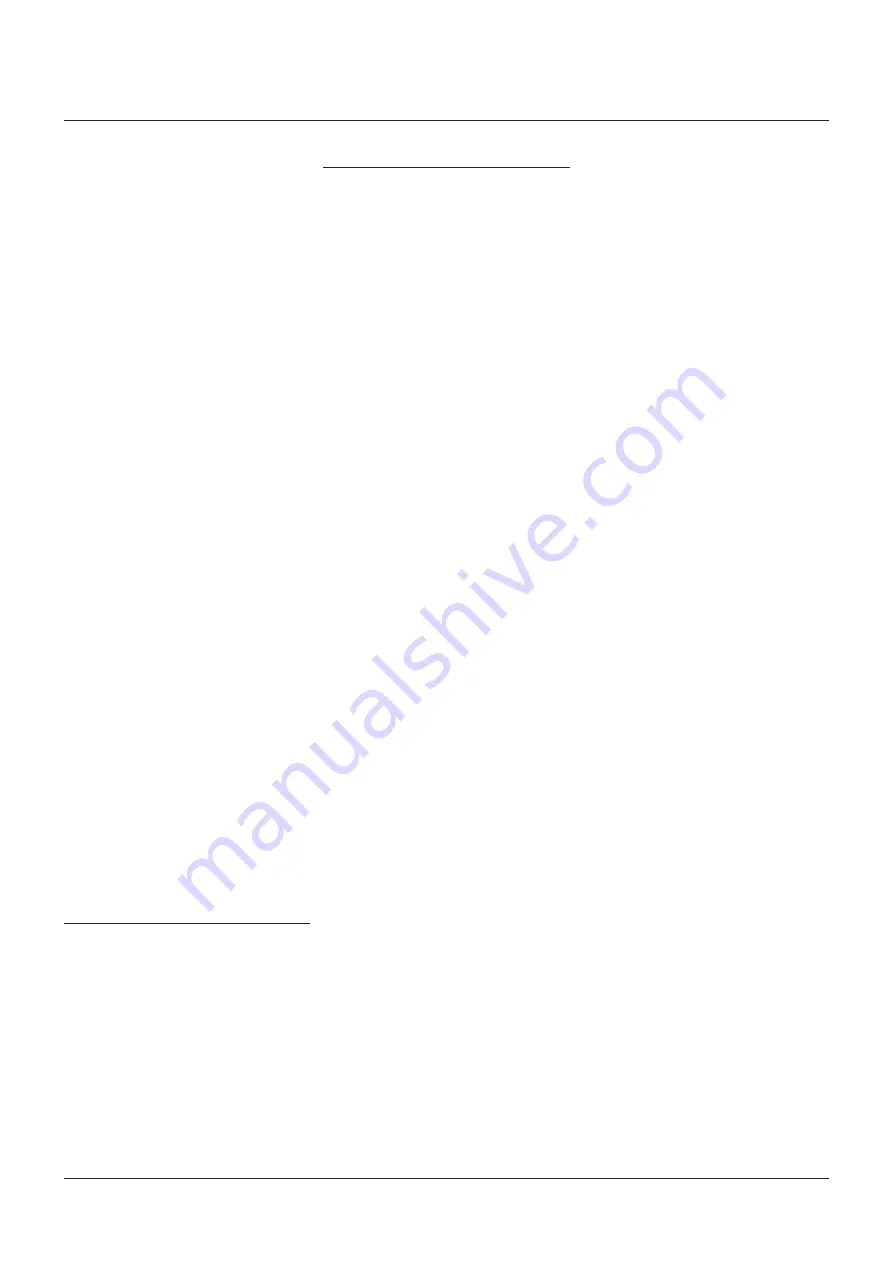
9
PENBERTHY
SERIES LC FLAT GLASS GAGES
INSTALLATION, OPERATION AND MAINTENANCE INSTRUCTIONS
9 DISPOSAL AT END OF USEFUL LIFE
Penberthy gages are used in a variety of fluid
applications. By following the appropriate
federal and industry regulations, the user
must determine the extent of preparation
and treatment the gage must incur before its
disposal. A Material Safety Data Sheet (MSDS)
may be required before disposal services
accept certain components.
Metal, glass and polymers should be recycled
whenever possible. Refer to order and
applicable technical data sheets for materials
of construction.
10 TELEPHONE ASSISTANCE
If you are having difficulty with your liquid level
gage, contact your local Penberthy distributor.
You may also contact the factory direct at
(956) 430-2500 and ask for an applications
engineer. So that we may assist you more
effectively, please have as much of the
following information available as possible
when you call:
∙ Model #
∙ Name of the company from whom you
purchased your liquid level gage
∙ Invoice # and date
∙ Process conditions (pressure, flow rates,
tank shape, etc)
∙ A brief description of the problem
∙ Trouble shooting procedures that failed
If attempts to solve your problem fail, you
may request to return your liquid level gage
to the factory for intensive testing. You must
obtain a Return Authorization (R.A.) number
from Emerson before returning anything.
Failure to do so will result in the unit being
returned to you without being tested, freight
collect. To obtain an R.A. number, the following
information (in addition to that above) is
needed:
∙ Reason for return
∙ Person to contact at your company
∙ 'Ship-to' address
There is a minimum charge for evaluation
of non-warranty units. You will be contacted
before any repairs are initiated should the cost
exceed the minimum charge. If you return a
unit under warranty, but it is not defective, the
minimum charge will apply.
6. Install shields, if used, and gasket on glass
being careful to keep components centered.
7. For transparent style gages, align studs
to accept liquid chamber and slide liquid
chamber into place being careful to keep
components centered.
8. For reflex style gages, install covers in place
while making sure alignment of components
is maintained with vision slot. Install
nameplate, washer and all nuts finger tight.
9. For reflex belleville style gages: install
nameplate and seven belleville washers
under each nut with pointed end toward the
nut (see Figure 2). Finger tighten nuts.
10. Using a torque wrench, tighten nuts in 5 ft·lb
(7 Nm) increments, following the sequence
in Figure 1 until the torque values shown in
Table 3 are reached.
Note:
depending on gage size there may be
less bolting than shown in Figure 1. Start at
the center and follow 'Z' pattern outward to
the limit of bolting on a specific gage.
11. For transparent style gages, install
gaskets and shields, if used, centered
on vision slots.
12. Install rubber band around each piece
of glass and cushion, then place glass
centered on gasket or shields, if used.
13. Install covers in place being careful to
maintain components alignment inside.
14. Install nameplate, washer and nuts to
studs. Finger tighten nuts.
14A. For transparent belleville style gages:
install nameplate and four belleville
washers under each nut with pointed
end toward the nut (see Figure 2). Finger
tighten nuts.
Note:
the following procedure is to be
done on only one side of the gage.
15. Using a torque wrench, tighten nuts in
5 ft·lb (7 Nm) increments, following the
sequence in Figure 1 until the torque
values shown in Table 3 are reached.
Refer to Section 5 for installation and Section 6
for operation of liquid level gage when
returning to service.