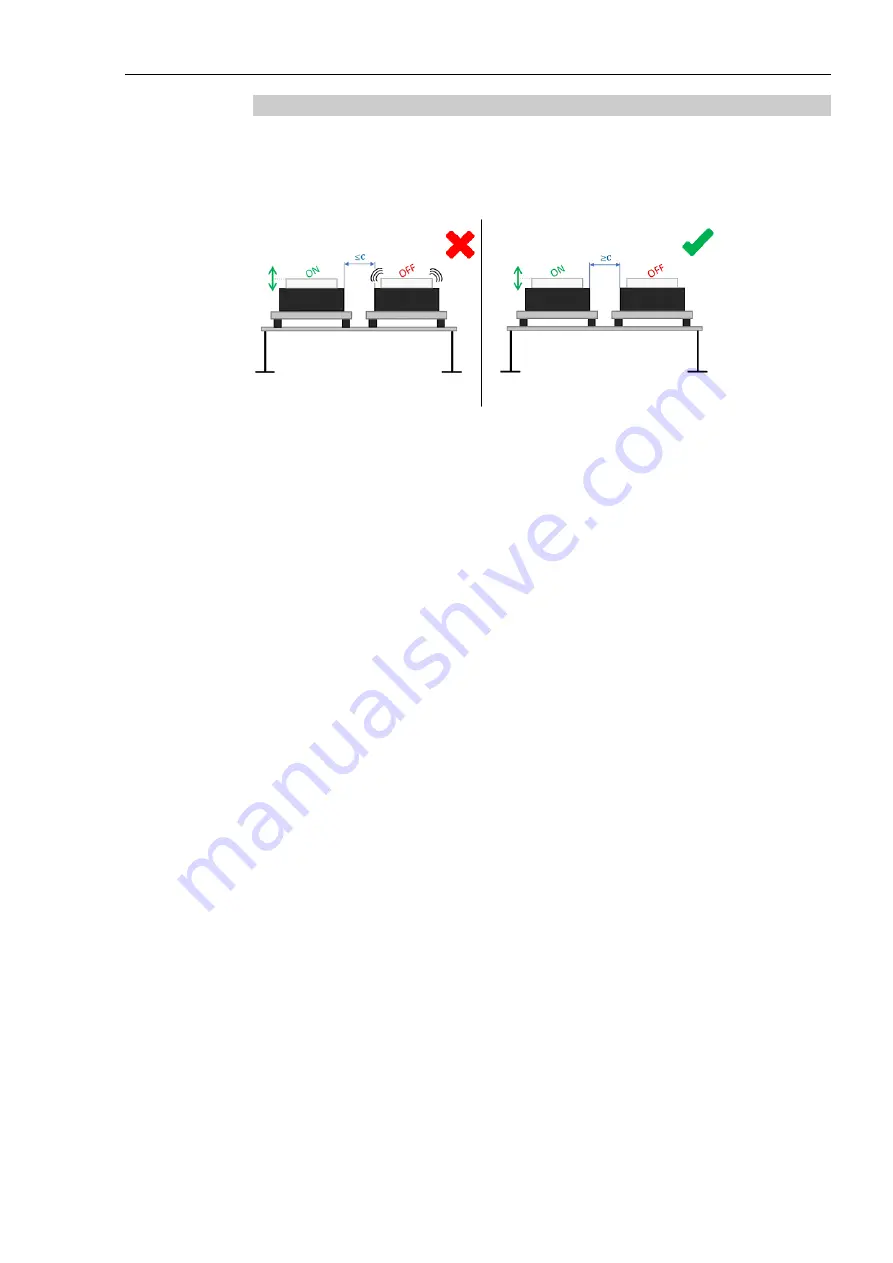
3. Environment and Installation
Part Feeding 7.0 IF-80 Rev.3
25
3.5.4 Minimal Distance Between Part Feeding
When two or more feeders are installed close to each other, the movement of the active
device can excite the passive one. It is therefore recommended to install the feeders at
enough distance to prevent them from disturbing each other.
The minimal distance between Part Feeding, refer to
3.5.5.4. Minimal Distance Between
Part Feeding.