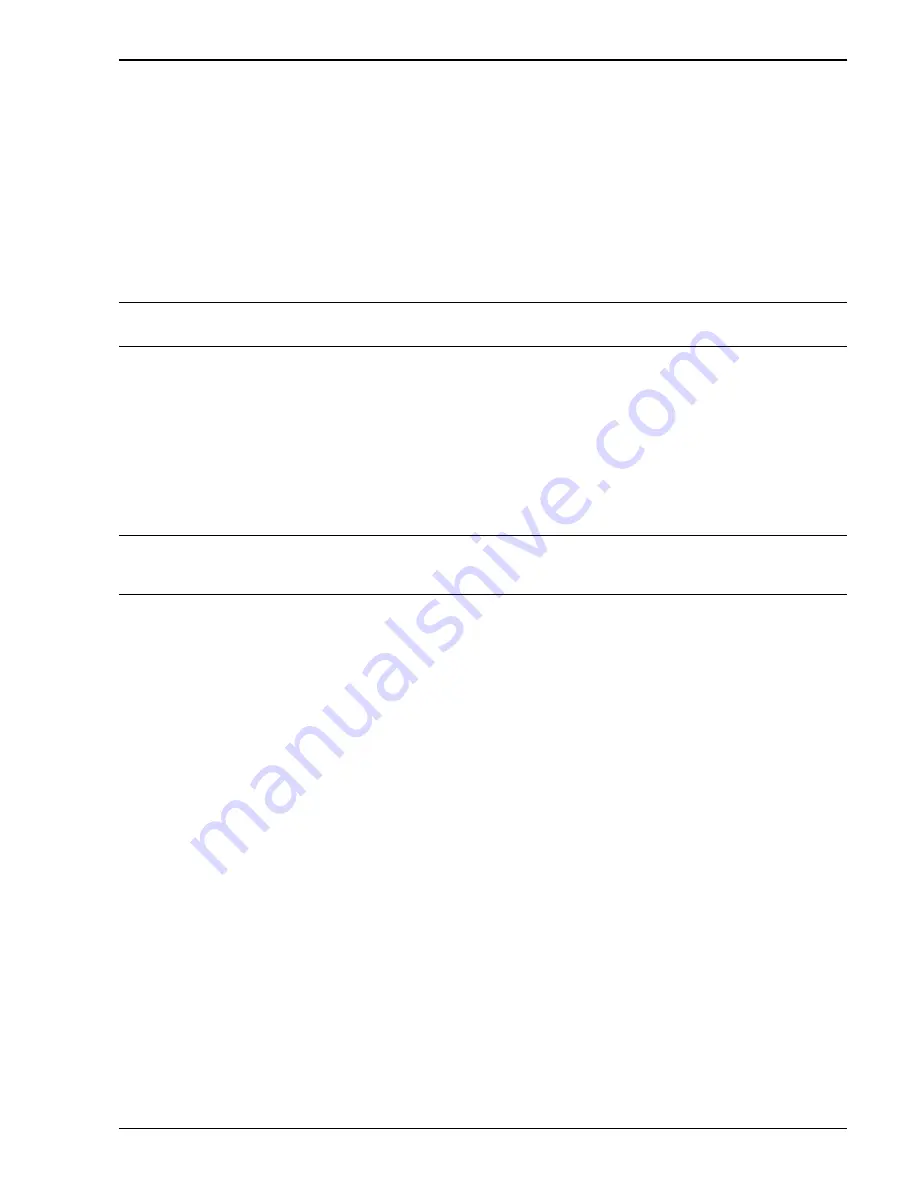
Proline Promass 40E
Hauser
17
Limiting flow
See information in the "Measuring range" section
→
4
Select nominal diameter by optimizing between required flow range and permissible pressure loss. See
the "Measuring range" section for a list of maximum possible full scale values.
• The minimum recommended full scale value is approx. 1/20 of the max. full scale value.
• In most applications, 20 to 50% of the maximum full scale value can be considered ideal
• Select a lower full scale value for abrasive substances such as fluids with entrained solids (flow
velocity <1 m/s (< 3 ft/s)).
• For gas measurement the following rules apply:
– Flow velocity in the measuring tubes should not be more than half the sonic velocity (0.5 Mach).
– The maximum mass flow depends on the density of the gas: formula
→
4
.
Pressure loss
To calculate the pressure loss, use the
Applicator
sizing tool (
→
36).
System pressure
It is important to ensure that cavitation does not occur, because it would influence the oscillation of the
measuring tube. No special measures need to be taken for fluids which have properties similar to water
under normal conditions. In the case of liquids with a low boiling point (hydrocarbons, solvents,
liquefied gases) or in suction lines, it is important to ensure that pressure does not drop below the
vapor pressure and that the liquid does not start to boil. It is also important to ensure that the gases
that occur naturally in many liquids do not outgas. Such effects can be prevented when system pressure
is sufficiently high.
Therefore, the following locations should be preferred for installation:
• Downstream from pumps (no danger of vacuum)
• At the lowest point in a vertical pipe
Thermal insulation
Some fluids require suitable measures to avoid loss of heat at the sensor. A wide range of materials can
be used to provide the required thermal insulation.
Heating
Some fluids require suitable measures to avoid heat transfer at the sensor. Heating can be electric, e.g.
with heated elements, or by means of hot water or steam pipes made of copper or heating jackets.
!
Note!
• If using an electric trace heating system whose heating is regulated via phase angle control or pulse
packages, influence on the measured values cannot be ruled out due to magnetic fields (i.e. for values
that are greater than the values approved by the EN standard (sine 30 A/m)). In such cases, the
sensor must be magnetically shielded.
The secondary containment can be shielded with tin plates or electric sheets without preferential
direction (e.g. V330-35A) with the following properties:
– Relative magnetic permeability
μ
r
≥
300
– Plate thickness d
≥
0.35 mm (d
≥
0.014")
• Information on permitted temperature ranges
→
13.
Special heating jackets, which can be ordered separately from Hauser as an accessory, are
available for the sensors.