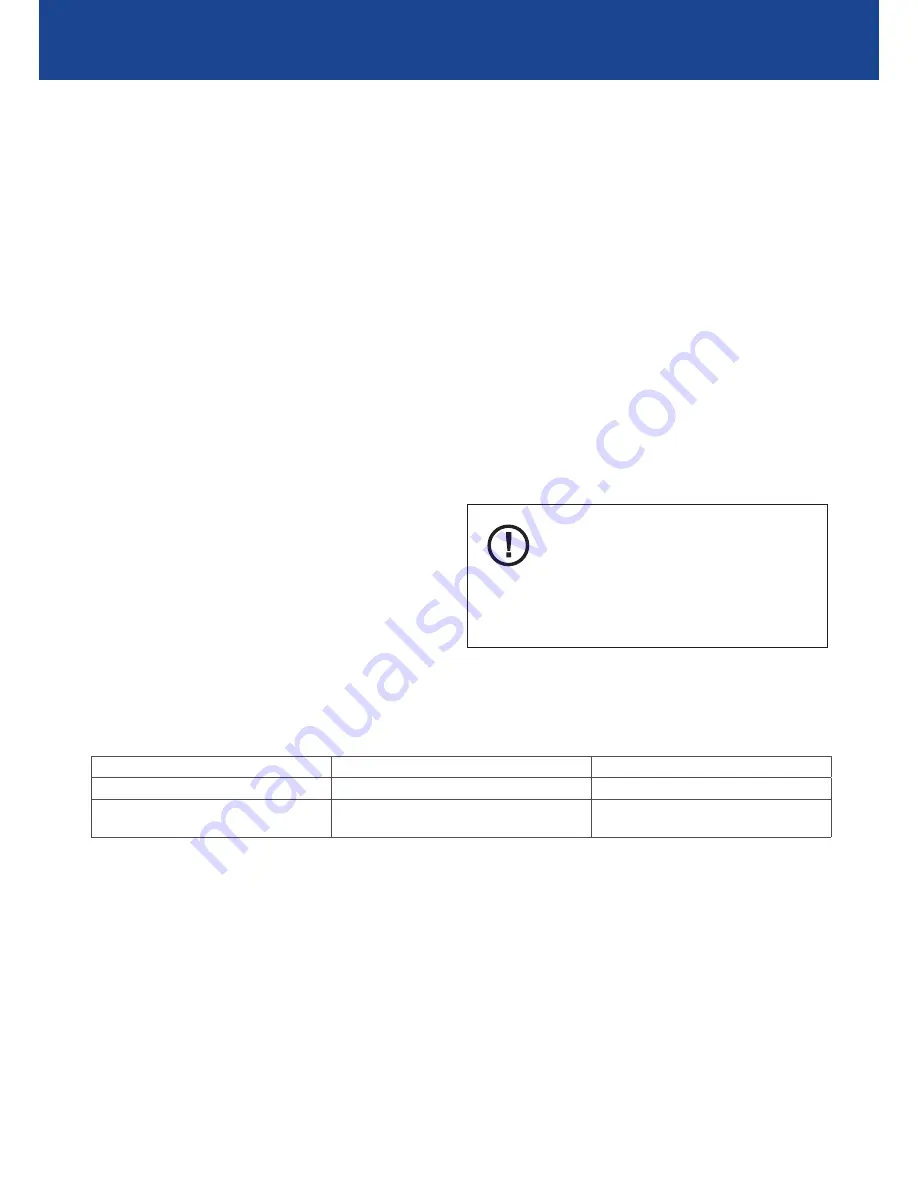
www.enware.com.au
Call 1300 369 273
7
The ENWARE AQUABLEND Thermostatic Mixers should be
installed using the appropriate Standard, Code of Practice and
legislation applicable to each state and following the details
outlined in this section.
They must be installed by a licensed plumber, or where
applicable, a licensed plumber who has undertaken accredited
training in Thermostatic Mixing Valves.
Note: To effectively control microbial hazards during system
design, installation, commissioning and maintenance, the
requirements outlined in AS/NZS3666 and local legislation
shall be adhered to.
If the valve is not installed correctly then it will not function
correctly and may put the user in danger. It may also void the
warranty of the valve.
Prior to the installation of the valve, the system must be
checked to ensure that the system operating conditions
fall within the recommended operating range specified in
‘Technical Information -Installation Conditions’.
To ensure that the Thermostatic mixer operates correctly,
it is necessary that the pipework is thoroughly flushed with
clean water before it is installed as per AS/NZS 3500.1. This
will remove any physical contaminants from the pipework,
ensuring trouble-free operation. During the flushing procedure
care should be taken to prevent water damage occurring to
the surrounding area.
WARNING: Do not cut the electrical cable
of the sensor tap, or alter the product
in any way to suit installation. Damage
caused in this way will void warranty.
Transformer with 4.5m Extended Cable (ENMS230)
are available if extra power cable length is required
TOOL REQUIRED
Supplied service & Allen keys
3mm Allen Key or flat head screwdriver
3/8” Flat end Allen key
Phillips head screw driver
Spirit level
Spanner
Loctite 577 thread sealant or
equivalent
INSTALLATION
Summary of Contents for AQUABLEND ESQX TOUCH FREE SERIES
Page 36: ......