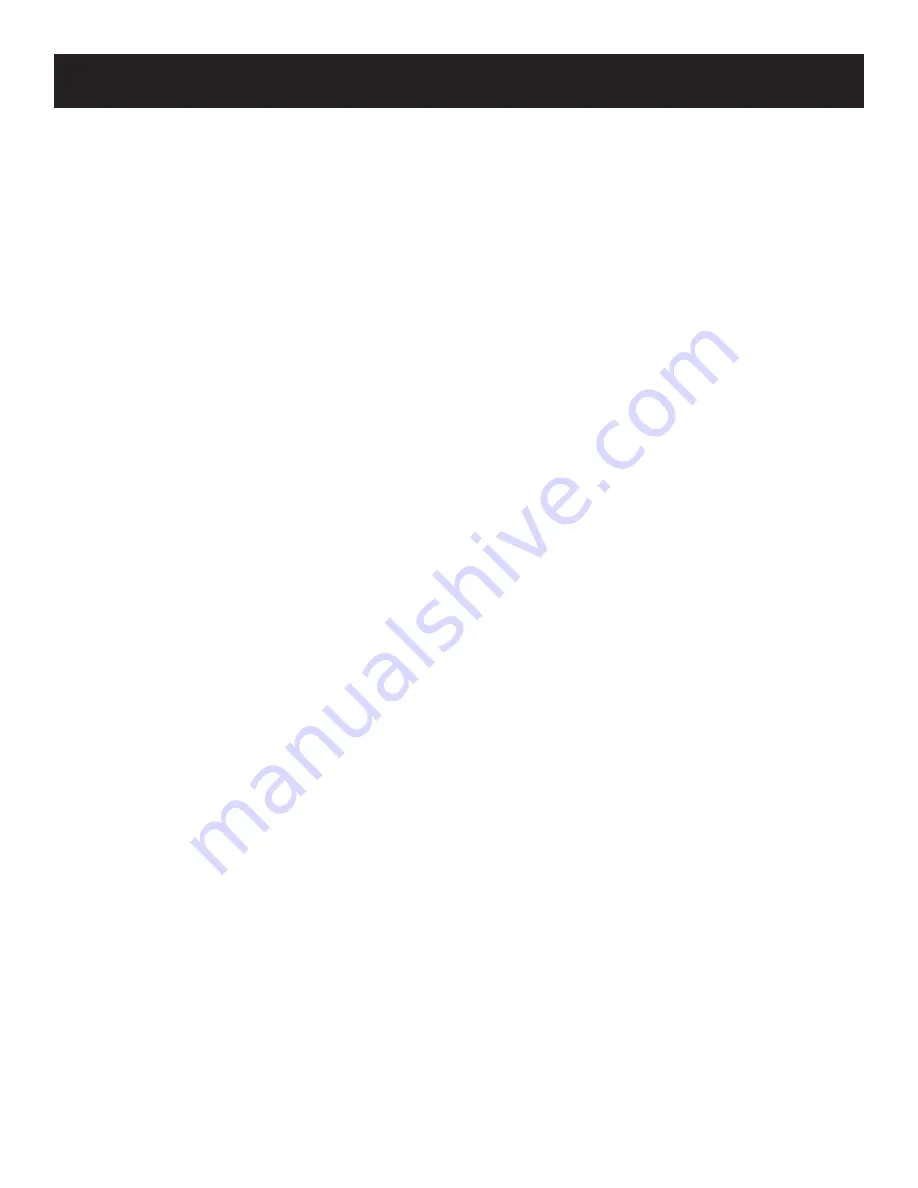
29083-0-0811
Page 5
INTRODUCTION
•
When the appliance is connected to a fixed piping system,
the installation must conform with local codes, or in the ab-
sence of local codes with the
National Fuel Gas Code, ANSI
Z223.1/NFPA 54
, or
International Fuel Gas Code
.
•
When installed, the appliance must be electrically grounded
in accordance with local codes, or in the absence of local
codes with the
National Electrical Code, ANSI/NFPA 70
, if
applicable.
•
Solid fuels shall not be burned in this appliance.
•
The maximum gas inlet supply pressure is 13" for LP and
10.5" for NAT.
•
For appliances for fixed fuel piping system and equipped
with an appliance gas pressure regulator, the required mani-
fold pressure in inches water column: 10" for LP and 3.5"
NAT.
•
For appliances for fixed fuel piping system and equipped
with an appliance gas pressure regulator, the appliance and
its individual shutoff valve must be disconnected from the
gas supply piping system during any pressure testing of that
system at test pressures in excess of 1/2 psi (3.5 kPa).
The appliance must be isolated from the gas supply piping
system by closing its individual manual shutoff valve during
any pressure testing of the gas supply piping system at test
pressures equal to or less than 1/2 psi (3.5 kPa).
For an appliance designed for use with a non-disposable self-
contained LP-gas supply system:
•
Propane cylinders may be acceptable for use with the ap-
pliance provided they are compatible with the appliance
retention means.
•
LP-gas supply cylinder must be constructed and marked
in accordance with the
U.S. Department of Transportation
(D.O.T.) Specifications for LP-Gas Cylinders
, or the
Stan
-
dard for Cylinders, Spheres and Tubes for Transportation
of Dangerous Goods and Commission, CAN/CSA-B339
as
applicable.
•
LP-gas supply cylinders between 4 and 40 pounds must
have an overfill prevention device.
•
LP-gas supply cylinder must have a connection device com-
patible with the connection of the appliance.
•
If the appliance is equipped with a CGA No. 600 Cylinder
Connection Device, the cylinder must be disconnected when
the appliance is not in use.
•
If appliance is to be permanently connected to a gas piping
system from a remote supply tank, installation must be in ac-
cordance with local codes or, in the absence of local codes,
with the
National Fuel Gas Codes ANSI Z223.1/NFPA 54.
Enclosures for LP-gas supply cylinders shall be ventilated by
openings at the level of the cylinder valve and at floor level. The
effectiveness of the opening(s) for purposes of ventilation shall
be determined with the LP-gas supply cylinder(s) in place. This
shall be accomplished by one of the following.
a. One side of the enclosure shall be completely open; or
b. For an enclosure having four sides, a top and a bottom:
1. At least two ventilation openings at cylinder valve
level shall be provided in the side wall, equally
sized, spaced at 180 degrees (3.14rad), and unob-
structed. Each opening shall have a total free area
of not less than 1/2 square inch per pound (2.3 sq.
cm/kg) of stored fuel capacity and not less than a
total free area of 10 square inches (64.5 sq. cm).
2. Ventilation opening(s) shall be provided at floor
level and shall have a total free area of not less
than 1/2 square inch per pound (3.2 sq. cm/kg) of
stored fuel capacity and not less than a total free
area of 10 square inches (64.5 sq. cm). If ventila-
tion openings at floor level are in a side all, there
shall be at least two openings. The bottom of the
openings shall be at floor level and the upper edge
no more than 5 inches (127 mm) above the floor.
The openings shall be equally sized, spaced at 180
degrees (3.14 rad) and unobstructed.
3. Every opening shall have minimum dimensions so
as to permit the entrance of a 1/8 inch (3.2 mm)
diameter rod.
•
Cylinder valves shall be readily accessible for hand opera-
tion. A door on the enclosure to gain access to the cylinder
valves is acceptable, provided it is non-locking and can be
opened without the use of tools.
•
There shall be a minimum clearance of 2 inches (51 mm)
between the lower surface of the floor of the LP-gas supply
cylinder enclosure and the ground.
•
The design of the appliance shall be such that (1) the LP-gas
supply cylinder(s) can be connected, disconnected and the
connections inspected and tested outside the cylinder en-
closure; and (2) those connections which could be disturbed
when installing the cylinder(s) in the enclosure can be leak
tested inside the enclosure;
Cleaning Instructions
This appliance is built using mostly high-grade stainless steel to
resist rust-through. In outdoor applications, all stainless steel will
develop a dull patina and, depending on the local environment
and on the materials used in the installation, may develop some
surface oxidation (rust). This does not affect the performance
of the firebox, and does not require any action to correct. If you
prefer keeping your firebox front looking factory-fresh, clean it as
required with stainless steel cleaner.
When installation application includes highly acidic applications
such as mortar or stone etching, do not remove the protective
PVC film from the stainless steel until after this application is
complete. Once the film has been removed we recommend that
the appliance be cleaned with a stainless steel cleaner immedi-
ately.
Please note that areas where the film has been formed (corners,
hems, etc.) may require extra cleaning due to the properties of
the film. Ensure that all protective film has been removed from
the firebox prior to burning the appliance.