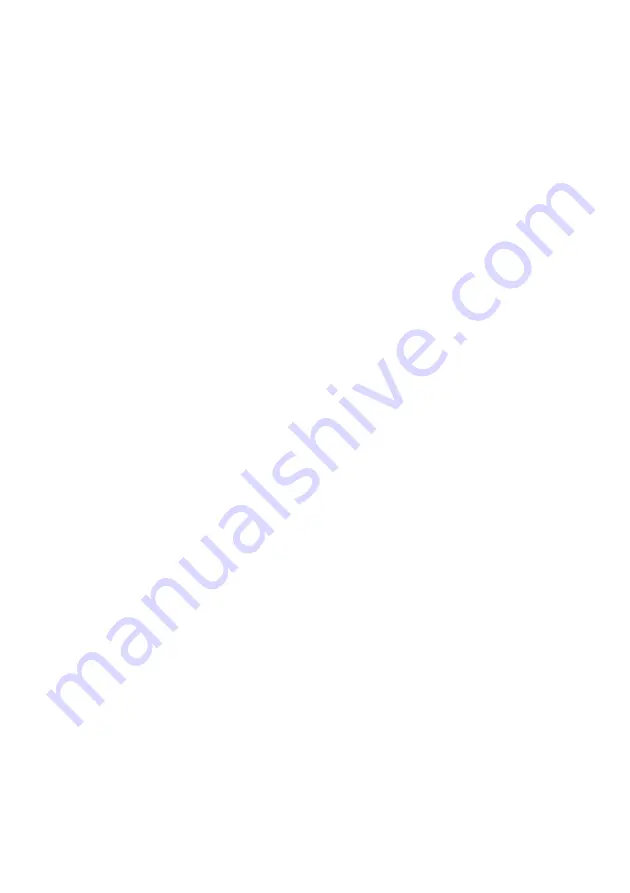
2
1. INTRODUCTION
This manual contains information that will allow to take full advantage of
ENEL200TH welding machine operation values and enable its safe use.
Before operating the product, be sure to read this manual.
2. APPLICATION
ENEL200TH welding machine is a modern direct current source designed
mainly for TIG welding and with coated electrodes (MMA) of all types (ER-,
EA-, EB-, ES-, ...) with diameters from
∅
1.6 to
∅
4.0. Due to the high open
circuit voltage (90V) and very good welding properties, the device also allows
welding with cellulose coated electrodes which are used, among others, for
pipelines welding.
When equipped with appropriate TIG welding torch it is possible to weld steel
and its alloys and copper and its alloys using TIG welding (welding with a non-
consumable electrode - mostly tungsten electrode in an inert gas shield, such
as argon). The ignition of the arc is non-contact (HF) or contact by scratch.
The remote control of the welding current is possible in all operating modes.
A microprocessor controller ensures precision welding, repeatable setting of
many parameters, and simple usage.
Due to the small dimensions and weight, and resistance to large voltage
fluctuations, the ENEL200TH welder is particularly useful for operation in
difficult field conditions when installing any type of welded structures,
pipelines, tanks, etc.
The device is designed for operation at ambient temperature from -10°C up to
+40°C and relative humidity up to 90% at temperature of + 20°C. You can not
operate the welder in the rain without an additional protection against water
entering the inside of the device.
3. DESCRIPTION
ENEL200TH welding machine is an inverter direct current source, which uses
an electronic power factor correction circuit (PFC). This way the welder offers
high power with low power consumption from the mains. This current source
is characterised by good dynamics and a smooth and stable arc. It is
lightweight, of small dimensions, resistant to large fluctuations of the mains
voltage. The connecting, control and indicating elements are located on the
front panel. On the rear panel there are: the power switch, the power cord, the
fan, the rating plate and the gas valve connection used to supply shielding
gas from the cylinder. Control and indicating elements of the welder are
shown in Fig. 1.