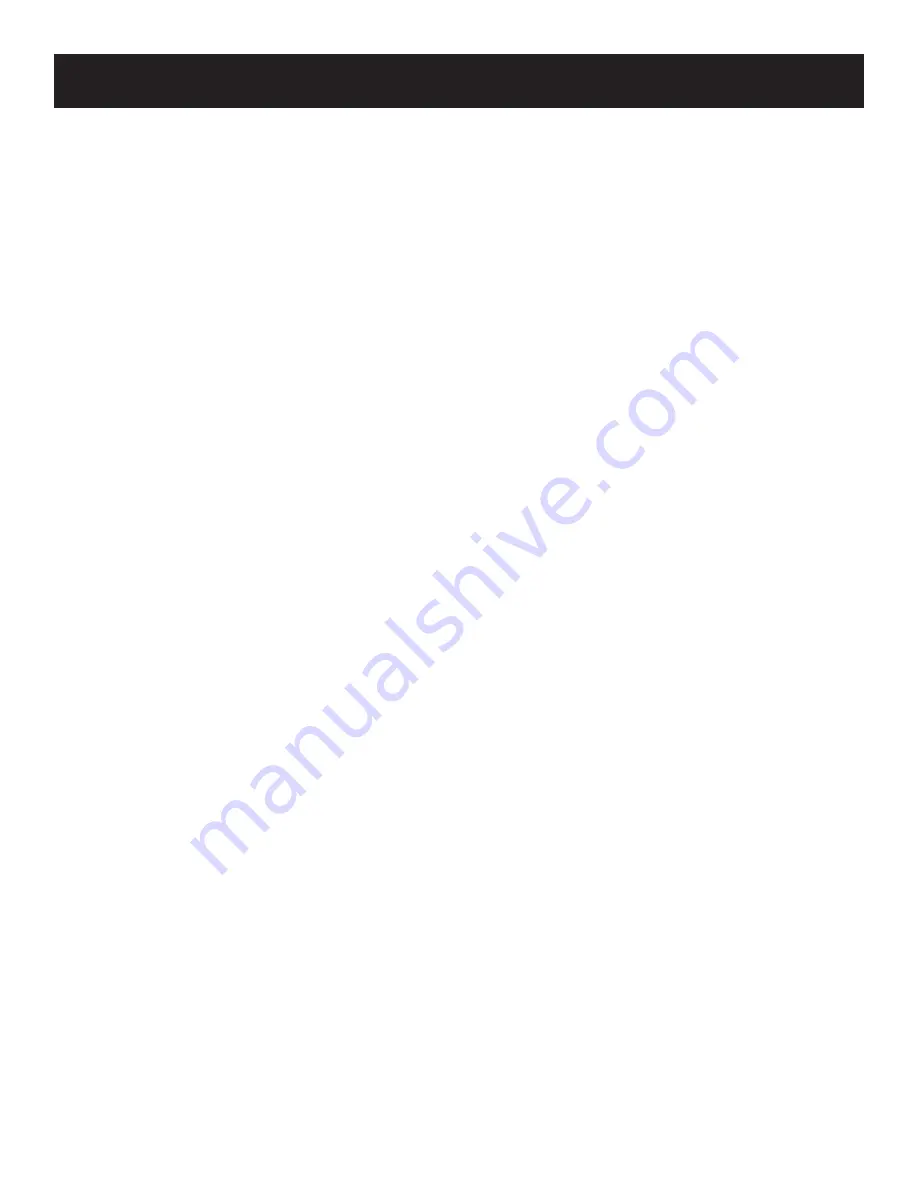
42603-4-0421
Page 39
1. Spark ignitor will not light pilot after repeated depressing
of piezo ignitor button.
a. Defective ignitor (no spark at electrode) - Check for spark at
electrode and pilot; if no spark and electrode wire is properly
connected, replace ignitor.
b. No gas or low gas pressure.
- Check remote shut off valves from stove. Usually there is
a valve near the main. There can be more than one valve
between the stove and main.
- Low pressure can be caused by a variety of situations
such as a bent line, too narrow diameter of pipe, or low line
pressure. Consult with plumber of gas supplier.
c. No Propane in tank.
- Check Propane tank. Refill tank.
2. Pilot will not stay lit after carefully following lighting
instructions.
a. Defective thermocouple.
- Check that pilot flame impinges on thermocouple. Clean
and/or adjust pilot for maximum flame impingement.
- Ensure that the thermocouple connection at the gas valve
is fully inserted and tight (hand tight plus 1/4 turn) faulty
thermopile if reading is below specified minimum.
- Disconnect the thermocouple from the valve, place one
millivolt meter lead wire on the tip of the thermocouple and
the other meter lead wire on the thermocouple copper lead.
Start the pilot and hold the valve knob in. If the millivolt
reading is less than 15 MV, replace the thermocouple.
b. Defective valve.
- If thermocouple is producing more than 15 millivolts, replace
faulty valve
3. Pilot burning, no gas to burner, valve knob "ON", on/off
switch "ON."
a. "On/Off" switch, wall switch, or wires defective.
- Check "on/off" switch and wires for proper connections.
Place jumper wires across terminal at switch - if burner
comes on, replace defective switch. If OK, place jumper
wires across switch wires at gas valve-if burner comes on,
wires are faulty or connections are bad.
b. Thermopile may not be generating sufficient milli-voltage.
- If the pilot flame is not close enough physically to the
thermopile, adjust the pilot flame.
- Be sure the wire connections from the thermopile at the
gas valve terminals are tight and the thermopile is fully
inserted into the pilot bracket.
- Check the thermopile with a millivolt meter. Take the
reading at TH-TP & TP terminals of the gas valve. The meter
should read 325 millivolts minimum, while holding the valve
knob depressed to the pilot position, with the pilot lit, and
the ON/OFF switch in the OFF position. Replace the faulty
thermopile if the reading is below the specified minimum.
-With the pilot in the ON position, disconnect the thermopile
leads from the valve. Take a reading at the thermopile leads.
The reading should be 325 millivolts minimum. Replace the
thermopile if the reading is below the minimum.
c. Defective valve.
- Turn valve knob to "ON." Place ON/OFF switch to "ON."
Check with millivolt meter at thermopile terminals. Millivolt
meter should read greater than 100 M.V. If the reading is
okay and the burner does not come, replace the gas valve.
d. Plugged main burner orifice.
- Check main burner orifice for blockage, clean main burner
orifice.
4. Frequent pilot outage problem.
a. Pilot flame may be too high or too low, or blowing (high),
causing pilot safety to drop out.
- Clean and adjust flame for maximum flame impingement
on the thermocouple. Follow lighting instructions carefully.
5. The pilot and main burner extinguish while in operation.
a. No Propane in tank.
- Check Propane tank. Refill fuel tank.
b. Inner vent pipe leaking exhaust gases back into system.
- Check for leaks.
c. Glass too loose, gasket leaks in corners after usage.
- Be certain glass assembly is installed correctly and tighten
corner.
d. Horizontal vent improperly pitched.
- The horizontal vent cap should slope down only enough
to prevent any water from entering the unit. The maximum
downwards slope is 1/4 inch.
e. Bad thermopile or thermocouple.
- Replace if necessary.
f. Improper vent cap installation.
- Check for proper installation and freedom from debris or
blockage.
6. Glass soots.
a. Flame impingement on logs.
- Adjust the log set so that the flame does not excessively
impinge on it.
7. Flame lifts off main burner.
a. Insufficient oxygen being supplied.
- Check to make sure vent cap is installed properly and free
of debris. Make sure that vent system joints are tight and
have no leaks.
- Check to make sure that no material has been placed at
the burner base.
- Be sure glass is tightened properly on unit, particularly on
top corners.
8. Doors open on their own.
a. Casting not level.
- Loosen front leveling bolts to elevate front of casting slightly
above the rear of casting.
With proper installation and maintenance, your new Direct Vent Stove should provide years of trouble-free service. If you do ex
-
perience a problem, refer to the Trouble Shooting Guide below. This guide will assist a qualified service person in the diagnosis
of problems and the corrective action to be taken.
MILLIVOLT TROUBLESHOOTING