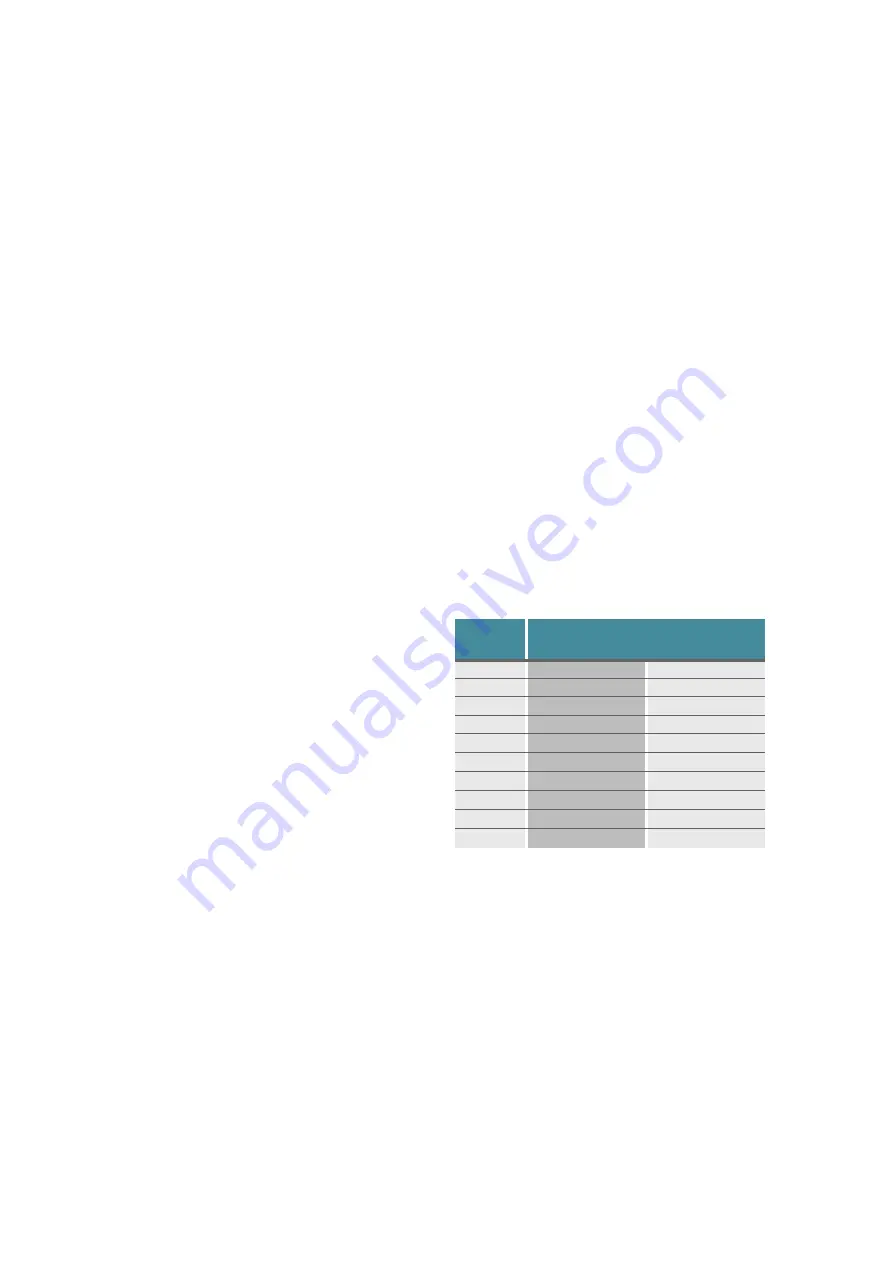
EMK
Operating and maintenance guidelines
3
Important for installations in wet internal conditions
or outdoors.
Please note that trouble free operation can only be en-
sured if all the measures set out below are carried out.
The motor terminal box is to be fitted so that the cable
entries are directed downwards.
Use suitable conduit screw fittings for the cable being
used and if necessary use reducing nipples.
Conduit screw fittings and plugs are to be coated with
sealing compound, tightened up securely and recoated.
Cable intakes are also to be made completely water-
tight.
The sealing surfaces of terminal boxes and termi¬nal
box covers are to be properly cleaned before reassem-
bly.
Gaskets are to be glued down on one face. Brittle gas-
kets are to be replaced!
When reassembling after maintenance work, etc. the
end shield centring spigots are also to be coated with
sealing compound.
The corrosion protection consists of a number of paint
coatings. Depending on environmental conditions the
paint coating must be renewed on a regular basis or
wherever necessary.
The electrical connection and maintenance of an elec-
tric drive may only be carried out by qualified electrical
personnel, who are conversant with the relevant regu-
lations. Similarly, the applicable accident prevention
regulations are to be adhered to.
Every EMZ motor is dispatched only after the specifi-
cations on the order have been checked, and a trial run
had been carried out. Until installed, the motor is to be
stored dry and in the same way as the mounting positi-
on. For longer stocked motors the insulated resistance
of every phase has to be measured to ground. It has to
be greater than 0,5 MΩ. For trouble free functioning,
proper installation and operation is essential.
Installation
The motor is to be installed according to its mounting
position and on an even and vibration-free base. The
shaft extensions up to 50 mm 0 have tolerances con-
forming to ISO k6 and above to ISO m6. Before fitting,
the rust inhibitor must be removed from the shaft end,
however, care must be exercised to ensure that no sol-
vent penetrates into the bearing. The motor shaft end
has been provided with a centre and a tapped hole, ac-
cording to the DIN specification 332 type D, which can
be used to pull on the transmission elements without
exerting harmful forces on the motor bearings.
Hammer blows and jolts are to be avoided at all times!
So as not to load the motor shaft excessively, the motor
and the driven machine are to be carefully aligned.
Operating and maintenance guidelines
EMK motors
»
EMK motors distinguish themselves...
Size
Torques (Nm)
Plastic
Metal
M12 x 1,5
1,5
8
M16 x 1,5
3,0
10
M20 x 1,5
6,0
12
M25 x 1,5
8,0
12
M32 x 1,5
10,0
18
M40 x 1,5
13,0
18
M50 x 1,5
15,0
20
M63 x 1,5
16,0
20
M72 x 1,5
-
28
M80 x 1,5
-
40