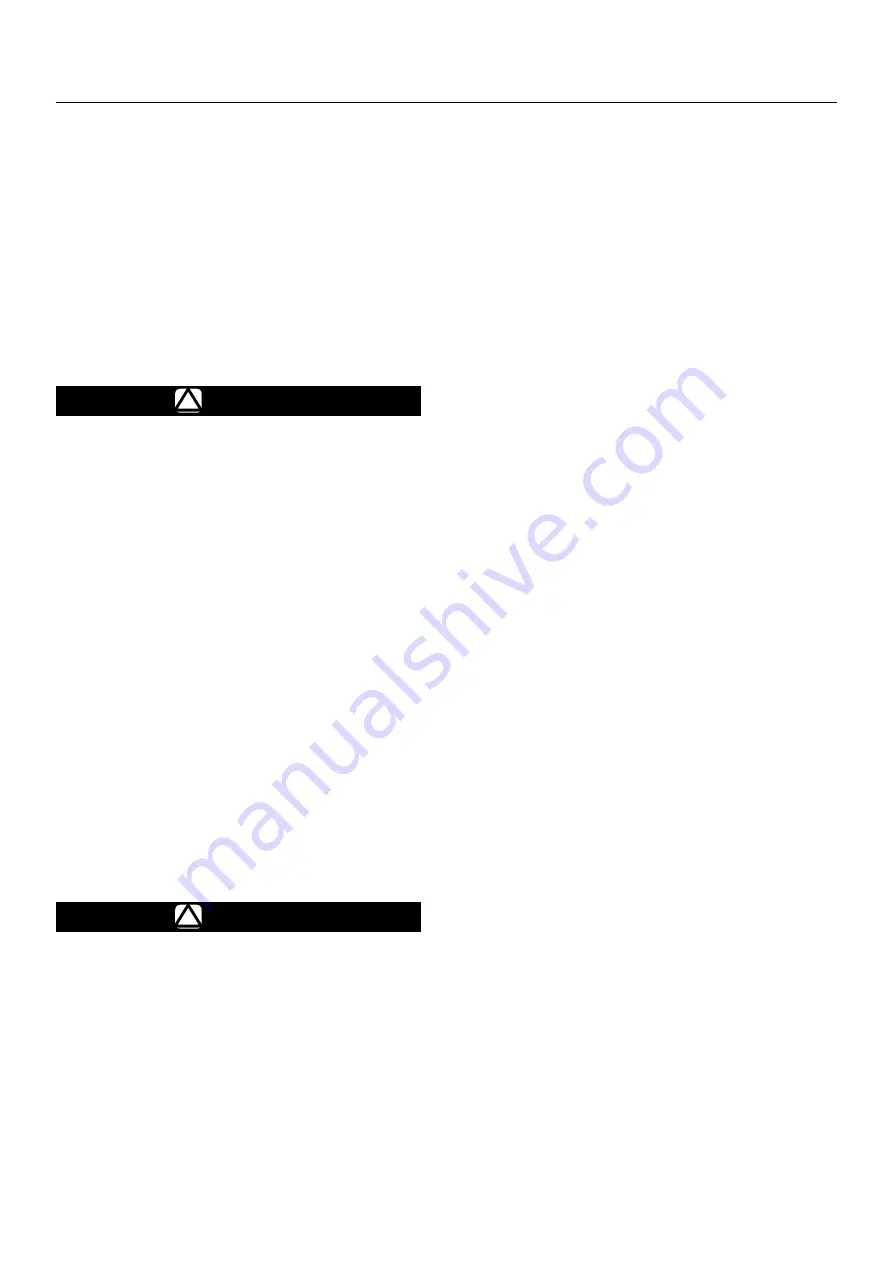
Europe,
Middle
East,
and
Africa
Only
Type FL
20
Reassembly
Lubricate the static O-rings with a thin layer of Molykote
55 M, be very careful not to damage the O-rings when
reassembling. No other pilot parts are to be lubricated.
Reassemble parts by reversing the above steps. As you
proceed, make sure that parts move freely and without
friction. In addition:
a. Once lever (key 36) and stem (key 12) have been
mounted, check that, with stem (key 12) against body
(key 19), clearance between forked stem (key 31) and
registered of lever (key 36) is 0.2 to 0.3 mm. If not, use
register to correct.
CauTION
The above clearance can be checked by
gently pulling the stem (key 12) upward.
Use the proper tool to make sure that
support of diaphragm (key 9) on the stem
(key 12) is on the same plane as that
supporting the diaphragm (key 9) in the body
(key 19).
b. Mount diaphragm (key 9) and screw on plate (key 8), first
by hand then with box wrench, always keep diaphragm
(key 9) firmly in place to avoid damage to stem (key 12) and
underlying levers.
c. Holding plate (key 8) firmly in place with box wrench,
tighten nut (key 7).
d. Before remounting cover (key 6), center diaphragm
as follows: mark a reference point (with pencil) on the
diaphragm; turn it to the right without forcing and mark
another reference on body. Now turn diaphragm to the
left and mark a further reference. Position the diaphragm
mark midway between the two marks on the body.
e. Tighten all screws uniformly to ensure proper sealing.
Calibration
See the paragraph Pilot Adjustment on page 12.
CauTION
The pilot has a wide range of self-adjustment
values. However, given actual operating
conditions, it may necessary to assist it
at times by finding the best setting of pin
screw/register (key 24) or the most suitable
calibration orifice (key 18).
BOOSTER vaLvE maINTENaNCE
TyPE V/31-1 (SEE FIGURE 25)
Overhaul booster valve when servicing monitor.
a. Remove cover (key 4) and replace pad (key 19),
diaphragms (keys 10 and 23) and O-ring (key 18).
b. When remounting, make sure that the tightening of the ring
nut (key 25) does not put undue stress on diaphragm
(key 23).
c. Set valve at no less than 5 mbar over monitor’s pilot
pressure value. Any value below this will result in a lower than
desired flow rate.
STaBILIzER FILTER maINTENaNCE
TyPE SA/2 (SEE FIGURE 26)
maintenance
Replacing Filter
a. Remove screws (key 2), cover (key 11); replace felt
(key 12) and O-ring (key 13). Reassemble in reverse
order the above sequence.
Replacing Stabilizer Diaphragm and Seal Pad
a. Remove cover (key 19); spring (key 1) and diaphragm
assembly (keys 21, 20, 3, 4, 18, and 17). Replace
diaphragm if necessary.
b. Unscrew seat (key 5), replace pad holder (key 15) and
O-ring (key 6).
c. Reassemble in reverse order the above sequence.
SPaRE PaRTS
Spare parts storage shall be done by proper procedures
according to national standard/rules to avoid over aging or
any damage.