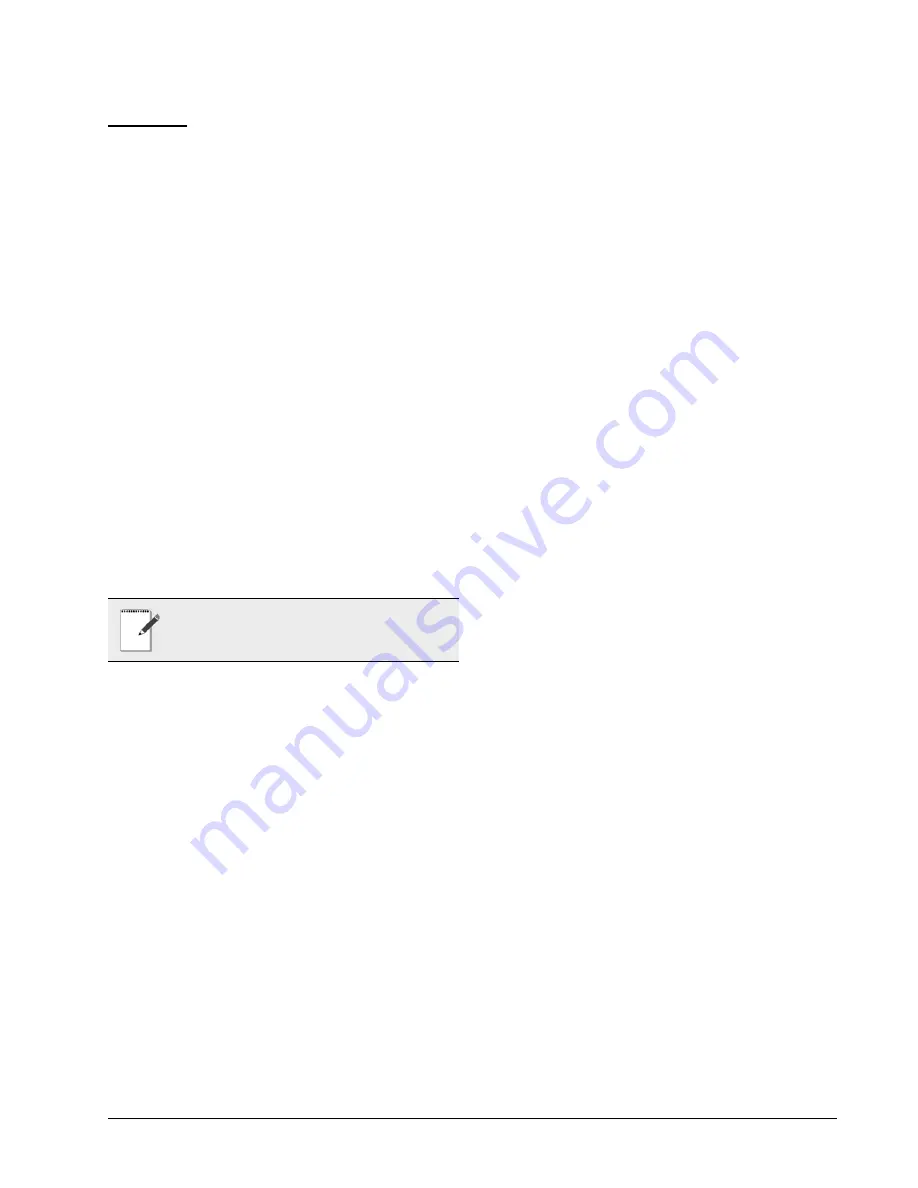
Step 1
Valve Zeroing • 12
Valve Mfg
If you have already associated the
valve and circuit, select the valve type in the
appropriate field. Press the F4 button to
choose the type of valve used. If this field is
set to
ECT Flow
,
the following options will
be available:
•
Stuck Valve alarm - the valve is not moving
in response to commands:
Based on characteristics for this valve type,
this feature offers a high probability that if
the valve becomes stuck, a Stuck Valve
alarm will be generated.
•
Open Wire alarm - at least one drive winding
of the valve is disconnected or has an open
coil (no current flow was detected).
•
Over Current alarm - available if the
Valve
Mfg
field is either set to
ECT Flow
or
Other
, the valve driver is reporting an over
current condition possibly caused by a
shorted driver winding.
7
Valve Zeroing
During the installation process of the valves or
when a valve is replaced, the valve(s) must be
zeroed before the MultiFlex ESR board can
begin controlling.
The zeroing process closes the valve twice the
number of Max Steps and should sufficiently
"zero" ECT valves. For Sporlan and other valve
manufacturers that have a full travel much
greater than Max Steps, this process may need to
be repeated one or two more times to fully zero
the valve. Once the valve has been zeroed, the
process will not need to be repeated unless the
valve has been replaced or driven open beyond
its control range by a device other than the Mul-
tiFlex ESR board. Note that if the valve manu-
facturer (
Valve Mfg
) is set to
Other
and the
valve harness becomes disconnected while the
MultiFlex ESR board is attempting to control,
zero the valve after the disconnect is resolved.
7.1.
Step 1
To zero the valve, first configure the Step Rate
and Max Step parameters for the valve type. The
configuration can be done with either the E2
controller or CPC’s hand-held terminal (HHT).
For the parameters to be configured with the E2,
the HHT must be unplugged and disconnected
from the MultiFlex ESR board.
The Max Step parameter is the total number of
control steps for the valve from 0-100%, but the
physical valve may have a step range that is sub-
stantially larger than the Max Step parameter.
This is why the valve must be zeroed at initial
start-up.
7.2.
Step 2
After the configuration of Step Rate and Max
Step parameters for the valve, disconnect the
power plug from the MultiFlex ESR board, then
reconnect the power plug to reapply power to the
MultiFlex ESR board. When power has been
reapplied to the board, all valves will begin to
close and the
Close
LED (located on the right
side under the valve connector on the MultiFlex
ESR board) will illuminate. After the valve
closes the Max Step parameter number of steps,
the valve will begin to open and the
Open
LED
(located on the left side under the valve connec-
tor on the MultiFlex ESR board) will illuminate.
The moment any
Open
LED illuminates, dis-
connect power from the board. Then reconnect
the power plug to reapply power to the Multi-
Flex ESR board.
8
Hand-Held Terminal
8.1.
Overview
The hand-held terminal (HHT) connector is
located on the lower left side of the board and is
NOTE: All alarms attempt to auto reset con-
tinuously every 10 minutes after the alarm was
first detected.
Summary of Contents for MultiFlex ESR
Page 1: ...026 1720 Rev 4 06 APR 2010 MultiFlex ESR Installation and Operation Manual ...
Page 2: ......
Page 4: ......
Page 21: ......