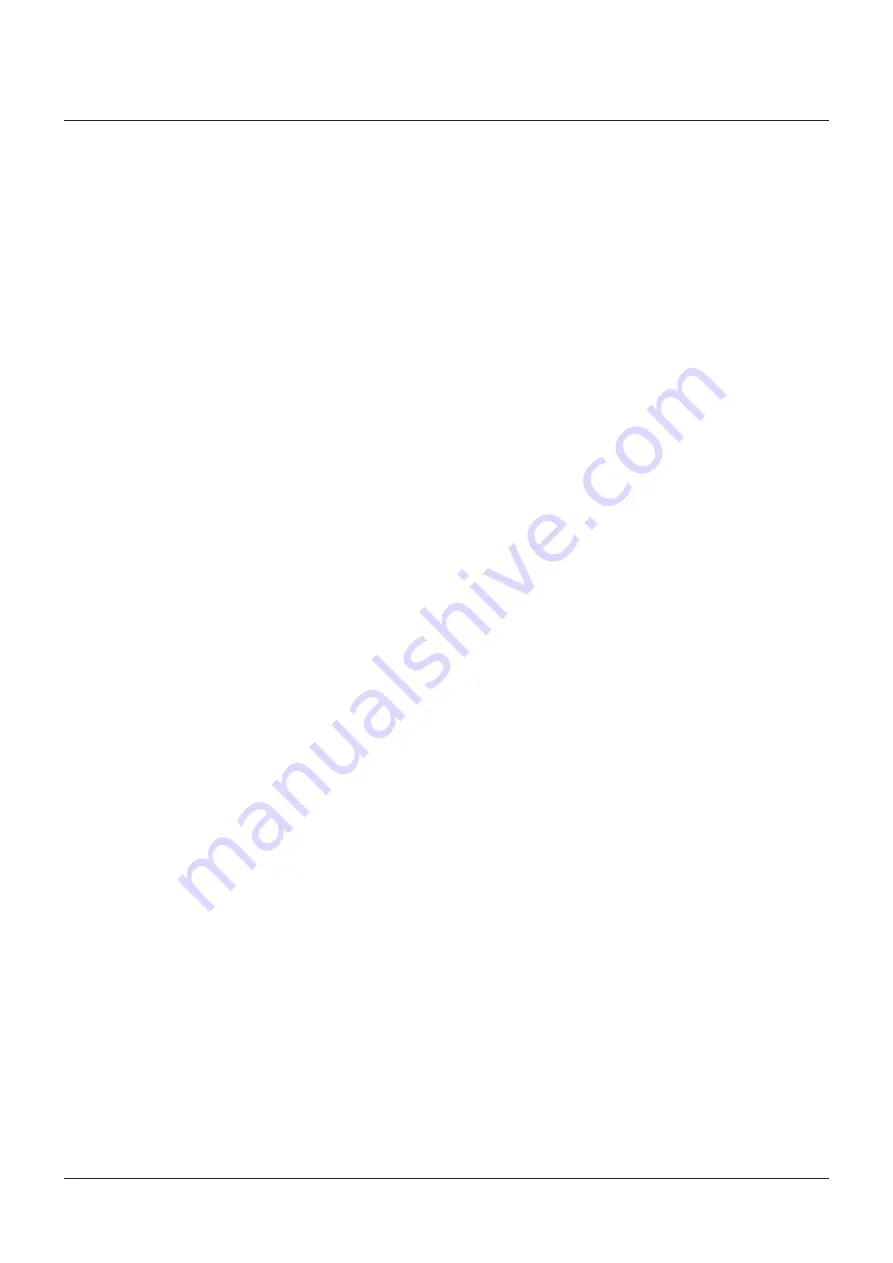
3
NOTES
• The valve can be installed in the pipe-line either with
or without the actuator mounted on top of the valve.
Make sure that you can turn the disc cautious so you
can feel a mismatch resulting from a disc touching
the adjacent piping.
• It is the responsibility of the valve user - and not the
valve manufacturer! - to ensure that the pipeline
system has been built professionally and the valve
has been properly installed.
• Adjacent piping must be positioned so that minimal
piping stresses are transmitted to the valve flanges
during or after installation.
• Handling and lifting of the valves during installation
MUST be performed following the same instructions
described in previous section ‘1.2 Handling’.
IMPORTANT
Mating flange faces should be in good condition
and free of dirt and/or inclusions. Both pipe
insides to be well cleaned.
3.3.1 Existing system (see sketch)
1. Check whether the flange distance
meets the valve face-to-face dimensions.
Spread with adequate tooling the flanges
for easy insertion of the valve.
2. In case of a wafer valve, insert some flange
bolts in the pipe flanges, to help you bear
the valve after insertion.
3. Close the valve so far, that the disc edge is
at least 10 mm within the body.
4. Insert the valve between the flanges, center
the valve body and insert all flange bolts.
Tighten the flange-bolts hand tight.
5. Slowly open the valve completely.
(The disc is in line with parallel flats or
keyway in stem head. Keyway points
towards disc edge).
6. Maintain the valve flange alignment while
gradually removing the flange-spreaders
and tighten the flange-bolts hand tight.
7. Slowly close and open the valve to check
for adequate disc clearance.
8. Cross-tighten all bolting to the proper
torque. Do not over tighten.
KEYSTONE
OPTISEAL F14/16 - 15/17 AND BREWSEAL BUTTERFLY VALVES
INSTALLATION AND MAINTENANCE INSTRUCTIONS
3.3.2 New system (see sketch)
1. With the disc in near-closed position center
each mating flange with the valve body.
Fix the body with some flange-bolts and
tighten the bolts.
2. Use the flange-valve-flange assembly
for fit-up and centering to the pipe.
3. Tack-weld the flanges to the pipe.
4. Remove the bolting and remove the valve
from between the flanges.
IMPORTANT
Do not finish-weld the flanges to the pipe with
the valve bolted between the flanges as this will
result in serious heat-damage to the seat.
5. Finish-weld the flanges to the pipe and
allow the flanges to cool completely.
6. Install the valve now according to the
procedure for installing in existing systems.
3.4 Valve verification
Check the operation of the valve by operating
it to ‘full open’ and ‘full close’. To verify the
valve operation, the disc position indicator
on the actuator or the handle should rotate
between the ‘full open’ and ‘full close’
indicators on the actuator or throttle plate.
Generally the valve disc travels clockwise
to close.