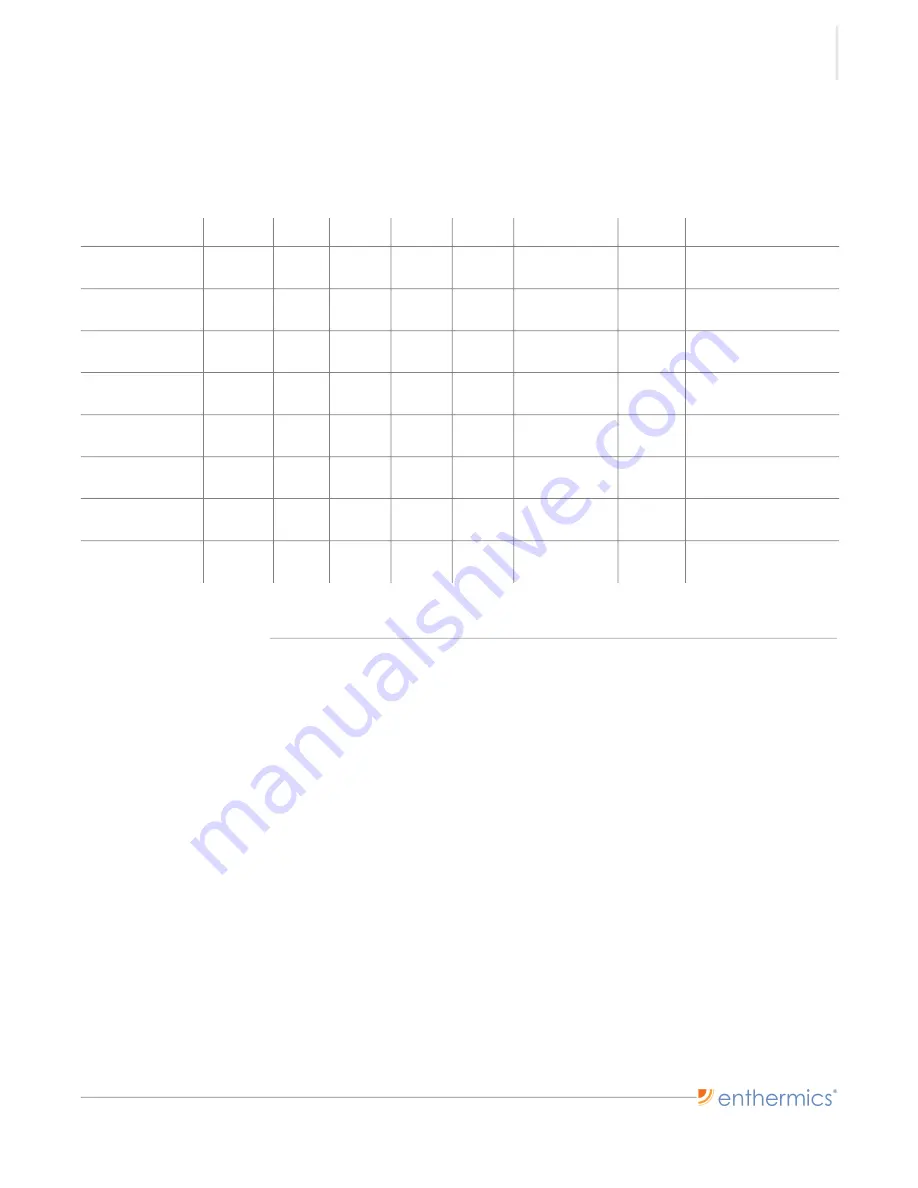
O
PERATION
Combination Blanket/Fluid Warmer
▪
Operator’s Manual
▪
MN-39940
▪
Rev 3
▪
8/20
37
Continued from previous page
Viewing data in
Microsoft® Excel
The table below is an example of temperature data from the warmer.
Result
The temperature data has now been viewed.
Time Stamp
Chamber Mode
Power
Door
Fan
Temperature Set-point
Errors
12/19/2018 14:48
bottom
off
closed
off
71.7
130
Diagnostics.SensorSho
rtErrors=0x0c
12/19/2018 14:48
top
off
closed
off
71.2
104
Diagnostics.SensorSho
rtErrors=0x0c
12/19/2018 14:53
bottom
on
closed
on
71.7
130
Diagnostics.SensorSho
rtErrors=0x0c
12/19/2018 14:53
top
INJ
on
closed
on
70.4
104
Diagnostics.SensorSho
rtErrors=0x0c
12/19/2018 14:58
bottom
on
closed
on
71.7
130
Diagnostics.SensorSho
rtErrors=0x0c
12/19/2018 14:58
top
INJ
on
closed
on
70.4
104
Diagnostics.SensorSho
rtErrors=0x0c
12/19/2018 15:03
bottom
on
closed
on
71.7
130
Diagnostics.SensorSho
rtErrors=0x0c
12/19/2018 15:03
top
INJ
on
closed
on
70.3
104
Diagnostics.SensorSho
rtErrors=0x0c