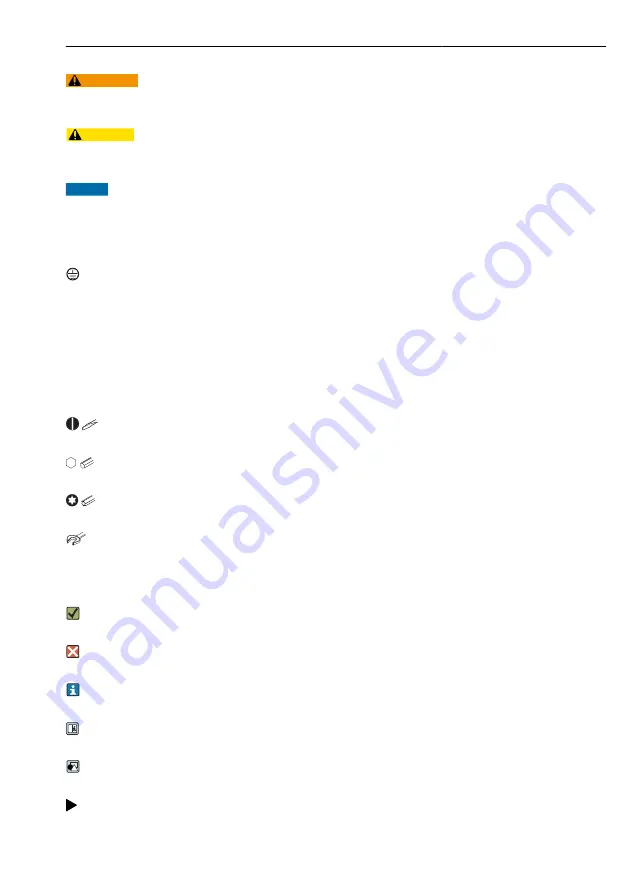
Levelflex FMP51, FMP52, FMP54 PROFIBUS PA
About this document
Hauser
3
WARNING
This symbol alerts you to a dangerous situation. Failure to avoid this situation can result in
serious or fatal injury.
CAUTION
This symbol alerts you to a dangerous situation. Failure to avoid this situation can result in
minor or medium injury.
NOTICE
This symbol contains information on procedures and other facts which do not result in
personal injury.
2.1.2
Electrical symbols
Protective earth (PE)
Ground terminals that must be connected to ground prior to establishing any other
connections.
The ground terminals are located on the inside and outside of the device.
• Inner ground terminal; protective earth is connected to the mains supply.
• Outer ground terminal; device is connected to the plant grounding system.
2.1.3
Tool symbols
Flat-blade screwdriver
Allen key
Torx screwdriver
Open-ended wrench
2.1.4
Symbols for certain types of information and graphics
Permitted
Procedures, processes or actions that are permitted
Forbidden
Procedures, processes or actions that are forbidden
Tip
Indicates additional information
Reference to documentation
Reference to graphic
Notice or individual step to be observed