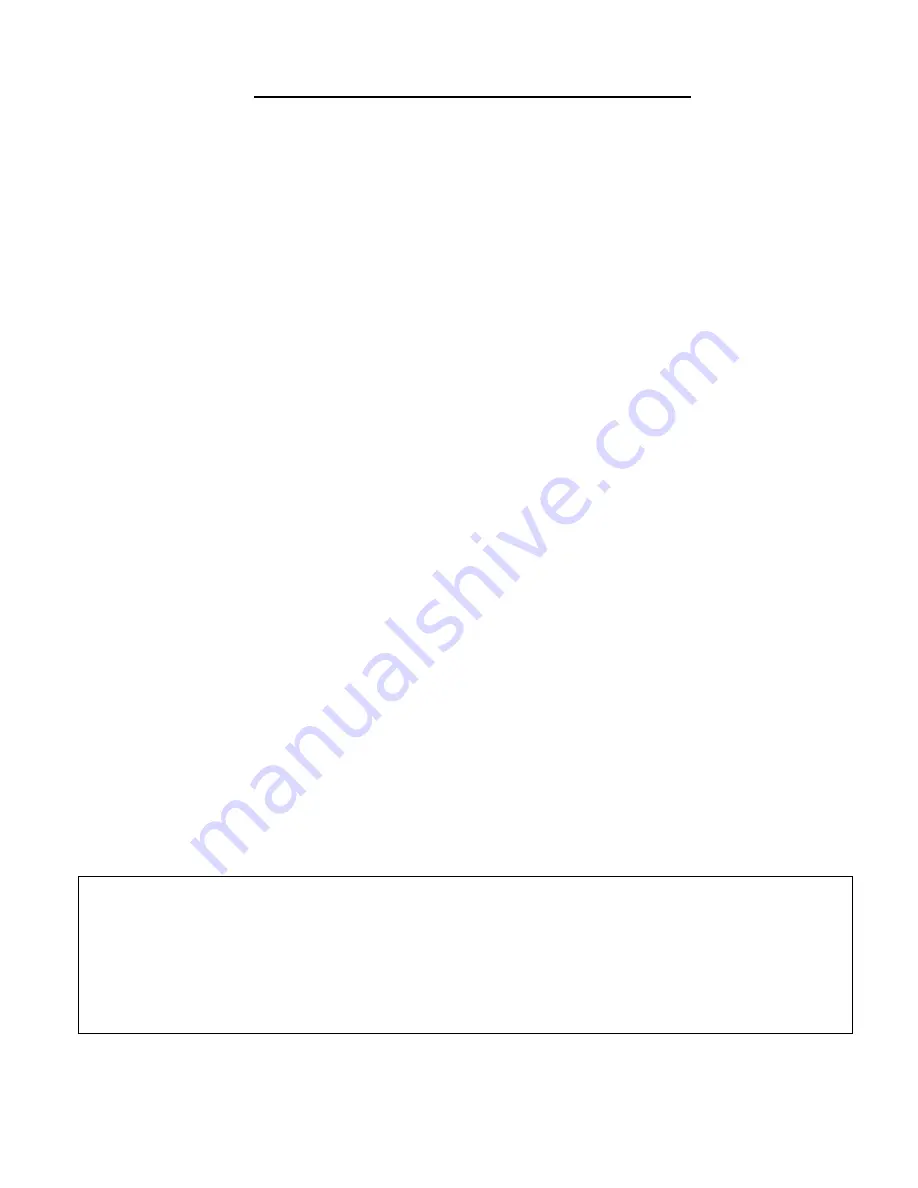
ROTARY MACHINE SAFETY RULES
•
EMT-7R machine should be DISCONNECTED from power source
before servicing.
•
Never place any part of the body including loose clothing near or
onto the rotating rolls. (KEEP HANDS AWAY). Failure to follow
this procedure will lead to personal body injury.
•
Never clean forming rolls while they are rotating.
•
Do not exceed specified material capacity of the machine.
•
Machine must be operated by authorized personal who have been
trained in regards to working and safety features of the machine.
All operators must read and understand the Operators Manual.
•
Never operate machine with any guards removed.
•
Do not use machine if service is required.
•
Use safety glasses and required protective equipment.
•
Keep work areas clean and in proper order.
It is the responsibility of the owner of this machine and shop supervisor to ensure that all operators of
this machine are properly trained on the safe operation of this machine and to require that this manual
including the above Safety Rules are read by all machine operators prior to operating.
If any of the EMT-7R safety labels are missing from the machine or damaged, it is the owner’s
responsibility to contact Empire Machinery & Tools Ltd. immediately for replacement labels. See
sample labels – OVER -)
Summary of Contents for EMT-7R
Page 6: ......
Page 7: ...EMT 7R Parts Breakdown ...
Page 8: ......
Page 9: ......
Page 10: ......
Page 11: ......
Page 22: ...Electrical Schematics for Air Oil Hydraulic Package EMPIRE EMT 7R PIPE FORMER ...
Page 23: ...UNIVERSAL EMT 7 ...
Page 24: ...UNIVERSAL EMT 7 ...
Page 25: ...UNIVERSAL EMT 7 ...
Page 26: ...UNIVERSAL EMT 7 ...
Page 27: ......
Page 28: ......
Page 37: ......
Page 46: ......