
7
TROUBLESHOOTING
Perform these checks and inspections before contacting an authorized service technician.
• Check that power is disconnected before starting any type of repair action.
Type of fault
Corrective action
Stick (SMAW) welding
problems
Check that the welding process is set for Stick (SMAW).
Check that the welding and return cables are correctly
connected to the power source.
Make sure that the return clamp has good contact with the
workpiece.
Check that the correct electrodes and polarity are being used.
For polarity, check electrode packaging.
Check that the correct Welding current (A) is set.
Adjust Arc Force and Hot start.
Live TIG (GTAW) welding
problems
Check that the welding process is set for Live TIG as necessary.
Check that the TIG torch and return cables are correctly
connected to the power source.
Make sure that the return clamp has good contact with the
workpiece.
Make sure that the TIG torch lead is connected to the negative
welding terminal.
Make sure that the correct shielding gas, gas flow, welding
current, filler rod placement, electrode diameter and welding
mode on the power source are used.
Make sure that the gas valve on the TIG torch is ON.
No arc
Check that the electrical power supply switch is turned on.
Check that the display is on to verify that the power source has
power.
Check that the setting panel is displaying the correct values.
Check that the welding and return cables are correctly
connected.
Check the electrical power supply fuses.
Welding current is
interrupted during welding
Check whether the Over Temperature LED (Thermal Protection)
on the setting panel is on.
Continue with Troubleshooting "No Arc."
Thermal protection trips
frequently
Make sure that the recommended duty cycle for the weld
current has not been exceeded.
Refer to power source "Duty cycle" section in
Make sure that the air inlets or outlets are not clogged.
Clean the inside of the machine using routine maintenance
methods.