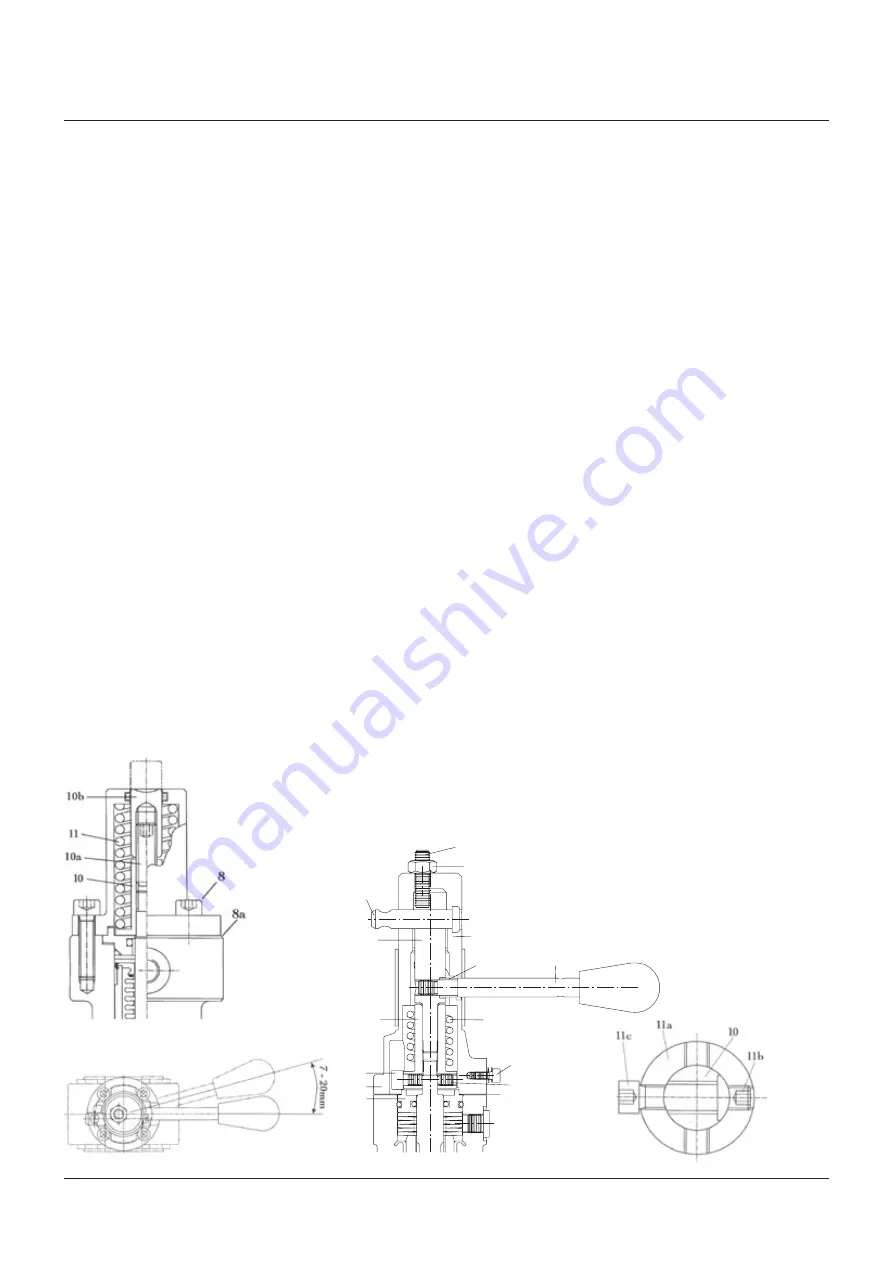
8
9e
9a
9b
10b
10c
10a
11
11c
9
7a
8a
10
11a
8
11b
Neotecha
Sapro Sampling DeviceS
Maintenance and RepaiR instRuctions
Figure 16
c) Bonnet re-assembly
1. Bayonet adaptor units only (spindle seal
type B) (See Fig. 16)
1.1. position gasket (8a) on valve body.
1.2. Screw spring support (10) onto the spindle
until finger tight, then back off by a quarter
turn.
1.3. position the coil spring (11) over the spring
support.
1.4. position the bonnet onto the valve body
over the coil spring and screw the two
threaded rods, from the spring tension
device in Tool kit Sv-W3, into opposing
holes in the valve body.
1.5. place the two-hole plate over the threaded
rods, followed by the washers and tighten
the bonnet onto the valve by means of
the wing nuts.
1.6. Screw two socket head screws (8) into
the two remaining bonnet/body holes and
tighten.
1.7. remove the spring tension device and
replace with two socket head screws (8).
Tighten all four screws to ensure full
compression of the coil spring.
1.8. Screw the position indicator (10b) lightly
onto the cap head screw (10a) through the
top of the bonnet, ensuring that it is finally
flush with the bonnet.
2. Bottle adaptor units only (spindle seal type A)
(See Fig. 17 and Fig. 18)
2.1. position the gasket (8a) on the valve body.
2.2. Screw the spring support (11a) onto
the spindle until contact is made with
the lantern ring (7a).
2.3. Screw the tie rod (10) into the spring
support until hand tight; then turn the tie
Note
ensure that the handlever has a lateral play
of minimum 7 mm and maximum 20 mm
(refer to Fig. 17).
if lateral play requires adjustment:
a. remove handlever and bonnet, as previously
described.
b. loosen the securing screw (11b) to free the spring
support from the spindle
c. rotate the spring support a quarter turn counter
clockwise and re-tighten securing screw.
d. rotate spindle assembly until the securing screw
is again aligned with the leak detection port.
e. repeat assembly from instruction (2.7).
Figure 18
closed
Figure 17
rod counter clockwise until the hole in the
tie rod is aligned with the next hole in the
spring support.
2.4. position the locating screw (11c) in the
spring support hole which is aligned with
the non-countersunk side of the tie rod
hole (See Fig. 19).
2.5. Fix the spring support to the spindle by
means of the securing screw (11b) in the
hole opposite the locating screw.
2.6. rotate the spindle assembly until the
securing screw is aligned with the leak
detection port in the valve body. (This port
has a yellow plastic blanking plug).
2.7. place the coil spring (11) over the spring
support (11a).
2.8. position the bonnet over the coil spring
ensuring that the locating screw (11c)
aligns with the key way in the bonnet.
2.9. applying hand pressure on the bonnet
to compress the coil spring, secure the
bonnet to the valve body using the cap
head screws (8).
2.10. Slide protective sleeve (10b) over bonnet.
2.11. locate the roller sleeve (10c) onto the
handlever and screw the handlever (10a/b)
into the tie rod (through the bonnet).
Figure 19
2.12. When lateral play is satisfactory, remove
the handlever and roller sleeve (10a/b/c).
2.13. Slide the protective sleeve (10b) into
position over the bonnet.
2.14. re-fit the roller sleeve to the handlever
and the handlever to the tie rod
(through the bonnet).
2.15. position the locking pin (9e) through the
bonnet. Try to operate the handlever
counter clockwise and check that the
spindle does not move off the valve seat.
2.16. Screw the set screw (9a) with hexagon nut
(9b) into the bonnet.