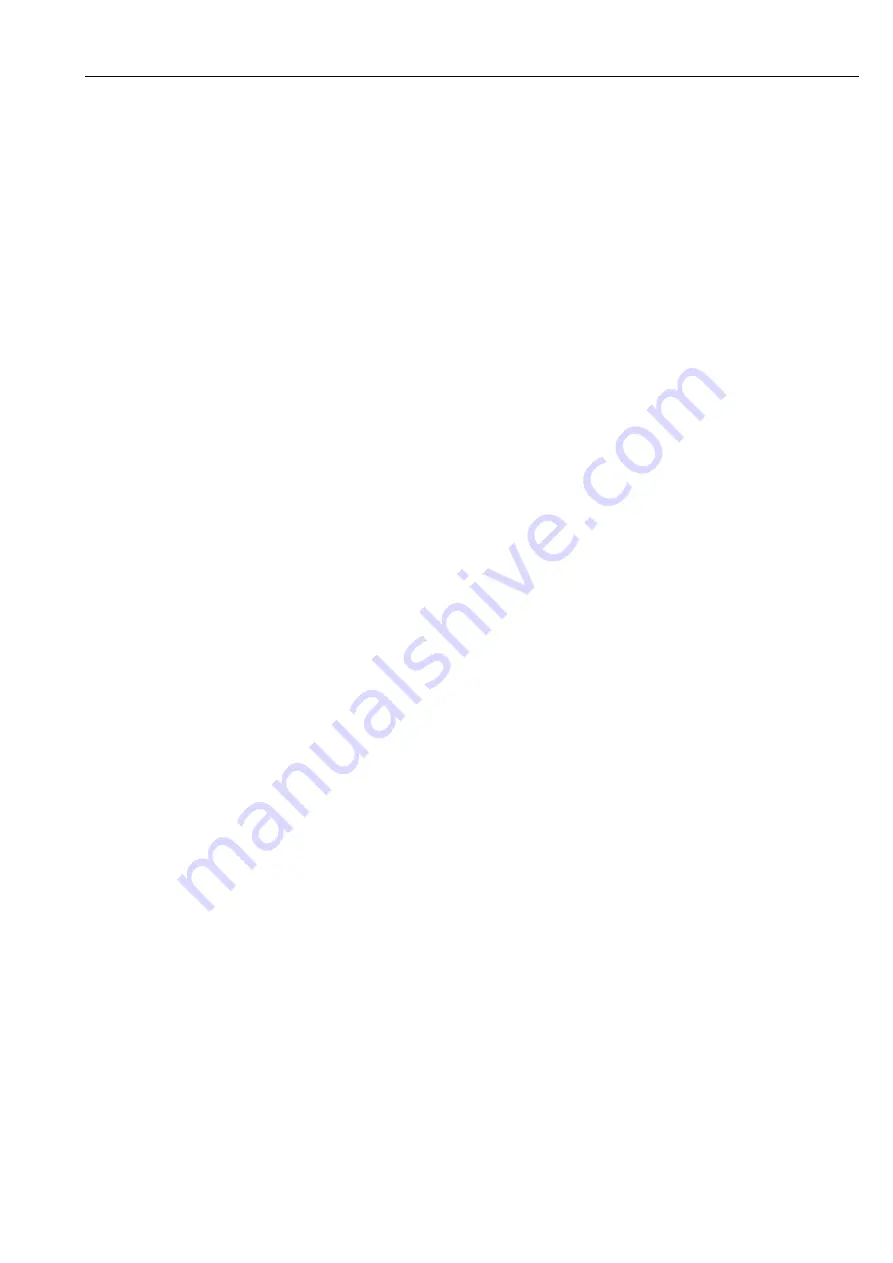
Cleanfit W CPA450
Operation
Hauser
17
4.3
Assembly operation
#
Warning!
• Do not try to insert or retract the assembly manually at a process pressure above 2 bar (29 psi)! If
the process pressure is higher, you have to switch off the process before moving the assembly!
• Never loosen the compression fitting at process pressures above 2 bar (29 psi)!
Moving from "service" position to "measuring" position
1.
Loosen the compression fitting with the hook wrench.
2.
Open the ball valve.
3.
Push the immersion tube into the process until stopping at the setting collar.
4.
Lock the immersion tube by tightening the compression fitting with the hook wrench. This
prevents the assembly from inadvertently returning to the "service" position.
Moving from "measuring" position into "service" position
1.
Securely hold the immersion tube. Failure to do so could cause the immersion tube to move
suddenly, possibly causing injury.
2.
Carefully loosen the compession fitting with the hook wrench by ¼ to ½ revolution.
3.
Pull the immersion tube out of the process until it stops ("service" position).
4.
Close the ball valve (if the assembly is installed correctly, the hand lever is horizontal).
5.
Perform the necessary service tasks.