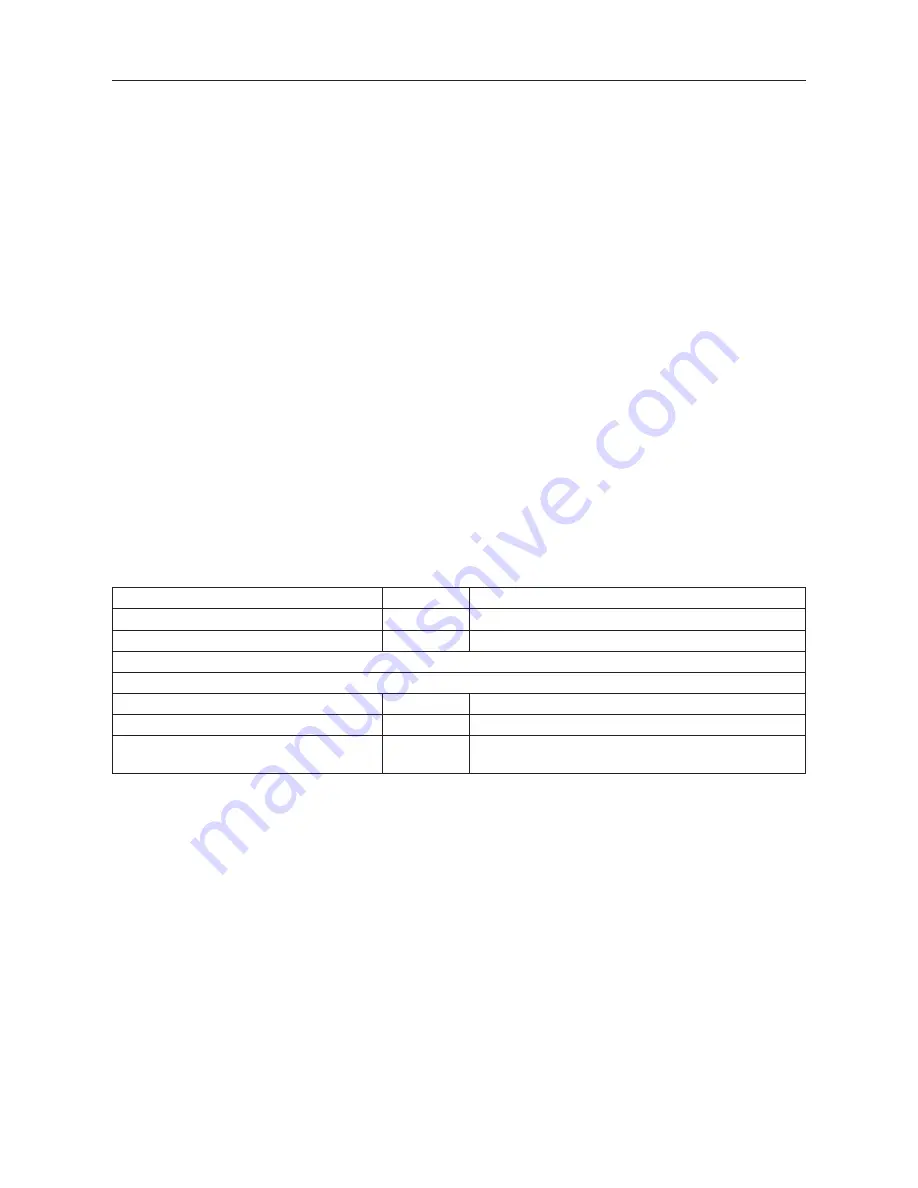
16
FieldQ
April 2017
Installation guide
DOC.IG.QC54.1 Rev.: 2
The QC54 module is suitable for use in a FISCO system in accordance with IEC 60079-11 : 2012 for use in
Zone 1 and 2 locations.
12.1 Fieldbus Intrinsically Safe Concept
The FISCO Concept allows the interconnection of intrinsically safe apparatus to associated apparatus not
specifically examined in such combination.
The criterion for such interconnection is that the voltage (Ui or Vmax), the current (Ii or Imax), and the
power (Pi), which intrinsically safe field devices can receive and remain intrinsically safe, considering faults,
must be equal to or greater than the voltage (Uo, Voc), the current (Io, Isc) and the power (Po) levels which
can be delivered by the associated power supply device considering faults and applicable safety factors.
In addition, the maximum unprotected capacitance (Ci) and inductance (Li) of each apparatus (other than
the terminators) connected to the Fieldbus must be less than or equal to 5 nF and 10 µH respectively.
In each I.S. Fieldbus segment only one active device, normally the associated apparatus, is allowed to
provide the necessary energy for the Fieldbus system. The voltage (Uo or Voc) of the associated apparatus,
used to supply the bus, has to be limited to the range of 14VDC to 24VDC.
All other equipment connected to the bus cable has to be passive, meaning that the apparatus is not al-
lowed to provide energy to the system, except to a leakage current of 50 µA for each connected device.
Separately powered equipment needs a galvanic isolation to insure that the intrinsically safe Fieldbus circuit
remains passive.
12.2 Cable parameters
The cable used to interconnect the devices needs to comply with the following parameters:
Loop resistance R
c
:
15 ...150
Ohm/Km
Inductance per unit length L
c
:
0.4…1
mH/km
Capacitance per unit length C
c
:
80 ...200
nF/km
C
c
= C
c
line/line + 0.5 C
c
line/screen, if both lines are floating or
C
c
= C
c
line/line + C
c
line/screen, if the screen is connected to one line
Length of spur Cable:
max. 60
m
Length of trunk cable:
max. 1
Km
Length of splice:
max. 1
m (T-box must only contain terminal connections
with no energy storage capability)
When the cable complies with IEC 60079-11, no further consideration of cable parameters is necessary. The
cable parameters may be determined in accordance with Annex C of IEC 60079-14.
12.3 Terminators
At both ends of the trunk cable, an approved line terminator with the following parameters is suitable:
- R
= 90 ...102Ohm
- C
= 0 ...2.2 µF
Note:
IEC 61158-2 requires an operational capacitance value of 0,8 µF to 1,2 µF.
The number of passive devices connected to the bus segment is not limited due to I.S. reasons. If the above
rules respected, up to a total length of 1000m (sum of trunk cable and all spur cables), the inductance and
capacitance of the cable will not impair the intrinsic safety of the installation.
12 FISCO Concept