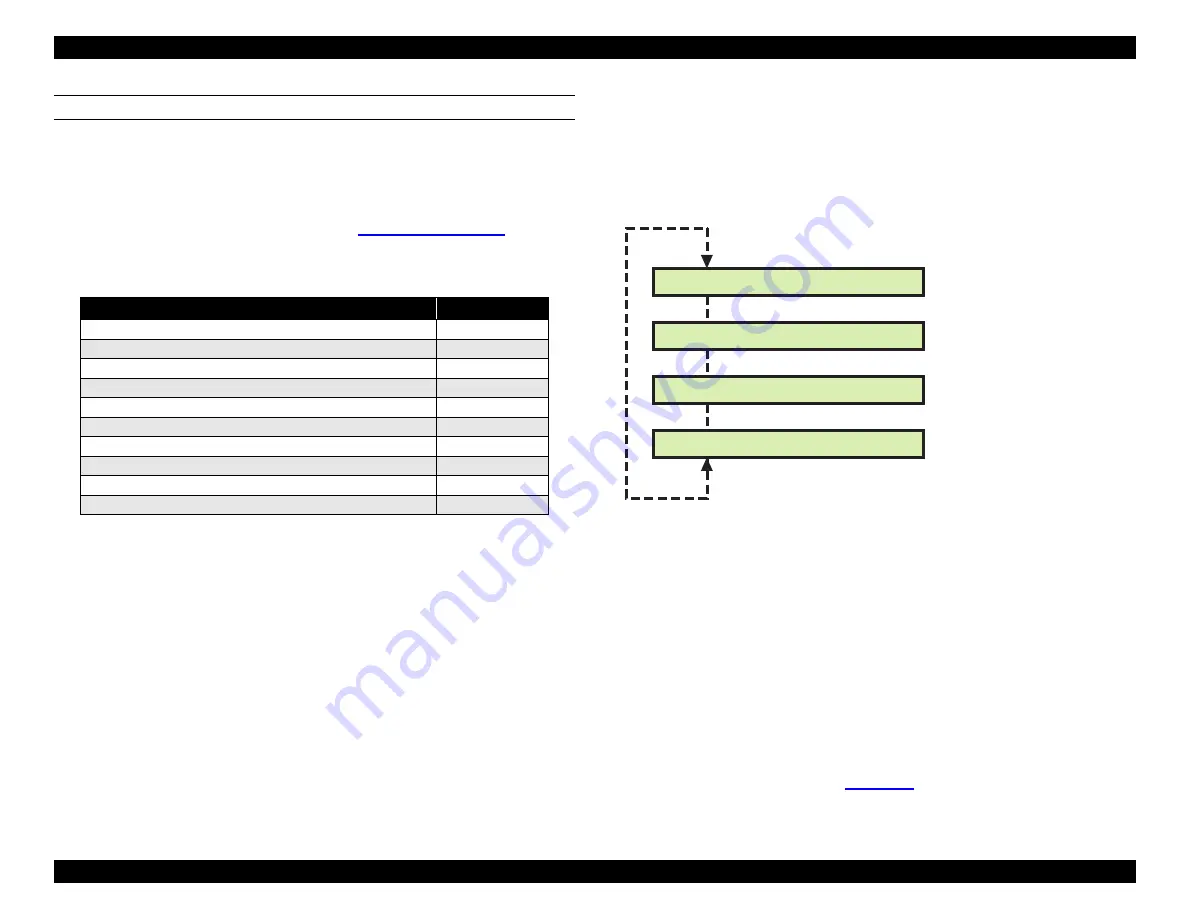
EPSON Stylus Pro 9000
Adjustments
128
COUNTER CLEAR
This function resets all the counters stored in memory on the Main Board to
their original condition. Remove the old ink cartridges before resetting the
counters; when you turn on the printer, the printer prompts you to install new
cartridges.
If you need to reset counters individually, see
Note *: "1" means the flag is set, and the next time power is turned on the printer will
perform an initial ink charge.
5.3.5 Cleaning menu
Using this menu, you can select a cleaning mode and start that cleaning
operation. You can also cause the printer to perform the initial ink charge
operation without resetting the initial ink charge flag.
Std. KK0 (CL1)
Normal cleaning cycle
Volume of ink cleared = low
Std. KK1 (CL1’)
Strong cleaning cycle
Volume of ink cleared = medium
Rubbing = off
Std. KK2 (CL2)
Strong cleaning cycle
Volume of ink cleared = high
Rubbing = on
Init. Fill
Perform initial ink charge sequence
5.3.6 Print menu
The Print menu performs the same functions as the "Test Print" option on the
Adjustment menu. For details, see
Table 5-11. Counters Reset by "Counter Clear"
Counter
Reset Value
Protection Counter A/B (for waste ink pads)
0
Ink Volume Counter Rb/ Ry/ Rx Rz
0
Consumed Ink Counter Cb/ Cy/ Cm/ Cc/ Cml/ Ccl
0
Power Cutoff Timer T2
0
Accumulated Prints Timer
0
CL Timer
0
CL Timer 3
0
CL Flag
0
Initial Charge Flag
1*
Periodic Pseudo-Vacuum Flag
0
[SelecType]
[Paper Source]
Cleaning: Std. KK0
Cleaning: Std. KK1
Cleaning: Std. KK2
Cleaning: Init. Fill
Performs the initial ink
charge operation
[Enter]
Summary of Contents for Stylus Pro 9000 - Print Engine
Page 1: ...EPSONStylusPro9000 Wide Format Professional Inkjet Printer TM PRO9000 ...
Page 10: ... PRINTERBASICS ...
Page 21: ... TECHNICALOVERVIEW ...
Page 38: ... TROUBLESHOOTING ...
Page 54: ... DISASSEMBLY ASSEMBLY ...
Page 101: ... ADJUSTMENTS ...
Page 137: ... MAINTENANCE ...
Page 145: ... APPENDIX ...
Page 182: ...STYLUS PRO 9000 PM 9000C No 3 Rev 01 10052 PF Rail Assembly CAT 5003 201 202 ...
Page 197: ......
Page 198: ......