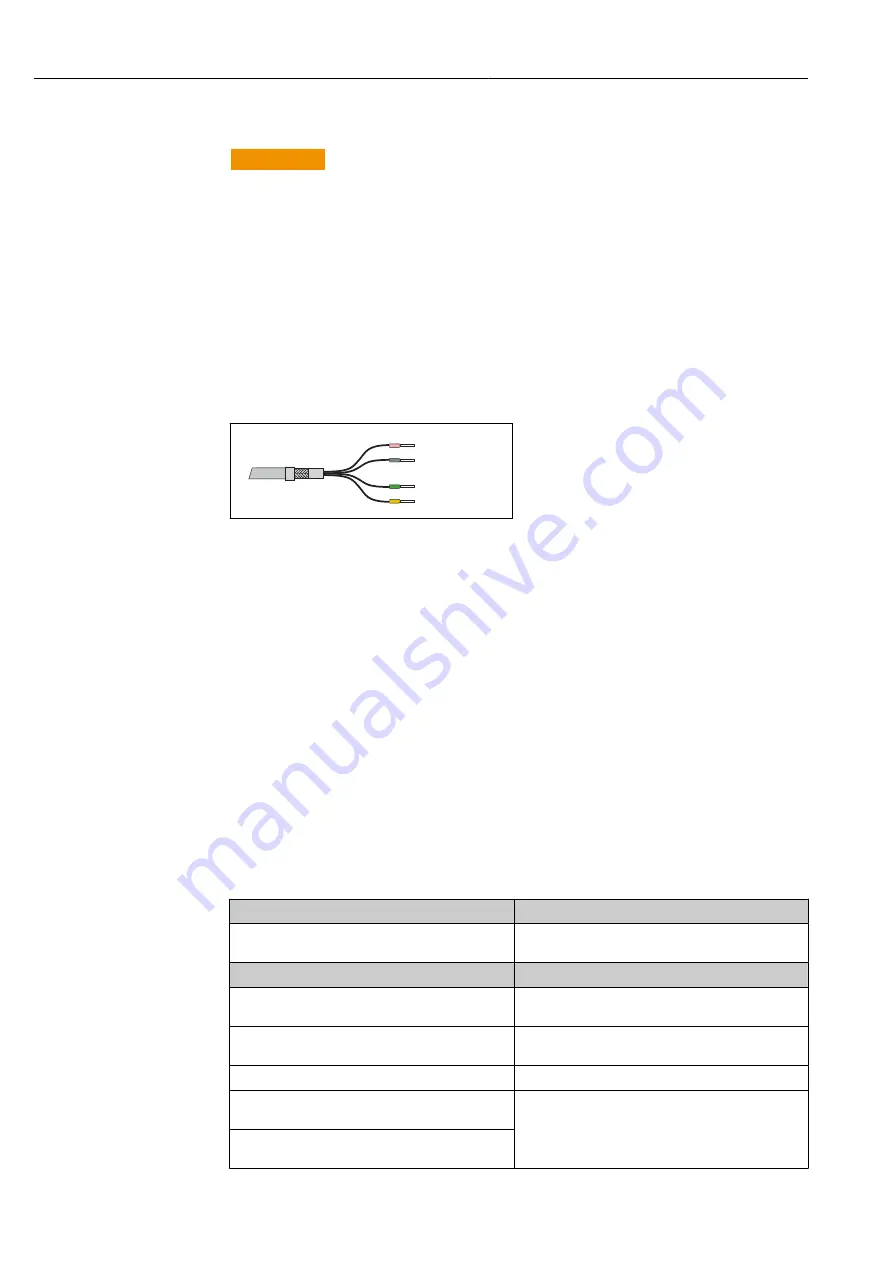
Electrical connection
Oxymax COS61D
20
Hauser
6
Electrical connection
L
WARNING
Device is live!
Incorrect connection may result in injury or death!
‣
The electrical connection may be performed only by an electrical technician.
‣
The electrical technician must have read and understood these Operating Instructions
and must follow the instructions contained therein.
‣
Prior
to commencing connection work, ensure that no voltage is present on any cable.
6.1
Connecting the sensor
Connection data
Sensor cable connected directly to the terminal connector of the basic module of the
transmitter
GN
PK
GY
YE
COM A
COM B
U
+
U
–
12
Sensor fixed cable with terminated cable cores
Optional: sensor cable plug connected to the M12 sensor socket of the transmitter
With this type of connection, the transmitter is already wired at the factory.
6.2
Ensuring the degree of protection
Only the mechanical and electrical connections which are described in these instructions
and which are necessary for the required, designated use, may be carried out on the device
delivered.
‣
Exercise care when carrying out the work.
Otherwise, the individual types of protection (Ingress Protection (IP), electrical safety, EMC
interference immunity) agreed for this product can no longer be guaranteed due,
for example to covers being left off or cable (ends) that are loose or insufficiently secured.
6.3
Post-connection check
Device condition and specifications
Action
Are the sensor, assembly or cables free from damage
on the outside?
‣
Perform a visual inspection.
Electrical connection
Action
Are the mounted cables strain-relieved and not
twisted?
‣
Perform a visual inspection.
‣
Untwist the cables.
Is a sufficient length of the cable cores stripped, and
are the cores positioned in the terminal correctly?
‣
Perform a visual inspection.
‣
Pull gently to check they are seated correctly.
Are all the screw terminals properly tightened?
‣
Tighten the screw terminals.
Are all cable entries mounted, tightened and leak-
tight?
‣
Perform a visual inspection.
In the case of lateral cable entries:
‣
Point cable loops downward so that water can drip
off.
Are all cable entries installed downwards or mounted
laterally?
Summary of Contents for Oxymax COS61D
Page 36: ...Technical data Oxymax COS61D 36 Endress Hauser Interface Memosens protocol...
Page 37: ...Oxymax COS61D Appendices Endress Hauser 37 14 Appendices...
Page 38: ...Appendices Oxymax COS61D 38 Endress Hauser A0044703...
Page 41: ......
Page 42: ......
Page 43: ......