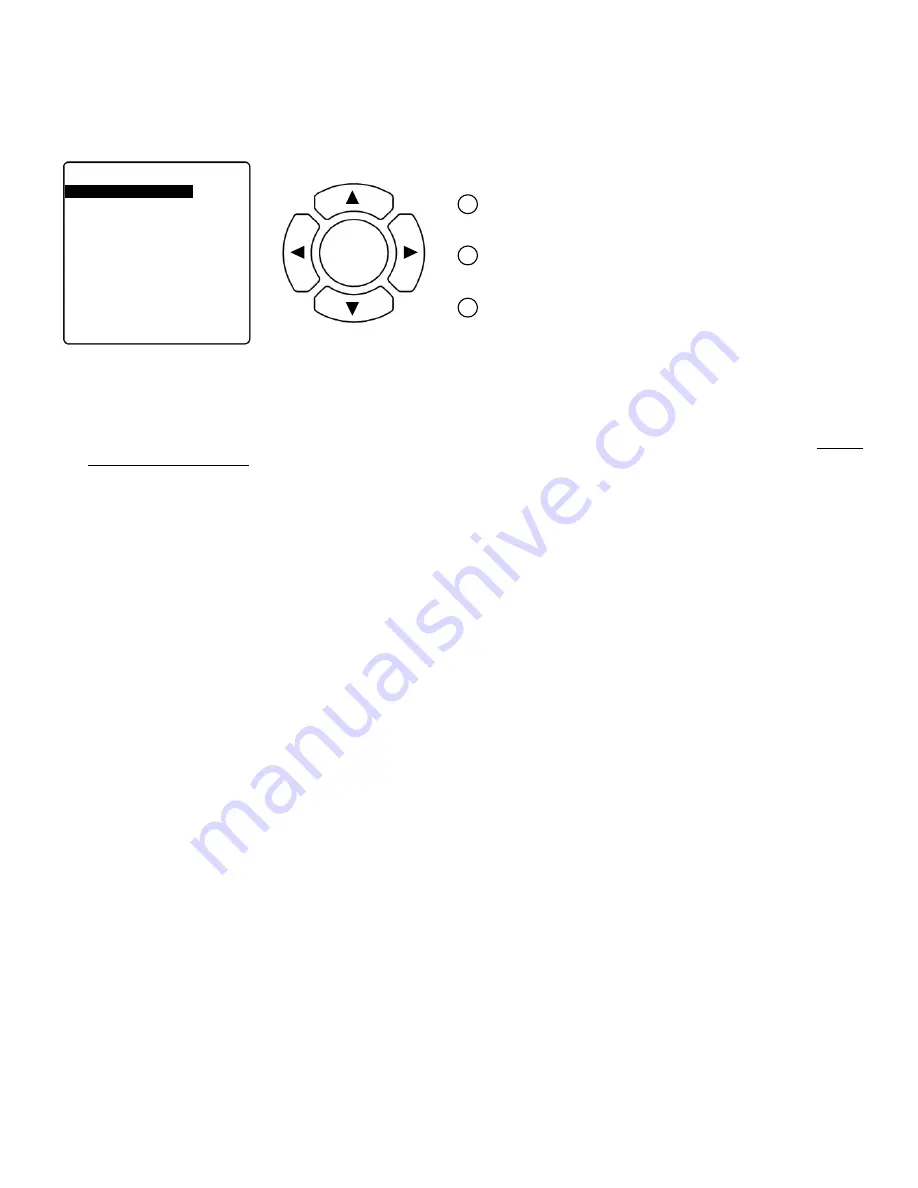
Accel CS Boiler - Gas Heat - Eighth Edition – January, 2015
45
combustion analyzer. Make sure to tighten inlet pressure tap, offset cap screw and combustion test port.
11. The target O2 reading is 4.5%. The valve used in the EK1C and EK2C boilers is capable of holding 4.5% O2 plus or
minus 0.2% O2. Maximum allowable deviation for all sizes is plus or minus 0.5% O2, or from 4.0% O2 to 5.0% O2
Method 2:
If the
INFO > Test
screen displays three options as shown, the following setup procedure may be used:
1. Perform carbon monoxide test two minutes after light off. If the carbon monoxide exceeds 400 ppm air-free after two
minutes of operation, shut off boiler immediately and repeat "Prepare for Start Up" checklist.
2. Set appliance minimum and maximum ‘modulation rate’ to min and max desired fan speed, respectively:
INFO > Advanced Setup > Modulation Config
. Use left and right arrows only. To delete prior setting, arrow to DEL
and press OK until cleared, then use arrows to enter the min/max fan speed.
See Fan Speed chart in section Length
of Run, Intake and Vent for fan speed ranges
.
Selecting fan speeds outside the recommended ranges may cause a
lockout.
3. Navigate to test mode menu:
INFO > Test > Forced Rate
. Select “Set Low Fire” and press the OK button, wait (2)
seconds to be sure “Manual firing rate” displays the desired fan speed. Repeat with “Set High Fire”. Select “Start
Test”.
4. Check that O2 reading is 4.5% and adjust throttle screw if necessary. Turn throttle screw clockwise to increase O2 and
counter clockwise to decrease O2 for EK1Cs and EK2Cs. For EK3Cs, the throttle valve can be turned continuously (4
full turns of the throttle adjustment screw will leave the throttle back at the starting point)--turn in one direction and note
if the O2 increased or decreased, and proceed using that as a reference to adjust the screw in the proper direction to
set the O2 reading to 4.5%.
If additional time is needed, the test may be restarted by selecting “Stop Test” and
pressing the OK button, and then immediately pressing the OK button again. The test can also be restarted after the 5
minute time limit has expired by selecting “Start Test” and pressing the OK button.
5. Keep appliance running until stabilized, about 15 to 20 minutes, make adjustment when necessary.
6. Set appliance to minimum fire by selecting “Set Low Rate”.
7. Remove cap screw with a Torx T-40 screw driver or 5 mm hex key to expose offset adjustment screw.
8. Check that offset O2 reading is 4.5% and adjust if necessary- clockwise to lower O2 (raise CO2, or make mixture
richer) and counterclockwise to raise O2 (lower CO2, or make mixture leaner).
9. Reset appliance max fan speed to max RPM (see Item 2 above). Verify speed is at max fan speed.
10. Repeat steps 2 through 8 inclusive when adjustment of offset pressure was necessary, resetting maximum fire to max
RPM. The test mode will run for 5 minutes before reverting to auto modulation.
11. After adjustments are made, stop appliance, disconnect pressure gauge and combustion analyzer. Make sure to
tighten inlet pressure tap, offset cap screw and combustion test port.
12. The target O2 reading is 4.5%. The valve used in the EK1C and EK2C boilers is capable of holding 4.5% O2 plus or
minus 0.2% O2. Maximum allowable deviation for all sizes is plus or minus 0.5% O2, or from 4.0% O2 to 5.0% O2
What if the fire goes out when you adjust the fan speed to minimum?
When this happens it means the valve is far enough out of offset adjustment that at low fan speeds the flame signal drops
below minimum. Example: Upon a hot water call, the burner lights at the light off speed of 3600 rpm, and then the burner
ramps up to maximum fan speed. Measure the oxygen level and adjust the gas valve main throttle screw as needed. Next
change the fan speed to minimum, and as the fan speed ramps down, the flame signal drops below minimum due to a large
change in the oxygen level, and the burner shuts off. In order to keep the burner running long enough to adjust the offset,
set the minimum fan speed to 2500 rpm and the flame should stay lit long enough for you to adjust the valve offset to a
reasonable setting. Then lower the minimum fan speed in steps such as 2000 rpm or 1200 rpm, and again adjust the gas
valve offset as needed.
Final checkout of the installation
After any adjustment, set appliance in operation. Observe several complete cycles to ensure that all burner components
function correctly.
OK
HOME
INFO
BACK
Test
Forced Rate
_____________
Manual Burner Operation
Manual Pump Operation
Summary of Contents for EK1C
Page 60: ...Accel CS Boiler Gas Heat Eighth Edition January 2015 59 DRAWINGS WIRING...
Page 61: ...Accel CS Boiler Gas Heat Eighth Edition January 2015 60 DRAWINGS WIRING...
Page 62: ...Accel CS Boiler Gas Heat Eighth Edition January 2015 61 DRAWINGS WIRING...
Page 63: ...Accel CS Boiler Gas Heat Eighth Edition January 2015 62 DRAWINGS WIRING...
Page 64: ...Accel CS Boiler Gas Heat Eighth Edition January 2015 63 DRAWINGS WIRING...
Page 65: ...Accel CS Boiler Gas Heat Eighth Edition January 2015 64 DRAWINGS WIRING...
Page 66: ...Accel CS Boiler Gas Heat Eighth Edition January 2015 65 DRAWINGS WIRING...
Page 71: ...Accel CS Boiler Gas Heat Eighth Edition January 2015 70...
Page 72: ...Accel CS Boiler Gas Heat Eighth Edition January 2015 71 THIS IS A BLANK PAGE...