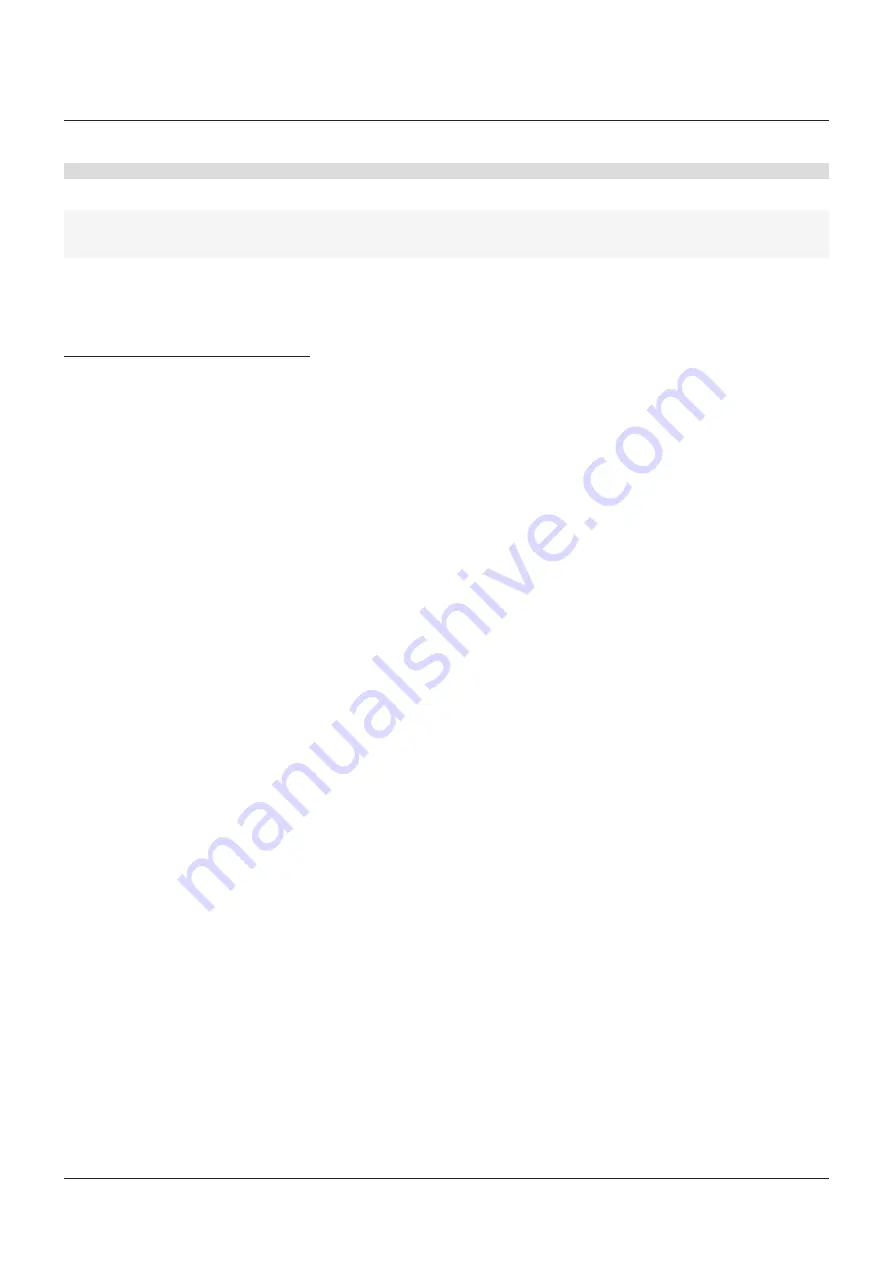
4
2.6 troubleshooting guide
symptom
Possible cause
resolution
valve would not rotate
actuator has failed
replace or repair
valve packed with debris
flush or clean valve to remove debris
valve leaking
valve not fully closed
Close valve
Debris trapped in valve
Cycle and flush (with valve open) to remove debris
seat is damaged
replace seat
Jerky operation
Debris trapped in valve
Cycle and flush (with valve open) to remove debris
air supply actuator inadequate
Increase air supply pressure and/or volume
3 maintenanCe
the Keystone butterfly valve Paraseal is
designed to require a minimum of maintenance.
3.1 routine maintenance
routine maintenance or lubrication is not
required other than periodic inspection to
ensure satisfactory operation and sealing. If
problems occur with valve pressure tightness
the seat can be replaced.
3.2 removing the valve
1. turn the disc to the nearly closed position.
(the disc is in line with the keyway in
the stem).
2. secure the valve with proper lifting
equipment and loosen all flange bolts and
remove the bolts, which prevent removing of
the valve.
3. spread the flanges width adequate tooling,
and remove the valve.
Warning
Depressurize and, if necessary in case of
dangerous fluids, drain the line and flush with
appropriate cleaning fluid before starting any
maintenance. Failure to do so may cause serious
personal injury and/or equipment damage.
Before disassembling the valve ensure the valve
has been decontaminated correctly from any
harmful gasses or liquids and that it is within a
safe temperature range for handling.
Personnel making any adjustments to the valves
should utilize suitable equipment.
All required personal protection means should
be worn.
Only personnel trained in all aspects of manual
and mechanical handling techniques must carry
out handling of all valves.
Keystone
Butterfly valves Paraseal
InstallatIon and maIntenance InstructIons
3.3 Valve disassembly
1. Place the valve on a horizontal support.
2. turn the disc to the full open position.
3. remove the actuation.
4. secure the disc with proper lifting
equipment.
5. remove the bottom plug or cover.
6. remove the nut of the thru-bolt at
bottom hub.
7. Mark the position of the bottom shaft and of
the driving shaft versus the disc.
8. Pull the driving shaft and belonging
thru-bolt out off body and disc. If required
use threaded hole in stemhead. support
shaft and disc during removal. It is possible
that also the shaft seal is removed.
9. remove bottom shaft. If necessary the
shaft can be pushed out with help of a bar
through the body driving shaft hole.
10. lift the disc out off the body.
11. Pull the lip of the seat out off the groove and
deform the seat to the shape of a heart and
remove the seat.
3.4 Valve assembly
1. Place the valve on a horizontal support.
Inspect correct position of bearings. for
some sizes a circlip should be mounted on
driving shaft and in disc bottom shaft hole.
2. Collapse the seat in the shape of a heart
perpendicular to the shaft holes. Pull the
seat lip over the edges and push the hubs
into the shaft holes. Divide the rubber
equally over the complete circumference.
3. Put some silicon grease on the inside of
the seat. especially on the circumferential
contact area between shaft and seat, the
shaft bearing and seat hole.
Pay attention!!
area between seat outside
and body inside should be free of grease.
4. lift the disc in vertical position (shaft holes
horizontal) leaving the shaft holes free.
5. let the disc descend into the seat until the
shaft holes of body and disc are exactly
in line.
6. Insert the bottom shaft in the initial position
as marked during disassembly. take care of
spline or key position if applicable.
7. Insert driving shaft with fixed thru bolt. Put
the shaft in the initial position as marked
during disassembly. Position of spline, key
or square should match exactly. look at
the mark on shaft and disc placed during
disassembly. When the shaft is ca 10 cm
before its landing surface the shaft seal
should be placed on the shaft top. for some
sizes a circlip should be mounted near
stemhead to lock up the seal.
8. Mount nut and ring on thru bolt at bottom
shaft side and tighten.
9. Place bottom plug or cover and tighten
screws.
10. remount the actuation and test valve