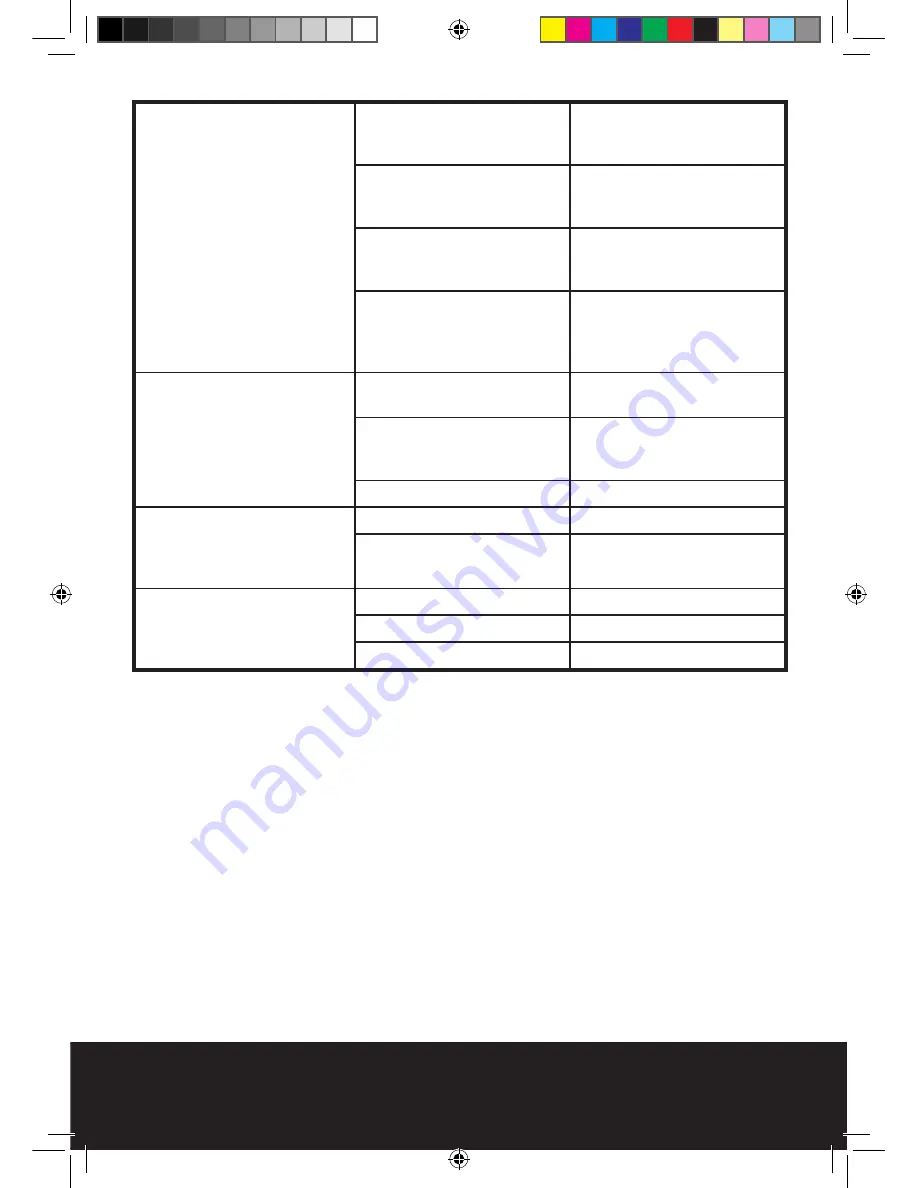
8” THICKNESS PLANER
The motor cuts out whilst
under load.
Motor has exceeded
its duty cycle and the
overload has cut in.
Allow the motor to cool
and reset the overload.
Cutting depth is too great
so the overload has cut in.
Allow the motor to cool
and reset the overload.
Reduce the cutting depth.
Feed rate is too fast so the
overload has cut in.
Allow the motor to cool
and reset the overload.
Reduce the feed rate.
Dull cutter blades so the
overload has cut in.
Replace or sharpen the
blades, allow the motor
to cool and reset the
overload.
Poor finish on workpiece.
Dull or damaged blades.
Replace or sharpen the
blades.
Uneven feed rate.
Ensure constant pressure
on the wor piece whilst
planing.
Feed rate too fast.
Reduce the speed of feed.
Extraction port becomes
blocked whilst thicknessing
(without external
extraction).
Cutting depth too great.
Reduce the cutting depth.
Wood is too damp.
Allow the wood to dry.
Extraction port becomes
blocked whilst planing
(without external
extraction)
Cutting depth too great.
Reduce the cutting depth.
Feed rate too fast.
Reduce the feed rate.
Wood is too damp.
Allow the wood to dry.
BTP210F-M-070928.indd 25
2007-9-28 13:36:04