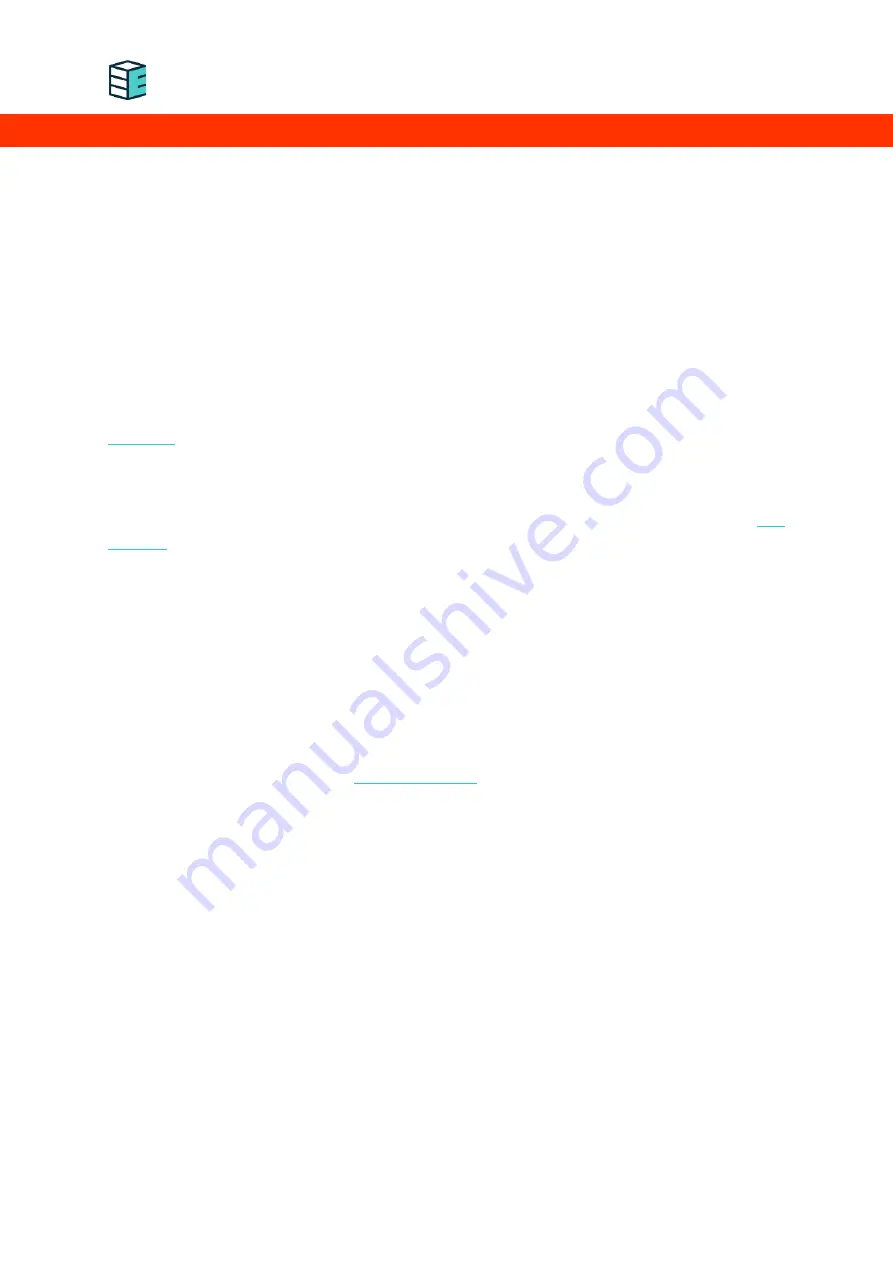
VE RS I ON
D O CU MEN T TI TLE
RE LEAS E DAT E
03
EL
–
Owner’s Manual
2022-04-29
EL
–
Owner’s Manual –
Rev.04
–
April 2022
40
This is a draft manual, technical specifications are subject to change
6.
ENAPTER MONITORING TOOLS
The device can be monitored and controlled remotely by authorised users by
logging into Enapter’s
cloud services on a web browser (https://cloud.enapter.com/login).
The device comes with a preinstalled UCM (Universal Communication Module), to monitor and manage
the device. Various sensor data from the devices is stored in the Enapter Cloud in a time-series database
and provides real-time or on-demand visualisation of collected data on customisable dashboards. To
support the latest protocols and security fixes, the UCM can be updated over-the-air.
Every device can be directly integrated with the Enapter Software-Defined EMS (Energy Management
System). The UCM inside the device connects either directly to the Enapter Cloud, or via an Enapter
Gateway which readies your device for Industry 4.0
–
to find out more, please visit the Enapter
Any user of Enapter products can now integrate a wide range of devices and analogue inputs into the
hydrogen production environment. System data of integrated devices is read continuously and is then
securely transmitted to the cloud, which can be accessed from anywhere in the world via the
or with the Enapter mobile application.
After the setup of the device is finished, it can be managed via the mobile or web dashboard, which
includes Automated Control and Monitoring functionality by customisable logic of the Enapter Rule
Engine (requires an Enapter Gateway on the site).
6.1
MOBILE APPLICATION
Enapter’s mobile application makes the installation of any energy system quick and easy.
If any part of
the hydrogen system encounters an issue, the mobile app can send push notifications to alert the
operator. This functionality is available via Wi-Fi or mobile network, all over the world.