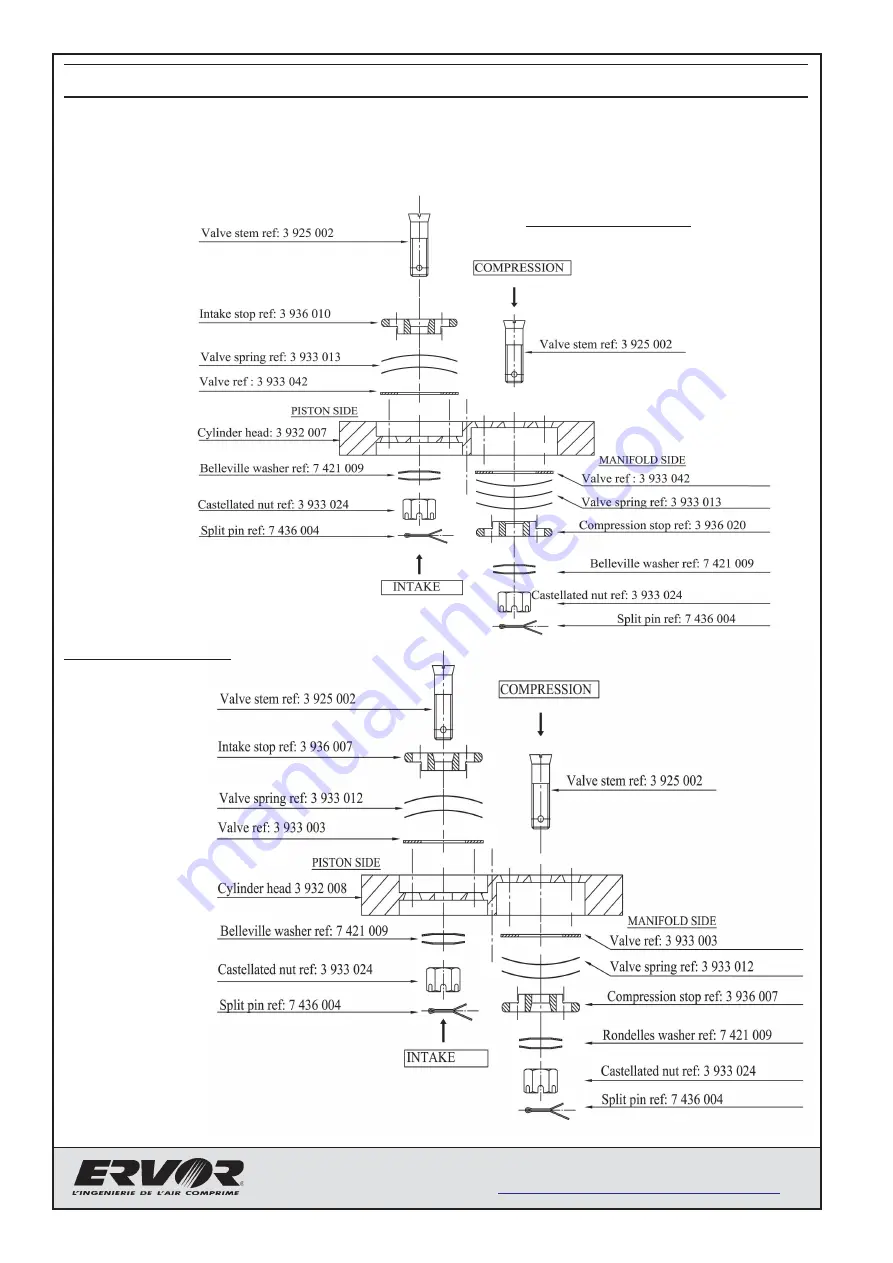
Page 26
ERVOR (SCA) - 6, Rue Désiré Granet - Z.I. du Val d'Argent - 95100 ARGENTEUIL FRANCE
(33) 01 34 11 50 00
(33) 01 34 11 50 10
Web : www.ervor.com - Email : [email protected]
Manual G06
Edition: 10/2015 - rev A
10 - B -
CYLINDER HEADS & VALVES
Intake and compression valves are made of annular discs which operate automatically.
Good water-tightness is necessary between the discs and their seats (avoid running the compressor
with clogged valves, with carbon deposits, oil carbon or more importantly, with broken valves).
Low Pressure stage
High Pressure stage
Summary of Contents for G06
Page 37: ......