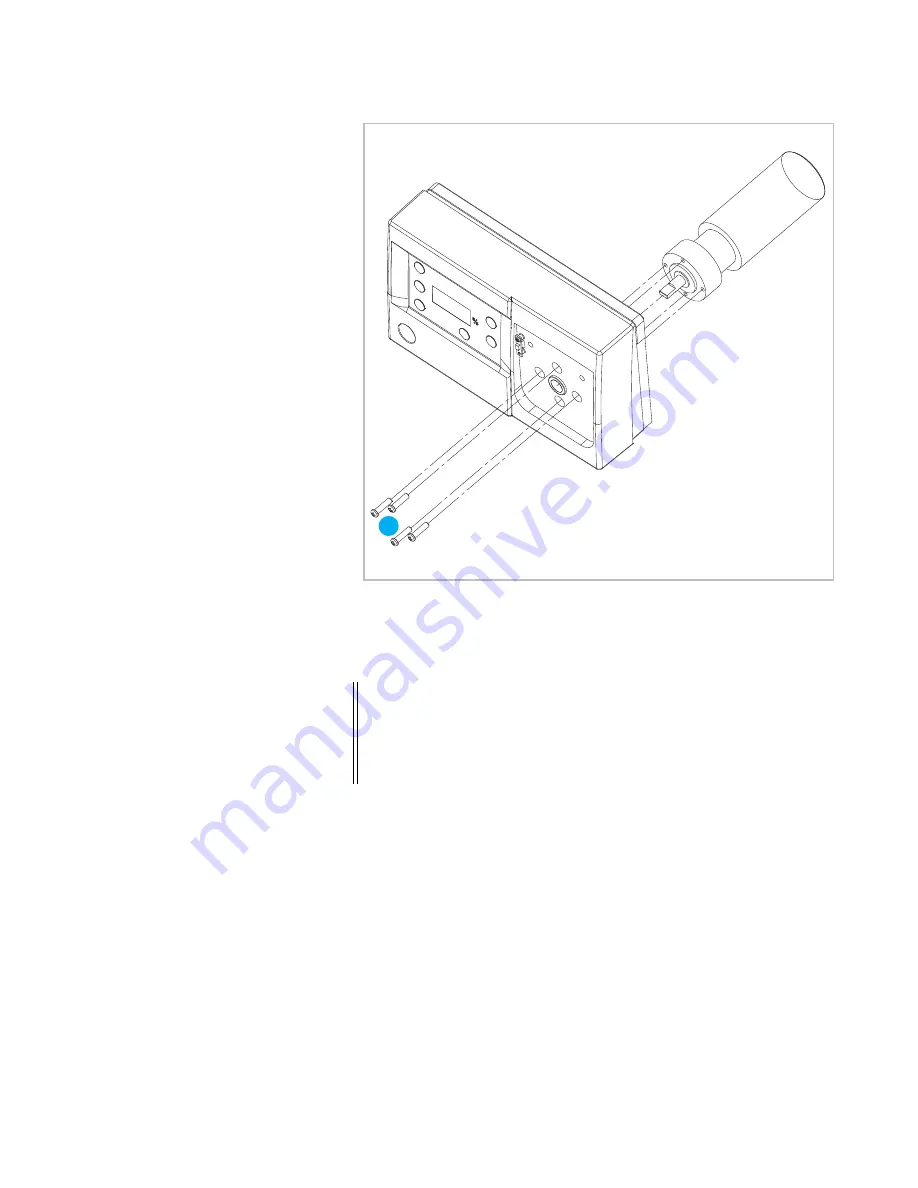
43
/ 56
10
•
Replacing components
801
16-
261
201
8-
07
Change gear motor
11. Undo screws on the gear motor (4) and remove the gear motor to the
rear.
12. Fit a new gear motor in reverse order.
13. Fit front frame in reverse order.
14. Close housing cover.
11
ATTENTION!
Check line voltage setting
The EIP 2 can be operated on a line voltage of 230 V, 120 V, or 100 V.
Therefore, every time the unit is opened always check afterwards
whether the correct line voltage ±10 % is set on the line voltage selec-
tor switch on the main board.
Summary of Contents for EIP 2
Page 1: ...2018 07 80116 261 SERVICE MANUAL EIP 2 V 1 0 x V 1 1 x ELECTROSURGERY ...
Page 2: ......
Page 3: ...SERVICE MANUAL EIP 2 ...
Page 10: ...2 Modifications 10 56 80116 261 2018 07 ...
Page 18: ...5 Installation 18 56 80116 261 2018 07 ...
Page 19: ...19 56 6 Circuit Descriptions 80116 261 2018 07 CHAPTER 6 Circuit Descriptions ...
Page 24: ...6 Circuit Descriptions 24 56 80116 261 2018 07 ...
Page 46: ...10 Replacing components 46 56 80116 261 2018 07 ...